Rubber Tire Driven Ball Mill -Grinding Mill on Rollers
These very nice rubber tire driven grinding mills do not come cheaply priced. A small, 1 meter X 1.5 meter Rod mill OR Ball Mill cost approximately $160,000 US (in 2014) The small(est) mill starts at 600mm x 900mm and goes up to the large(est) 2100mm x 4200mm Options in the small "tyre" or Rubber roller grinding mills ...
ball mill méxico | Mining & Quarry Plant
Mineral Grinding Machines price & Sale Intermittence Ball Mill for sale Ball mill products & equipment,Energy-Saving Ball … coke grinder ball mills in mexico Coke grinder is a famous coke grinder machine in coal grinding industry including coke vertical mill, coke ball mill, coke Raymond mill etc.
اقرأ أكثر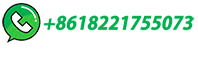
Ball mill introduction
Ball mill is a type of grinder used to grind materials into extremely fine powder mainly for use in mineral processing industry.The ball mill can grind various ores and other materials either wet or dry. ... Ball mill is a key piece of equipment for grinding crushed materials, and it is widely used in production lines for powders such as cement ...
اقرأ أكثر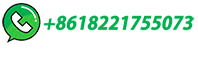
Vertimill VS Ball Mill
To participate in the 911Metallurgist Forums, be sure to JOIN & LOGIN; Use Add New Topic to ask a New Question/Discussion about Grinding.; OR Select a Topic that Interests you.; Use Add Reply = to Reply/Participate in a Topic/Discussion (most frequent). Using Add Reply allows you to Attach Images or PDF files and provide a more complete input.; …
اقرأ أكثر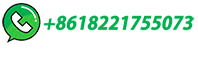
_Taurus
A rotating robust steel drum with liners is supplying kinetic energy to grinding media inside the mill. These grinding media are crushing and grinding fresh product due to impact and friction. The lining as well as the grinding media can be made out of hard wear resistant high manganese/chromium steel, ceramic or silex.
اقرأ أكثر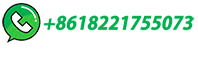
Grinding Media in Ball Mills for Mineral Processing
The performance of grinding media in a ball mill is measured in terms of wear rate, which is a function of the media composition, hardness, phase structure, and corrosive–abrasive characteristics of the slurry. The wear mechanisms involved in a ball mill are impact, abrasion, corrosion, and erosion.
اقرأ أكثر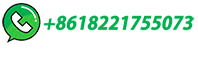
OPTIMIZATION OF CEMENT GRINDING OPERATION IN …
handled by the plant's maintenance crew. Upgrading the classifier and baghouse involves capital expenditure with a high benefit to cost ratio. Optimization is especially important when multiple products are being produced. Operation and Elements of a Closed-Circuit Ball Mill System . Cement ball mills typically have two grinding chambers.
اقرأ أكثر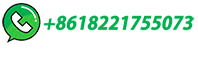
Ball Mill vs SAG Mill: What's the Difference?
As a general rule, SAG mills tend to be more expensive to acquire and maintain than ball mills, however, the cost-benefit analysis must consider the total cost of operation over the life of the mill. To get a closer look into quotes and details, you may find grinding mills here. Understand the Difference Between Ball Mill vs SAG Mill. In ...
