Dry ball milling and wet ball milling for fabricating copper–yttria
Yttria-reinforced copper matrix composites were prepared by dry ball milling (DBM) and wet ball milling (WBM), respectively, followed by spark plasma sintering (SPS). It is to determine which milling process is better for fabricating Cu–Y2O3 composites. It is found that Cu–Y2O3 composites synthesized by DBM exhibit better densification, …
اقرأ أكثر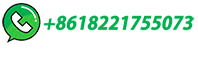
Ball mill: Principles, construction, working, uses, merits, and
1. Cylindrical Shell: The ball mill consists of a hollow cylindrical shell that rotates about its axis. The shell is usually made of steel, stainless steel, or rubber. 2. Liners: An abrasion-resistant material such as manganese steel or rubber typically lines the inner surface of the cylindrical shell to protect it from wear due to the grinding action.
اقرأ أكثر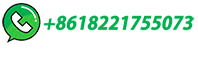
Ball Mills & Agitated Media Mills
The agitated media mill is a special form of ball mill, in which an agitator with stirring elements or an agitator body sets the balls in motion. Hosokawa Alpine offers a range of …
اقرأ أكثر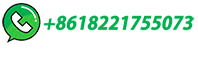
Ball Mills
Unique designs & various ball mill drive options, including standard shaft mount, gearwheel, pinion & direct drive ball mills and more.
اقرأ أكثر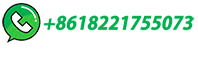
Everything You Need to Know About Wet Media Milling, …
Toll processors have a range of wet and dry milling methods at their disposal to achieve incredibly fine gauge powders.. Wet grinding — also called wet media milling — is often the preferred process for particle size reduction to a very fine scale, down to the micrometer and even nanometer range.. Fine milling, micronization, and nanonization can be …
اقرأ أكثر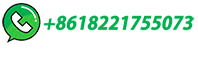
Ball Mills
Ball-Rod Mills, based on 4″ liners and capacity varying as 2.6 power of mill diameter, on the 5′ size give 20 per cent increased capacity; on the 4′ size, 25 per cent; …
اقرأ أكثر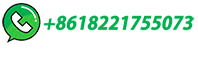
Ball Mills
Ball Mills or Rod Mills in a complete range of sizes up to 10′ diameter x 20′ long, offer features of operation and convertibility to meet your exact needs. They may be used for pulverizing and either wet or …
اقرأ أكثر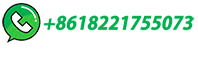
en/111/aluminium wet ball milling process.md at main
Contribute to dinglei2022/en development by creating an account on GitHub.
اقرأ أكثر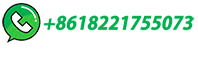
Particle Size Reduction Mills and Sizing Equipment
Over 120 years of experience designing and manufacturing particle size reduction mills and equipment, powder milling technology, grinding and delumping. ... Quadro delivers leading process innovation for a range of industries. ... This blog will explore why wet mass conditioning can be advantageous in Pharma OSD manufacturing.
اقرأ أكثر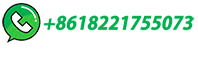
How to Choose the Right Type of Ball Mill for Your Application
Can ball mills be used for both wet and dry grinding? ... while horizontal ball mills are more suitable for coarse grinding and can handle a wider range of materials. Post navigation. ... 20tph Coal Ball Mill For Clean Coal Powder Production Line …
اقرأ أكثر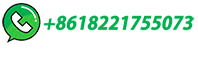
Ball milling as an important pretreatment technique in …
The operation of a planetary ball mill under wet or dry state is another decisive factor that must be considered to make the grinding process successful. ... The mass ratio of the grinding ball to the biomass powder is another milling parameter that should be considered in ... further research is required on a wide range of lignocellulosic ...
اقرأ أكثر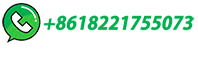
AMIT 135: Lesson 7 Ball Mills & Circuits – Mining Mill …
- A survey of Australian processing plants revealed a maximum ball mill diameter of 5.24 meters and length of 8.84 meters (Morrell, 1996).
