A comparison of SAG mill power models
There are several mill power draw models available to perform the ... • εB is the porosity of the rock and ball bed, as a fraction of total bed volume (e.g. 0.3 for 30%) ... published method works out to 0.17, an additional 507 kW, for a total of 3,472 kW power draw at
اقرأ أكثر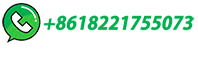
MODULE #5: FUNCTIONAL PERFOMANCE OF BALL MILLING
Size rated as diameter x length. Feed System 1. One hopper feed 2. Diameter 40 – 100 cm at 30 ° to 60 ° 3. Top of feed hopper at least 1.5 meter above the center line of the mill. Feeder 1. Single or double helical scoop feeder or a spout feeder 2. Double helical feeders used in closed-circuit with classifiers 3. Spout feeders p…
اقرأ أكثر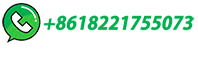
AMIT 135: Lesson 6 Grinding Circuit – Mining …
Grinding is a powdering or pulverizing process using the rock mechanical forces of impaction and attrition. ... Larger than Ball mills at same power draw . Special Tumbling Mill ... (135-6-14)] Conical Ball Mill. Wet or dry …
اقرأ أكثر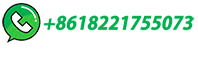
The effect of ball size distribution on power draw, charge …
The results showed that at a constant mill filling, the power draw was changed with changing the ball size distribution and for all mill fillings the maximum power draw occurred when the fraction ...
اقرأ أكثر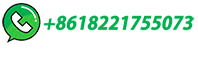
Ball Milling
Ball milling technique, using mechanical alloying and mechanical milling approaches were proposed to the word wide in the 8th decade of the last century for preparing a wide spectrum of powder materials and their alloys. In fact, ball milling process is not new and dates back to more than 150 years. It has been used in size comminutions of ore, …
اقرأ أكثر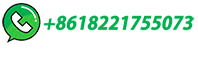
Charge behaviour and power consumption in ball mills: …
In this paper, we analyse the effect of changes in particle size and shape distribution (for both balls and rocks), lifter pattern and profile, and fill level on power …
اقرأ أكثر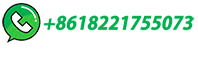
Ball mill- Principle, Construction, Working
3. Granulation: Ball mills can be employed for wet or dry granulation processes, where pharmaceutical powders are agglomerated into granules of controlled size. Granulation is a common step in tablet and capsule manufacturing. 4. Solubility Enhancement: In the pharmaceutical industry, ball mills enhance the solubility of poorly …
اقرأ أكثر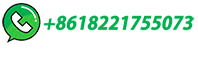
Ball Mill Design/Power Calculation
The power consumption per short ton will only be correct for the specified size reduction when grinding wet in closed circuit. If the method of grinding is changed, power consumption also changes as follows: ... Ball Mill Power Calculation Example #1. A wet grinding ball mill in closed circuit is to be fed 100 TPH of a material with a work ...
اقرأ أكثر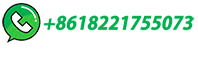
Experimental investigation of the power draw of tumbling mills in wet …
Charge behaviour and power consumption in ball mills: sensitivity to mill operating conditions, liner geometry and charge composition. ... Rezaeizadeh M. Investigating the kinematic and dynamics of mill contents with DEM and experimental methods PhD Thesis, Mechanical Engineering Department, Bahonar University, …
اقرأ أكثر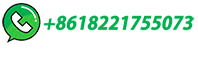
Experimental analysis of wet mill load parameter based on …
The feed rate, power draw, pulp temperature were collected automatically by the control system while samples of the feed material and ground product of the ball mill were manually taken to ...
اقرأ أكثر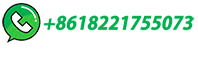
The Ultimate Guide to Ball Mills
6. According to the operation characteristics of ball mill: • Wet ball mill: Adding water when feeding, the discharging material is discharged when it is in a certain concentration of slurry. The wet ball mill forms the closed circuit operation with the hydraulic classification equipment in the closed circuit system.
اقرأ أكثر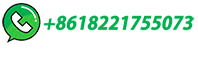
mill power draw mechanical methods wet ball mill
Mill Power Draw Mechanical Methodswet Ball Mill Ill Power Draw Mechanical Methods Wet Ball Mill. mill power draw mechanical methods wet ball mill. Ball-Rod Mills, based on 4 liners and capacity varying as 2.6 power of mill diameter, on the 5 size give 20 per cent increased capacity on the 4 size, 25 per cent and on the 3 size, 28 per cent.
اقرأ أكثر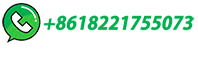
Ball Mill (Ball Mills Explained)
Crushed ore is fed to the ball mill through the inlet; a scoop (small screw conveyor) ensures the feed is constant. For both wet and dry ball mills, the ball mill is charged to approximately 33% with balls (range 30-45%). Pulp (crushed ore and water) fills another 15% of the drum's volume so that the total volume of the drum is 50% charged.
اقرأ أكثر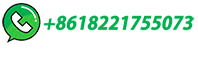
Functional Performance of Ball Milling Circuits – A Plant …
Mill power draw (MP) Ball mill power draw is measured during a circuit survey by means of calibrated power draw instrumentation. The reference point for power draw is the mill …
اقرأ أكثر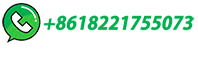
A Review of the Grinding Media in Ball Mills for Mineral …
The ball mill is a rotating cylindrical vessel with grinding media inside, which is responsible for breaking the ore particles. Grinding media play an important role in the comminution of mineral ores in these mills. This work reviews the application of balls in mineral processing as a function of the materials used to manufacture them and the …
اقرأ أكثر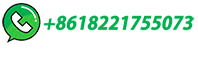
A method to identify wet ball mill's load based on …
A ball mill is a type of heavy mechanical equipment that relies on its own rotation to drive the steel balls inside to impact and grind materials with high reliability. However, the ball mill has the disadvantages of low working efficiency and high energy-consumption. ... a novel method of wet ball mill load identification based on CEEMDAN ...
