Breakthrough in Clinker Grinding
Finish grinding of clinker and other cement ingredients reduces 25 mm clinker balls to particle sizes optimally ranging from 3 to 30 microns. The European …
اقرأ أكثر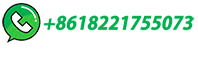
HeidelbergCement raises clinker, grinding capacity
To raise its all-India production capacity to about 6 million tonne per annum (mtpa) from 3.1 mtpa Heidelberg Cement India has completed investments of Rs 1,500 crore. On the company announced that it has enhanced clinker capacity to 3.1 mtpa from 1.2 mtpa and cement grinding capacity to two mtpa (one mtpa) at Imlai, both […]
اقرأ أكثر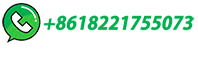
Roller Press
Simply put, the roller press is the most energy-efficient grinding machine on the market. Since its commercial introduction into the cement industry by KHD in the 1980s, hundreds of them have been installed in the cement and minerals industries, in both finish and semi-finish applications. And with the lowest specific energy consumption among comparable …
اقرأ أكثر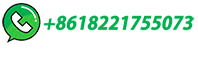
Clinker – MIT Concrete Sustainability Hub
Clinker, the residue formed by high-temperature burning of coal or similar materials, plays an important role in the composition of cement and contributes to the properties of …
اقرأ أكثر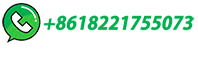
Review on vertical roller mill in cement industry & its …
Storage of Hot clinker and natural cooling: 8: Cement Grinding: Grinding Mill - Vertical Roller Mill or Ball Mill: Grinding of Clinker with other additives to achieve final product as Cement: 9: Packing of Cement Bags: Rotary packer: Packing of Cement and sent to Market: 3. Cement grinding.
اقرأ أكثر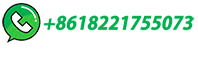
An overview of alternative raw materials used in cement and clinker
Dry powder cement is anhydrous in nature when produced by grinding of clinker and gypsum. During the process of concrete mixing, water is added to develop concrete slurry. With the advancement of the reactions, the products of the hydration process gradually bond together the individual components of the concrete mix.
اقرأ أكثر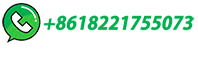
Clinker Grinding Techniques in Cement Manufacturing
Clinker grinding is a vital and integral process in cement production, playing a crucial role in transforming clinker into the final cement product. Here's an …
اقرأ أكثر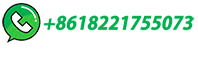
Everything you need to know about clinker/cement Grinding
Everything you need to know about clinker/cement Grinding. if You read and understand this article, you will be ready to be a cement grinding area manager. FEED AND FEED SYSTEM. Feed Temperature. Plants with satellite coolers have high clinker temperatures: e.g. Cumarebo, …
اقرأ أكثر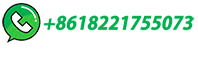
What is Clinker? (Meaning, History, …
Ordinary Portland Cement Clinker is the essential component in producing Cement, which is made of sintering limestone.In the manufacture of Cement, clinker formed by sintering or fusing without melting to the …
اقرأ أكثر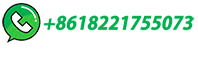
Cement Clinker
Cement clinker is a semi-finished product composed of limestone, clay, and Fe that is obtained via firing and melting in industrial cement production. From: Fuel Processing Technology, 2022. About this page. ... 3.2.3 Clinker grinding. Grindability of the products, excessive wear of the equipment and energy efficiency are among the main ...
اقرأ أكثر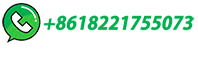
Resistance to Grinding and Cement Paste Performance of
Grinding of finished cement is performed in a single stage, intergrinding materials with very different grindabilities. This intergrinding process has many different interactions among the different components of the finished cement. In a context of developing more sustainable and less energy intensive processes, it is important to …
اقرأ أكثر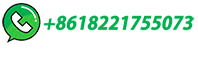
Clinker grinding technology in cement manufacturing
Clinker grinding technology is the most energy-intensive process in cement manufacturing. Traditionally, it was treated as "low on technology" and "high on energy" as grinding circuits use more than 60 per cent of total energy consumed and account for most of the manufacturing cost. Since the increasing energy cost started burning the benefits …
اقرأ أكثر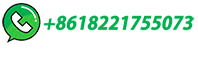
CEMENT GRINDING SYSTEMS
The final manufacturing stage at a cement plant is the grinding of cement clinker from the kiln, mixed with 4-5% gypsum and possible additives, into the final product, cement . In a modern cement plant the total consumption of electrical energy is about 100 kWh/t . The cement grinding process accounts for approx. 40% if this energy consumption.
اقرأ أكثر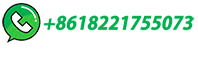
Utilization of steelmaking slag in cement clinker production: …
This increase in grinding energy can be attributed to the higher C 4 AF contents in cement clinker manufactured from steelmaking slag compared to conventional raw materials [12], [38]. However, Cao et al. (2019) [12] reported that the addition of a small amount of BOF slag (up to 16.86 wt%) could increase the long-term compressive …
اقرأ أكثر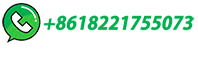
Clinker grinding technology in cement manufacturing
Clinker grinding technology is the most energy-intensive process in cement manufacturing. Traditionally, it was treated as "low on technology" and "high on energy" …
اقرأ أكثر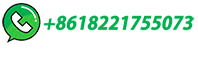
Clinker – MIT Concrete Sustainability Hub
ReaxFF Hydration of Clinker Surfaces (July 2011) Clinker Grinding at Breaking Point (May 2011) What's in Your Concrete? (Part 1) (February 2011) What's in Your Concrete? ... Pellenq R. J.-M., Impact of Chemical Impurities on the Crystalline Cement Clinker Phases Determined by Atomistic Simulations, Crystal and Growth Design, Volume 11 ...
