Ball Mill VS Rod Mill: Difference & Selection
Ball and rod mills are widely used grinding equipment in mineral processing plants. The two are similar in appearance and grinding principle, but there are differences in structure, performance, use, etc. This article will introduce their similarities and differences and tell you how to choose a ball mill and a rod mill.
اقرأ أكثر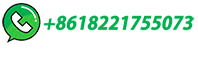
The Selection and Design of Mill Liners
Figure 5. High–low wave ball mill liner Materials The selection of the material of construction is a function of the application, abrasivity of ore, size of mill, corrosion environment, size of balls, mill speed, etc. liner design and material of construction are integral and cannot be chosen in isolation.
اقرأ أكثر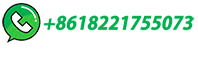
Grinding Media in Ball Mills-A Review
Table 1. Chemical composition of typical grinding media (% wt.). Adapted from [24]. 2.1.1. Cast Iron Cast iron can be grey cast iron or white cast iron, but white cast irons are commonly used in ...
اقرأ أكثر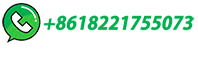
Ball mill principle: An explanation of operation and …
Applications of Ball Mills. Ball mills find extensive application in industries such as: 1. Mining and Mineral Processing: Ball mills are commonly used in the preparation of ores for mineral beneficiation, as well as in the production of metals and minerals. 2. Ceramics: Ball mills are essential in the production of ceramics, where fine ...
اقرأ أكثر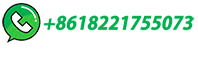
BALL MILLS Ball mill optimisation
production costs as well as maintenance costs. Ball mills and grinding tools Cement ball mills are typically two-chamber mills (Figure 2), where the first chamber has larger media with lifting liners installed, providing the coarse grinding stage, whereas, in the second …
اقرأ أكثر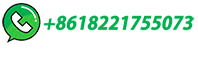
Difference and Choice of 2 Common Mills, Ball …
Ball mill production capacity can be adjusted between 0.65-615 tons. In general, according to the grinding process and investors demand, manufacturers can provide customized grinding machine and …
اقرأ أكثر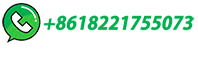
Improvement of Ball Mill Performance in Recycled …
structure of graphite consists of the multilayer stacking of ... required for sustainable manufacturing and production cost-saving for material and waste disposal costs. For example, ... Ball Milling Process. A pilot-scale ball mill with a 25 L ceramic chamber, containing 50 kg of four mixed-size ZrO 2 balls (10, 15, 20, and 25 mm with a ratio ...
اقرأ أكثر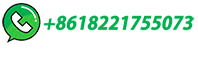
Parametric study on four station ball mill for synthesis of …
Comparison of different milling methods: The study may have compared the four-station ball mill with other milling methods, such as the planetary ball mill, vibratory ball mill, and attritor mill. The comparison results may indicate that the four-station ball mill is more efficient and cost-effective for the synthesis of ultrafine powders at a ...
اقرأ أكثر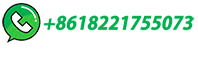
SAG Mill Grinding Circuit Design
These mills typically grind ROM ore in a single stage. A large example of such a mill was converted from a single-stage milling application to a semi autogenous ball-mill-crushing circuit, and the application is well described. This refers to high-aspect AG/SAG mills. Ball Charge Motion inside a SAG Mill. With a higher density mill charge.
اقرأ أكثر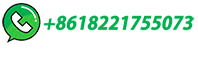
Trunnion Bearing Ball Mill vs. Slide Shoe Bearing Ball Mill
The design and structure of trunnion bearing ball mills are carefully engineered to ensure optimal performance. The mill consists of a hollow cylindrical shell, typically made of steel, with the ends fitted with trunnion bearings. ... Additionally, slide shoe bearing ball mills are cost-effective, with lower initial costs compared to trunnion ...
اقرأ أكثر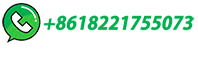
How to Choose Ball Mill Trunnion for Cement Mill, Autogenous Mill…
When selecting a ball mill trunnion for your mill, several crucial factors should be considered to ensure optimal performance and longevity. 1. The operating conditions and environment of the ball mill play a significant role in mill trunnion selection. Factors such as temperature, humidity, and the presence of corrosive substances must …
اقرأ أكثر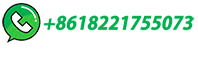
Optimization of ball mill cylinder structure based on …
The optimization design can save materials and costs, and provide a theoretical reference for the lightweight research of the ball mill's cylinder. The cylinder …
اقرأ أكثر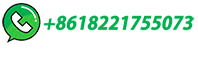
Cement Ball Mill | Cost Effective Cement Grinding Mill from …
The installation of liners. Length Diameter Ratio. The length-diameter ratio of the cement ball mill is relatively large. For mills of open-circuit grinding system, the length-diameter ratio is usually between 3.5 and 6 to ensure that the product fineness is qualified through single grinding; For ball mills in closed-circuit grind system, in order to increase the …
اقرأ أكثر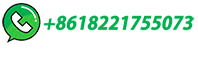
What's the Difference Between Ball Mill, Rod Mill and SAG Mill?
different grinding media of ball mills, rod mills and SAG mills. Crushing ratio Comparison. The biggest feature of SAG mills is the large crushing ratio, which can crush and grind the materials to 0.074mm at one time, accounting for more than 20% to 40% of the total product.