اقرأ أكثر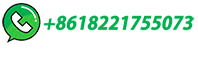
What is a Ball Mill Explained: In-Depth Guide
Critical Speed: Critical speed is the hypothetical speed at which the centrifugal force is equal to the gravitational force, and the grinding media starts sticking to the inner shell of the equipment instead of falling freely.Grinding at or close to critical speed of the mill yields a poorer grinding efficiency. The ball mills are mostly operated at 65 …
اقرأ أكثر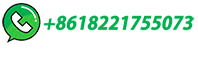
Mill power draw models
Mill Power Draw Models. The mill power draw models are used to predict how much power will be consumed by a particular type of mill, mill geometry and set of mill operating conditions. This power is transferred to the ore and used to predict the throughput when combined with the specific energy consumption models.
اقرأ أكثر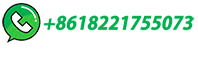
Grinding in Ball Mills: Modeling and Process Control
The paper presents an overview of the current methodology and practice in modeling and control of the grinding process in industrial ball mills.
اقرأ أكثر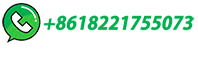
Dry ball milling and wet ball milling for fabricating copper–yttria
Yttria-reinforced copper matrix composites were prepared by dry ball milling (DBM) and wet ball milling (WBM), respectively, followed by spark plasma sintering (SPS). It is to determine which milling process is better for fabricating Cu–Y2O3 composites. It is found that Cu–Y2O3 composites synthesized by DBM exhibit better densification, …
اقرأ أكثر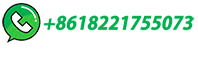
Ball Mill Motor Power Draw Sizing and Design Formula
The following equation is used to determine the power that wet grinding overflow ball mills should draw. For mills larger than 3.3 meters (10 feet) diameter …
اقرأ أكثر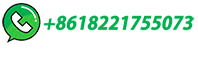
Modern Wet Milling and Material Processing | …
Traditional Wet Milling. The coatings industry is no different from others in its search for modern manufacturing techniques. The traditional high-speed dissolver, ball mill, vertical mill and standard horizontal mill have been the primary methods used to mill pigmented materials for more than 50 years, and are still considered to be the industry …
اقرأ أكثر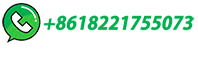
Ball Mill Motor Power Draw Sizing and Design Formula
The following equation is used to determine the power that wet grinding overflow ball mills should draw. For mills larger than 3.3 meters (10 feet) diameter inside liners, the top size of the balls used affects the power drawn by the mill. This is called the ball size factor S.
اقرأ أكثر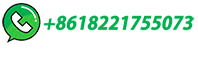
Mechanism characteristic analysis and soft measuring method …
1. Introduction. Operational optimization control and reduction on energy consumption for the entire production process of mineral processing enterprises are urgent problems that should be solved (Chai, 2013, Chai et al., 2014a, Chai et al., 2014b).Grinding process is a "bottleneck" operation in mineral processing, where broken raw ores are …
اقرأ أكثر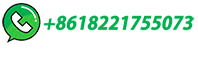
The prediction of power draw in wet tumbling mills
Semantic Scholar extracted view of "The prediction of power draw in wet tumbling mills" by S. Morrell. Skip to search form ... Methods Citations. 9. Results Citations. 1. View All ... This paper investigates grinding media's dynamic voidage to improve the Morrell-C model's accuracy in predicting the ball mills' power draw. Using a three-level ...
اقرأ أكثر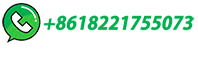
Exploring Ball Mill Diagram: A Comprehensive Guide
The speed of ball mill rotation is a critical parameter which determines the grinding efficiency and the end product quality. The optimum speed will differ depending on the mill's diameter, the size and density of the grinding media, and …
اقرأ أكثر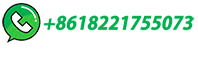
Analysis of ball movement for research of grinding …
A simulation of the three-dimensional motion of grinding media in the stirred media mill for the research of grinding mechanism has been carried out by 3-dimensional discrete element method (DEM). The movement of ball assemblies was graphically displayed with some snapshots from start of the milling to 0.20 s. From these simulation …
اقرأ أكثر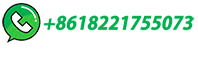
Ball Mill Motor Power Draw Sizing and Design …
Ball Mill Motor Power Draw Sizing and Design Formula. The following equation is used to determine the power that wet grinding …
اقرأ أكثر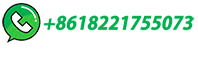
Ball milling as a mechanochemical technology for …
Wet ball milling is a green and labor-saving technology at room temperature. Wet ball milling of biochar with organic solvents (such as ethanol, hexane, and heptane) was proved to effectively enlarge the Brunauer-Emmett-Teller (BET) surface area of derived biochar up to 194 m 2 g −1, compared with 3 m 2 g −1 of the unmilled
اقرأ أكثر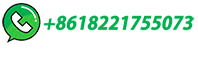
A comparison of the Bond method for sizing wet tumbling ball mills …
Excessive mill speeds caused more power consumption but resulted in reduced grinding rate. Based on the simulation data, two scale-up models were proposed to predict power draw and grinding rate. The models were tested with larger mills and show excellent prediction on power draw and reasonable accuracy on grinding rate.
اقرأ أكثر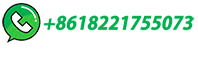