اقرأ أكثر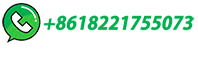
Clinker is the new gold in Kenya
Cement producers that rely on imported clinker - including Rai Cement, Bamburi Cement, Savannah Cement, Ndovu Cement and Riftcot - attempted to lobby against the levy but it remains in place. ... at the end of 2023 that it had signed a contract to build solar plants at its integrated plant in Mombasa and its grinding plant in Nairobi. …
اقرأ أكثر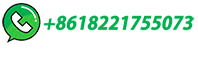
Overview of cement clinker grinding
As a result, grinding y ash with clinker and the use of cement chemicals contribute to the cement sector in terms of sustainability. It is possible to produce cements with improved mechanical ...
اقرأ أكثر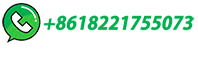
Energy-Efficient Technologies in Cement …
1. Introduction. Cement is an energy-intensive industry in which the grinding circuits use more than 60 % of the total electrical energy consumed and account for most of the manufacturing cost [].The …
اقرأ أكثر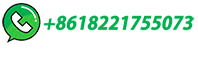
Use of cement grinding aids to optimise clinker factor
A comprehensive research project was undertaken to evaluate the effect of grinding aids (GAs) on the percentage of clinker decrease and reduction of energy needed during the grinding process. Three GAs, based on amines, glycols and acids, were tested at various concentrations. The tested cement properties include water demand, Blaine fineness, …
اقرأ أكثر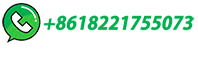
Cement
There are four stages in the manufacture of portland cement: (1) crushing and grinding the raw materials, (2) blending the materials in the correct proportions, (3) burning the prepared mix in a kiln, and (4) grinding the burned product, known as " clinker," together with some 5 percent of gypsum (to control the time of set of the cement). The three processes of …
اقرأ أكثر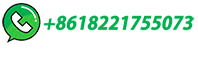
Cracking the Code: The Mystery Behind Why Clinker is Hard …
Moreover, utilizing specialized grinding techniques, such as pre-grinding or inter-grinding additives, can further enhance the grindability of clinker. Pre-grinding involves crushing the clinker before it enters the mill, while inter-grinding additives are blended with the clinker during the grinding process to reduce particle agglomeration …
اقرأ أكثر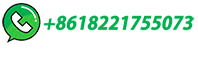
EVERYTHING YOU NEED TO KNOW ABOUT …
Clinker Grinding Mill. The clinker, gypsum, and additive will next be fed into the grinding mill, to produce the desired type of cement. Essentially this is a rotating horizontal cylinder containing steel balls. The materials …
اقرأ أكثر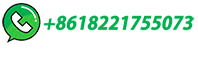
Quality & Composition of cement clinker
Cement clinker is produced by sintering the kiln feed at a temperature where 20~30% of the material melts to form a liquid flux. ... The higher strength performance of mineralised cements provides the opportunity to reduce the fineness of grinding of cement at the finish milling stage and thereby save electrical energy consumption, and also ...
اقرأ أكثر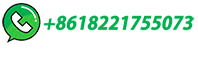
The Cement Manufacturing Process
Cement manufacturing is a complex process that begins with mining and then grinding raw materials that include limestone and clay, to a fine powder, called raw meal, which is then heated to a sintering temperature as high as 1450 °C in a cement kiln. ... systems are used by cement QC laboratories to determine major and minor oxides in …
اقرأ أكثر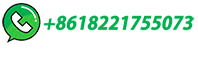
Diving into the Depths of Clinker Grinder: Unveiling its …
The clinker grinder, a crucial component in industrial settings, plays a fundamental role in the efficient operation of power plants and cement manufacturing …
اقرأ أكثر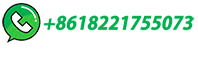
The clinker manufacturing process
The clinker manufacturing process. The clinker manufacturing process starts with the extraction of the raw meal from the homogenization silo to insure that the raw meal is stable and homogenized in order to produce consistent clinker quality.
اقرأ أكثر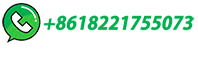
CLINKER GRINDING IN CEMENT PRODUCTION
Earlier we considered a mixture of which materials is used in cement production. The base of this mixture is a clinker. In this article, we will consider the composition of clinker and its impact on grinding balls deterioration in milling process. Clinker (in cement industry) is transitional product in cement production. Upon heating …
اقرأ أكثر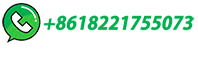
The Environmental Profile of Clinker, Cement, and Concrete: …
Concrete is the most-used material in the construction industry, and the second most-used after water. Cement is the main component of concrete. A total of 8% of global CO2 emissions correspond to the cement industry; CO2 is the main greenhouse gas contributing to global warming. To mitigate climate change, it is necessary to design …
اقرأ أكثر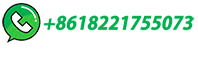
An Introduction to Clinker Grinding and Cement Storage
The cement clinker is ground as finished cement, in a vertical roller mill for cement or in ball mills similar to those normally used for grinding hard raw materials in dry and semi-dry …
اقرأ أكثر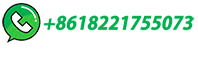