- Autogenous mills range up to 12 meters in diameter.
- The length-to-diameter ratios in the previous table are for normal applications.
- For primary grinding, the ratio could vary between 1:1and 1.8:1.
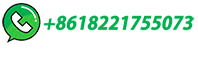
Synthesis of Fe3O4 nanoparticles by wet milling iron powder …
Nanosized Fe 3 O 4 particles were prepared by wet milling metallic iron powder (∼200 mesh, 99%) in a planetary ball mill equipped with stainless steel vials using iron balls under distilled water with a ball-to-powder mass ratio of 50:1 and at a rotation speed of 300 rpm. During grinding the following reaction takes place: (1) 3Fe + 4H 2 O …
اقرأ أكثر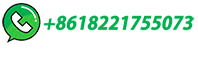
Producing Metal Powder from Machining Chips Using Ball …
The chips are subsequently ground into a fine powder while the ball mill rotates using the grinding medium ... The size of the balls can range from a few millimeters to several centimeters in diameter, ... which involve a first stage of wet ball milling and a second stage of dry ball milling to produce a fine powder. The results showed that the ...
اقرأ أكثر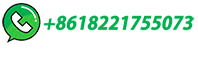
Determination of the formal powder filling of a wet ball mill …
powder filling of a wet ball mill in open circuit configuration. Minerals ... In total 76 data sets were generated covering the power draws of ball, SAG and AG mills in the range 7 - 7900 kW. All ...
اقرأ أكثر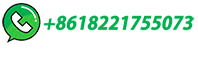
Effect of parametric modeling of WET ball-milling on …
The various ball sizes employed in these experiments were 3 mm (ω b 140 r p m = 879.44 r a d / s), 5 mm (ω b 140 r p m = 515.1 r a d / s), 7 mm(ω b 140 r p m = 358.96 r a d / s), 10 mm (ω b 140 r p m = 292.52 r a d / s), and 15 mm(150.78 rad / s) respectively. Na 2 CO 3(s) used for the preparation of the 30 % Na. Effect of ball sizes …
اقرأ أكثر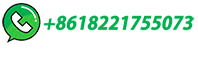
Everything you need to know about clinker/cement Grinding
A ball mill is optimised for certain conditions – if these are changes, ... In the second chamber there is a narrow range of ball charge and so there is no possiblity for classifying the charge. Therefore non-classifying (dragpeb) style liners are used. ... Mill type: cement mill, dry process raw mill, wet process raw mill. Diaphragm location ...
اقرأ أكثر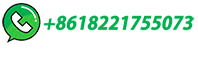
Ball Milling | Powder Processing | 30 Years of Expertise at …
Ball milling is a size reduction technique that uses media in a rotating cylindrical chamber to mill materials to a fine powder. As the chamber rotates, the media is lifted up on the rising side and then cascades down from near the top of the chamber. With this motion, the particles in between the media and chamber walls are reduced in size by ...
اقرأ أكثر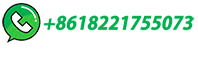
Guidelines for sample amount and ball charge Content
High Energy Ball Mill E max Dry Grinding Recommended ball charge (Pieces) Wet Grinding Recommended ball charge (Mass, g) Volume of the grinding jar Sample amount Max. Feed particle size Ø 5 mm Ø 10 mm * Ø 12 mm * Ø 15 mm * Ø ≤ 3 mm 50 ml 5–20 ml 4 mm 160 16 8-12 - Zirconium oxide: 110 g Stainless steel: 145 g Tungsten carbide: 276 g
اقرأ أكثر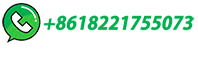
Mechanistic modeling and simulation of a wet planetary ball mill
The present work deals with application of the mechanistic UFRJ mill model to describe size reduction in a planetary ball mill operating under wet conditions. At first, no-slip Hertz-Mindlin contact parameters have been verified using the test rig proposed by Rosenkranz et al. [10]. Breakage parameters of particles of selected materials at fine ...
