OK™ Raw and Cement Mill
In 2017 we released the OK™ vertical roller mill for raw materials grinding. The OK™ Mill's modular design comes with unique flexibility, showcasing parts commonality, where spare parts can be shared between vertical roller mills regardless of size and application. Equipment longevity is assured with durable wear protection on all ...
اقرأ أكثر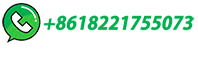
CLRM Enhanced Roller Mill
The CLRM Enhanced Roller Mill adjusts for powder from 80 to 500 mesh, ideal for materials under Mohs 6. ... capable of producing powder from 80 to 500 mesh, and is …
اقرأ أكثر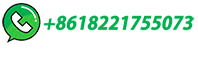
Polysius Roller Mills. For grinding
uses the test-roller mill Atrol (throughput approx. 240 kg/h) for grindability testing and quantitative prediction of wear in industrial mills. Roller mill for granulated blast furnace slag grinding in China. Roller mill for cement raw material grinding in China. Roller mill for cement clinker grinding in Mexico. Coal grinding plant in Poland.
اقرأ أكثر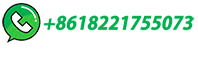
OK™ raw mill Reliable and efficient raw material grinding
A complete size range, including the largest VRM available for raw grinding, ensure the ability to meet all possible capacity require-ments in a single mill even for the hardest materials. The well-known reputation of the OK mill as a reliable machine that is easy to operate and maintain continues with the OK raw mill. In addition to the roller ...
اقرأ أكثر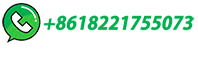
Research of iron ore grinding in a vertical-roller-mill
The application of vertical-roller-mills (VRM's) for ore grinding is part of the second strategy. The grinding parts of a Loesche mill (Fig. 1) are a rotating table (1) with a horizontal grinding track and rollers (2), which are pressed onto the table by lever arms and a hydro pneumatic spring system.
اقرأ أكثر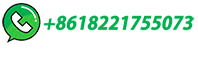
How it Works: Crushers, Grinding Mills and Pulverizers
Table Source: Wikipedia (Crushers) Cone crushers use a spinning cone that gyrates in the bowl in an eccentric motion to crush the rock between the cone surface, referred to as the mantle, and the crusher bowl liner.Gyratory crushers are very similar to cone crushers, but have a steeper cone slope and a concave bowl surface. As the gap …
اقرأ أكثر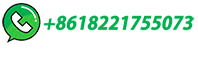
Energy-saving and Efficient Vertical Roller Mill
HLM series vertical mill is a large-scale, high-yield, and energy-saving grinding product developed by FTM Machinery using advanced grinding and external circulation technology, combined with years of milling …
اقرأ أكثر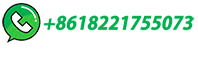
Vertical Roller Mills
Projects. More than 100 customer cases of vertical mill production lines. CHAENG vertical roller mill is applied in many large production lines, playing an important rolls in slag, cement and other material production lines, such as: Shanghai Baosteel 1,500,000 tons /year composite powder (slag, steel slag) production line, Henan Meng Electric Group …
اقرأ أكثر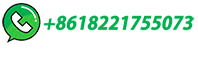
Limestone Powder Ultrafine Vertical Roller Mill
The limestone powder vertical grinding mill grinds materials by the principle of material layer grinding, with low energy consumption. The power consumption of the grinding system is 20% to 30% lower than that of the ball mill, and the energy saving effect is more obvious as the moisture of the raw material increases.
اقرأ أكثر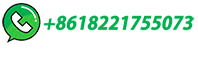
SikaGrind® for vertical roller mills
The production of Portland Cement (OPC, CEM I) with Vertical Roller Mills can demand the following benefits from a Grinding Aid: ́ Increased production rate, energy saving ́ Higher …
اقرأ أكثر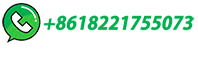
Roller Press
Simply put, the roller press is the most energy-efficient grinding machine on the market. Since its commercial introduction into the cement industry by KHD in the 1980s, hundreds of them have been installed in the cement …
اقرأ أكثر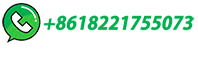
OK™ mill The most reliable and efficient mill for raw and …
The OK mill efficiently grinds even the hardest raw materials and blended cements with a wide range of additives such as slag, pozzolana, limestone and fly ash.
اقرأ أكثر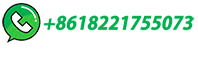
QUADROPOL roller mill
The two roller units remaining in the mill then continue the grinding process. This mill system from Polysius thus fulfils the prere-quisites for "online operation" in the cement factory with a practically uninterrupted flow of material from the mill to the kiln. High grinding plant availability has two beneficial results: it permits the ...
اقرأ أكثر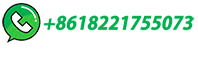
Vertical roller mills | FL Cement
The vertical roller mill is well known in the cement and power plant industries as the preferred mill for grinding of raw materials. It is increasingly used as a solution for efficient grinding. ... continuous advances in manufacturing processes and design principles have helped us to produce reliable vertical roller mills of ever-larger size ...