اقرأ أكثر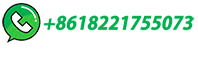
Ball Mills in the Mineral Processing Industry
In mineral processing plants, ball mills are employed in grinding circuits to reduce the particle size of the ore further, enabling the liberation of the desired …
اقرأ أكثر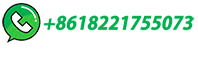
Exploring Ball Mill Diagram: A Comprehensive Guide
Balls mills are an important part of the gear in the mining and mineral processing industry, where they are utilized in the grinding stage of the crushing …
اقرأ أكثر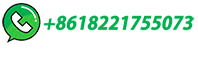
Replacement of Wet Ball Milling with High-Pressure Grinding …
In response to the Natural Resources Canada "Crush It Challenge," Corem partnered with the University of British Columbia and led a project to develop and demonstrate the use of high-pressure grinding to replace the workhorse of the industry, wet ball milling. Two plant case studies, a small tonnage gold recovery operation and a …
اقرأ أكثر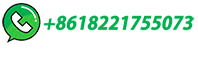
New and Used Ball Mills for Sale | Ball Mill Supplier …
Savona Equipment offers new and used Ball mills for sale in the USA, Canada, Mexico and South America. ... paints, pyrotechnics, ceramics and selective laser sintering. The ball mill is a key piece of equipment for grinding crushed materials, and it is widely used in production lines for powders such as cement, silicates, refractory material ...
اقرأ أكثر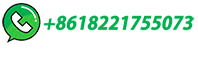
Planetary Ball Mills 101
Planetary ball mills share the same design as other basic ball mills – a grinding jar filled with media and rotated on its own axis. But their unique design takes advantage of centrifugal force and the Coriolis effect to grind materials to a very fine or even micron size. These forces come into play as
اقرأ أكثر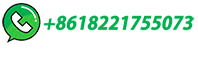
Grinding Mill Design & Ball Mill Manufacturer
Grinding Mill Specifications Data. According to formula 42.3/√d, where d is equal to internal shell diameter within new liners. In this case the thickness used was 60 mm for small mill sizes up to and including 2940 and 80 mm for larger mills.
اقرأ أكثر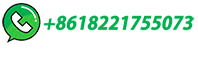
Batch Mill Grinding VS Continuous Grinding Compared
When the amount of ore in the mills was the same, no appreciable difference between batch and continuous open-circuit ball-mill grinding was found. This should be so, because the progression in particle size for the duration of a batch run would be expected to be the same as the progression from the feed to the discharge ends in a …
اقرأ أكثر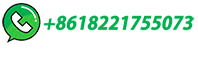
Tyre Drive Ball Mills
Tyre drive ball mills mainly for dry and wet grinding for the mining industry. It is a new kind of ball mills for ore grinding. Because of adopting the tyre drive manner, making the …
اقرأ أكثر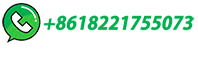
trailer mounted ball mill | Mining & Quarry Plant
Ball Mounts at discount prices from Mill Supply … Ball Mounts Parts on this page replace manufacturer part numbers:724920065405, 1803007, 1803015 and 724920065405 …
اقرأ أكثر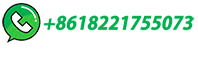
Ball Mill | Mining Grinding Mill
The ball mill can efficiently and finely grind various materials with different hardness and abrasion properties, including metallic ores, non-metallic ores, cement clinker, etc.; It has a highly automated control system, …
اقرأ أكثر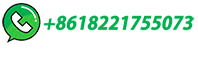
Ball Mill VS Rod Mill: Difference & Selection
Ball and rod mills are widely used grinding equipment in mineral processing plants. The two are similar in appearance and grinding principle, but there are differences in structure, performance, use, etc. This article will introduce their similarities and differences and tell you how to choose a ball mill and a rod mill.
اقرأ أكثر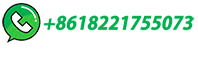
Factors Affecting Ball Mill Grinding Efficiency
The following are factors that have been investigated and applied in conventional ball milling in order to maximize grinding efficiency: a) Mill Geometry and …
اقرأ أكثر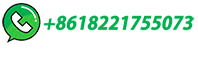
Fine Grinding as Enabling Technology – The IsaMill
Figure 1 : Grinding Power to produce various product sizes in a Ball Mill (9mm balls) and an Isa Mill (2 mm sand) (for KCGM pyrite concentrate) Chemistry Impacts The use of inert grinding media gives a crucial advantage to stirred milling in fine flotation and leaching applications. Even if it were economic to grind to 10 microns in a steel ...