اقرأ أكثر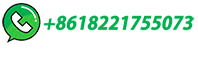
Mini Ball Mill – Mineral Grinding Small Ball Mill For Sale
The mini ball mill is a type of small-scale ball mill, suitable for trial production and small batch production. AGICO offers high-efficiency mini ball mills at a competitive price. ... Mini Ball Mill Structure. ... which have high wear resistance and low use-cost. The equipment motor complies with international standards.
اقرأ أكثر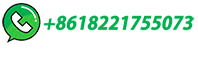
Grinding in Ball Mills: Modeling and Process Control
An important characteristic of an industrial ball mill is its production capacity which is measured in tons of production per hour. The production capacity depends
اقرأ أكثر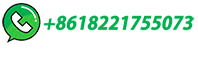
Vertical Stirred Ball Mills – ZJH minerals
1.4, Simple structure, easy operation and maintenance, small footprint, the foundation cost is less than 1% of the machine cost. Application scope of JM stirred ball mill. 2.1, Adopting The vertical spiral stirred mill to …
اقرأ أكثر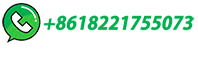
Grinding in Ball Mills: Modeling and Process Control
56 parameters of the process. In this case the kinetic and energy type of models are most frequently used. II.2. Kinetic and energy models Several basic assumptions are made in modeling of the ...
اقرأ أكثر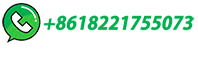
Structure Of A Ball Mill | Crusher Mills, Cone Crusher, Jaw …
Information about the Structure of Ball Mill – Mining – Zimbio. Information about the Structure of Ball Mill . By jocelyn0825 on 1. Cylinder: the ball …
اقرأ أكثر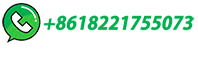
Grinding Ball Design
If structure and hardness vary, surface to center, the size distribution will be skewed. Typical 127 mm (5 in.) martensitic balls are hard on the exterior, softer in the center. ... a routine program of quality control is an investment that can pay good dividends in ball cost and mill production. Elements of an effective ball quality-control ...
اقرأ أكثر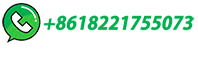
Cement Ball Mill
【Cement mill structure】 Ball mill is mainly composed of feeding part, supporting frame, rotary part, discharge, transmission, lubricant and cooling part. ... Cement has corrosion, which affects the service life of steel ball and increases the production cost. 2. Different wear-resistant microelements in different materials of wear-resistant ...
اقرأ أكثر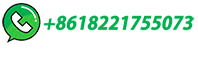
Exploring Ball Mill Diagram: A Comprehensive Guide
A ball mill consists of three main components: the shell, the grinding media (balls or pebbles), and the engine. The shell is constructed as a metal tube that is hollow …
اقرأ أكثر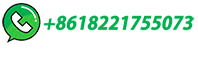
Grinding in Ball Mills: Modeling and Process Control
55 known as the distribution function [45, 46]) describes the distribution of fragment sizes obtained after a breakage of particles of size xj.Thus, b1j, b2j, …, bnj are the mass fractions of particles in size classes 1, 2, …, n after a breakage of particles in size class j. The mechanism of breakage is illustrated in [23] by a diagram shown in Fig. 3.
اقرأ أكثر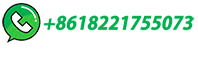
What is the difference between vertical mill and ball mill?
Ultrafine vertical mill VS ball mill. Product performance. Ball mill: Generally, produce 45um thick body; ultra-fine ball mill can produce 10um powder; ceramic ball mill has high whiteness and the lowest iron content. Good grain, spherical
اقرأ أكثر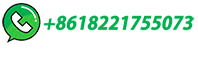
screens dramatically increase production, lower cost in …
the ball mill for re-grinding, along with the raw or new feed stream. In this process, a circulating load of 300 to 350 percent was the accepted norm. In other words, the amount of material circulating back to the ball mill was 3 to 3-1/2 times the amount of new feed added to the mill! Exploring the use of screens in 1996
اقرأ أكثر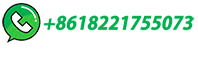
Technical specifications and selection guide for ball mills
Ball mills are widely used in the mining and mineral processing industries for fine grinding and mixing materials. The selection of the appropriate ball mill is critical to ensuring …
اقرأ أكثر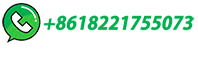
Ball, Pebble and SAG Mills: A Buyers Guide
The Ball Mill, the Pebble Mill and the SAG Mill are 3 of the most popular types of mills on the industrial market. They are primarily used for the Mining industry, but they can also be used in the Chemical & Processing industry which has it's own category page for those listings here: Ball, Pebble, SAG Mills for Chemical Use .
اقرأ أكثر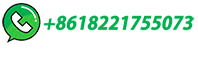
Cost-Effective Solution for Small Scale Ball Mill Material …
Ball mills are an essential tool for material processing, and their significance has only grown over the years. However, large scale ball mills can be costly and impractical for small businesses and start-ups. That's where small scale ball mills come in – they are a cost-effective solution that can handle a range of materials and applications.
اقرأ أكثر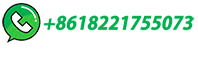