اقرأ أكثر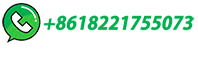
RAYMOND® ROLLER MILLS
Raymond roller mills are available with grinding ring diameters ranging from 30 inches to 120 inches (760 to 3050 mm). These sizes are capable of producing a wide range of …
اقرأ أكثر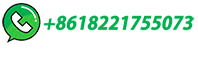
PROCESS CONTROL FOR CEMENT GRINDING IN VERTICAL ROLLER MILL …
The power ingesting of a grinding process is 50-60% in the cement production power consumption. The Vertical Roller Mill (VRM) reduces the power consumption for cement grinding approximately 30-40% associated with other grinding mills. The process variables in cement grinding process using VRM are strongly nonlinear and having …
اقرأ أكثر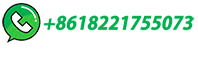
Numerical Investigation of Vertical Roller Mill Operation …
A vertical roller mill (VRM) is a grinding equipment used for the size reduction of minerals, cement, and ceramics. ... size reduction of raw materials is an energy-intensive operation. A vertical roller mill is a grinding equipment for many industries such as minerals, cement, and ceramics. ... Jensen LRD, Fundal E, Møller P, …
اقرأ أكثر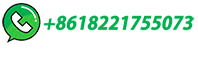
Wollastonite Industrial Grinding Mill Equipment
HGM ultrafine industrial grinding mill. The newly designed grinding roller grinding ring grinding curve improves the grinding efficiency. The production capacity is 40% higher than that of jet mills and stirring mills, and the energy consumption is only 30% of that of jet mills. Equipped with multi-head cage type powder concentrator.
اقرأ أكثر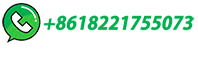
Grinding Mills and Pulverizers Selection Guide: Types, …
Video credit: shsbjq / CC BY-SA 4.0 Specifications. Important specifications when selecting grinding mills and pulverizers include, The size of the mill can range from pilot/lab to production, e.g., 3.5 to 1600 cu. ft.; Feed size, material, and hardness of feed must be considered.; Output size ranges.; Mills can handle dry or wet input, or both.; Mills …
اقرأ أكثر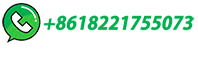
RAW MATERIAL GRINDING ITadipatri's big sixer
The first six-roller Loesche mill for grinding cement raw material was successfully put into operation in July 2008 (see Figure 1). The grinding plant is part of the new production line in the Tadipatri works of the second largest cement manufacturer in India, Grasim Industries Ltd, Mumbai and its subsidiary UltraTech Cement Ltd. Around 16,000t of
اقرأ أكثر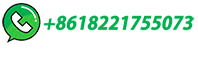
The Evolution of Clinker Vertical Roller Mills: From Inception …
The first significant use of the vertical roller mill for cement grinding can be traced back to the 1970s. ... these mills were used in raw material grinding, but their potential for clinker ...
اقرأ أكثر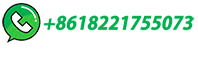
Everything you need to know about clinker/cement Grinding
cement mills with a drying chamber see raw mills. Mill working conditions: ventilation air speed through the mill. Bigger or smaller than 1.2 [m/s]. Material abrasivity. The [%] of slag or pouzzolana content on the fresh mill feed for cement grinding. The [%] of free silica at mill feed for raw material grinding. Moisture content of the mill ...
اقرأ أكثر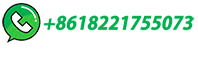
SvenMill
Our Main line of roller mills is the SvenMill™. It is used for a variety of functions including grain grinding (Corn, Wheat, Barley, Oats, Pulses, Oil seeds, etc.) as well as many other materials (Fertilizer, Coal, Nuts, Spices, etc.) The design of our roller mill allows for a gentle roll to preserve the quality of the grains being grinded. A ...
اقرأ أكثر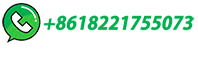
VERTICAL ROLLER MILLS
allow highly efficient grinding while maintaining vibration kept at minimum level. M/s. AMCL Machinery Ltd. (AMCL) has signed a Licensing Agreement in May 2019 with M/s. UBE Machinery Corporation Ltd., Japan to manufacture & supply state-of-the-art UBE Vertical Roller Mills for grinding applications related to Raw material, Coal, Clinker and Slag.
اقرأ أكثر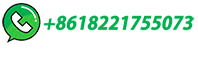
Grinding Of Abrasive Materials In The Mill | Crusher Mills, …
Cement raw materials grinding mill, raw mill, cement mill. Cement Raw Materials Grinding Mill. … Vertical mills can be used for moisture contents up to 16-18% as long as the raw materials are not very abrasive.
اقرأ أكثر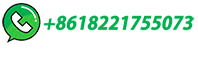
CLUM Ultrafine Vertical Grinding Mill
CLUM Ultrafine Vertical Grinding Mill. Discharge fineness: 150-3000 mesh Feed size.: 15 mm Output: 1-20 T/H
اقرأ أكثر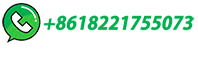
Modeling and simulation of vertical roller mill using …
The cement raw materials (lime, silica and iron ore) enter the circuit through two apron feeders. The raw materials are crushed in a hammer crusher to D 95 of 80mm. The raw materials are mixed in a certain proportion and fed into a vertical roller mill (LOESCHE mill). The vertical roller mill grinds the marital to D 85 of 90µm. The ground ...
اقرأ أكثر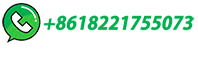
Clinker size and cement grinding | GCP Applied Technologies
Clinker size and cement grinding. ... For most mill systems, manufacturers recommend the following raw material size: Fine clinker is more of an issue in vertical roller mills, since it can quickly slip under the rollers, leading to vibration and instability. As a general rule, there should be less than 25% of clinker that is below 1mm in size.
اقرأ أكثر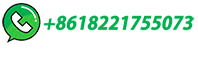
Coal mill, gypsum mill, clay mill, etc. | Pfeiffer …
Number of grinding rollers: 3: Feed size: up to 100 mm: Feed moisture: up to 10%: Target fineness degree of fine material: ... different wear materials are used on our vertical roller mills. The grinding elements are …
اقرأ أكثر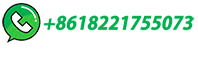