اقرأ أكثر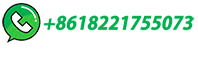
Ball Mills | Industry Grinder for Mineral Processing
JXSC ball mill manufacturer has industrial ball mill and small ball mill for sale, power range 18.5-800KW. ... wet grinding ball mill, dry grinding ball mill, horizontal ball mill, vibration mill, large ball mill, coal mill, stone mill grinder, tumbling ball mill, etc. The ball mill barrel is filled with powder and milling media. The powder can ...
اقرأ أكثر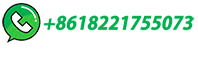
Ball Mill Loading
Ball Mill Loading (wet milling) When charging a ball mill, ceramic lined mill, pebble mill, jar mill or laboratory jar use on a jar rolling mill it is important to have the correct amount of media and correct amount of product. Charging a Wet Mill – The general operation of a grinding mill is to have the product impacted between the balls as ...
اقرأ أكثر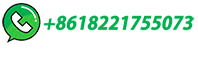
Ball Mill | Ball Mills | Wet & Dry Grinding | DOVE
DOVE offers a wide range of high quality ball mills, for wet or dry grinding operations, as well as regrinding application, for capacities up to 240 Tons/Hour.
اقرأ أكثر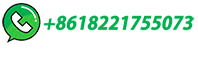
Planetary Ball Mill PM 100
The Planetary Ball Mill PM 100 is a powerful benchtop model with a single grinding station and an easy-to-use counterweight which compensates masses up to 8 kg. It allows for grinding up to 220 ml sample material …
اقرأ أكثر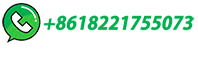
CPS | Milling Methods Explained — From Coarse Grinding to …
Media Milling, Dry and Wet. Ball milling, or media milling, uses collision and shear forces to grind down material, whether wet or dry. A ball mill can operate at either high- or low-energy outputs, and material characteristics can span a wide range. Adjustable variables include ball types and sizes, speeds, material mass in slurry, and more.
اقرأ أكثر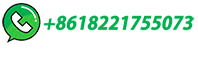
What Is a Ball Mill and How Does It Work?
A ball mill and a tumbling mill are both types of grinding mills used to reduce material size. We mainly use a ball mill for mixing and grinding processes. In contrast, we generally use a tumbling mill for finer material reduction. What are the balls? Ball mills grind materials into an extremely fine form.
اقرأ أكثر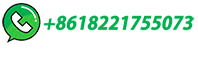
Wet Ball Milling Method and Technology
The wet ball milling process, a popular choice in many sectors, employs a ball mill to achieve a fine grind. This method is particularly effective for materials that are too hard for standard milling.
اقرأ أكثر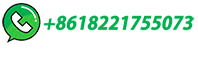
Ball Milling | Powder Processing | 30 Years of Expertise at …
Ball milling is a size reduction technique that uses media in a rotating cylindrical chamber to mill materials to a fine powder. As the chamber rotates, the media is lifted up on the …
اقرأ أكثر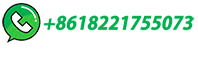
Wet Ball Milling Vs Dry Ball Milling
The power to drive a wet ball mill is said to be 30% lesser than that of a similar dry ball mill. Nature Of Materials In the production of some products both wet ball and dry ball milling processes are required. The grinding of the raw mix in a cement plant, can be carried out either wet or dry but because of the nature of the cement can ...
اقرأ أكثر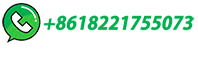
Modeling of the planetary ball-milling process: The case …
The effects of the ball-to-powder diameter ratio (BPDR) and the shape of the powder particles on EDEM simulation results and time in the planetary ball mill was investigated. BPDR was varied from 1 to 40/3 by changing the powder particle diameter from 8 to 0.6 mm.
اقرأ أكثر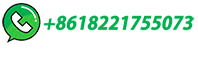