اقرأ أكثر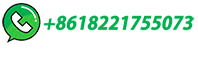
A Review of the Grinding Media in Ball Mills for Mineral …
The ball mill is a rotating cylindrical vessel with grinding media inside, which is responsible for breaking the ore particles. Grinding media play an important role in the comminution of mineral ores in these mills. This work reviews the application of balls in mineral processing as a function of the materials used to manufacture them and the …
اقرأ أكثر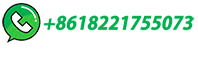
AMIT 135: Lesson 6 Grinding Circuit – Mining Mill …
Basic Mill Linings. Use rubber linings wherever possible due to lifetime, low weight, easy to install and noise dampening.; When application is getting tougher use steel-capped rubber, still easier to handle than steel.; When these both options are overruled (by temperature, feed size or chemicals) use steel.; Ore-bed is a lining with rubber covered permanent …
اقرأ أكثر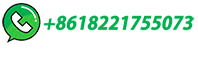
Mini Ball Mill
Our mini ball mills are perfect for piloting regrind applications or ultra low capacity mineral processing test plants. Sizes 8″ x 8″ to 12″ x 24″ (ball and rod mill) Mild steel construction Flanged heads Bronze trunnion bearings (oil-lubricated) Replaceable trunnion liners Replaceable one-piece steel liner with integral lifters V-belt drive OSHA-type drive guard …
اقرأ أكثر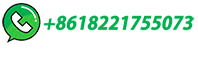
How To Choose Ball mill Or Wet Pan Mill In Grinding Gold
Wet disc mills generally have simpler mechanical structures and fewer moving parts than traditional ball mills, which can mean lower downtime and operating costs. 3. Abrasiveness. Harder materials may wear out the ball mill more quickly than a sturdier designed wet disc mill, requiring more frequent grinding media changes.
اقرأ أكثر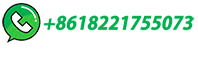
A Review of the Grinding Media in Ball Mills for Mineral …
The ball mill is a rotating cylindrical vessel with grinding media inside, which is responsible for breaking the ore particles. Grinding media play an important …
اقرأ أكثر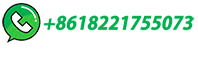
Kinetics of Dry-Batch Grinding in a Laboratory-Scale Ball …
in a mineral processing plant [1–5]. With ball-mill grinding being one of the most energy-consuming techniques, setting the optimal values of the operational and mineralogical parameters for e cient grinding is a key target in mineral processing plants [6–10]. Ball size is one of the key factors of ball-mill
اقرأ أكثر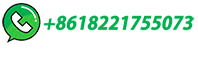
Grinding Media Balls
The use of ball mills in mineral comminution is a critical step in many extraction and production processes where size reduction to a fine powder is required. While pan milling and grinding plates is used in …
اقرأ أكثر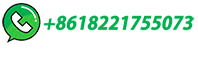
Ball Mills
Ball mills have been the primary piece of machinery in traditional hard rock grinding circuits for 100+ years. They are proven workhorses, with discharge mesh sizes from ~40M to <200M. Use of a ball mill is the best choice when long term, stationary milling is justified by an operation.
اقرأ أكثر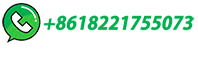
Grinding & Classification Equipment
The ball mill can process various grinding minerals, non-ferrous metal beneficiation, and new building materials. It is often combined with a spiral classifier to form a closed-circuit …
اقرأ أكثر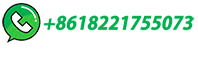
Rubber Tire Driven Ball Mill -Grinding Mill on Rollers
These very nice rubber tire driven grinding mills do not come cheaply priced. A small, 1 meter X 1.5 meter Rod mill OR Ball Mill cost approximately $160,000 US (in 2014) The small(est) mill starts at 600mm x 900mm and goes up to the large(est) 2100mm x 4200mm. Westpromachinery Sepro System
اقرأ أكثر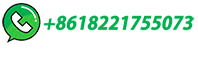