PROCESS OPTIMISATION FOR LOESCHE GRINDING …
• Cement raw material • Clinker / granulated slag • Industrial minerals, and • Ores The core elements of these plants are the Loesche vertical mills for dry-grinding the above-mentioned grinding stock. Loesche has developed and built the largest and most efficient grinding plants for its customers. Loesche plants
اقرأ أكثر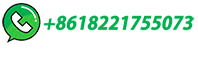
Modeling of energy consumption factors for an …
80 mm. e raw materials were mixed in a certain proportion and fed into a vertical roller mill (LOESCHE mill). e raw vertical roller mill has four rollers, 3000 KW main drive, 4.8 m table diameter ...
اقرأ أكثر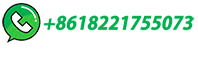
Cement mills and raw mills for small to medium throughput …
Gases (air or hot gas) flow through this nozzle ring, take up the ground and dried material and convey it to the classifier where it is separated by the rotating wheel (rotor) into grits and fines. The grits fall back into the grinding zone whereas the fines leave the classifier with the gas flow for being separated in cyclones or a filter.
اقرأ أكثر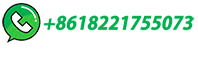
OK™ Raw and Cement Mill
Our best-in-class OK™ Mill is a globally successful vertical roller mill solution for grinding raw material, cement and slag. Its cutting-edge design features consistently deliver the highest quality products with the greatest efficiency. It is affordable to install and cost effective to operate over your cement plant's lifetime.
اقرأ أكثر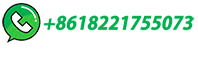
OCCUPATIONAL HEALTH AND SAFETY IN CEMENT INDUSTRY
These raw materials are crushed, finely ground, and blended to the correct chemical composition. The fine raw material is fed into a large rotary kiln (cylindrical 4 furnace) which rotates while the contents are heated to extremely high (EPA 2010). The most commonly used kiln fuels are coal, natural gas, and occasionally oil (EPA 1994).
اقرأ أكثر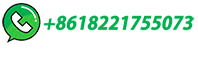
petcoke grinding vrm
Petcoke Grinding Vrm - art-de-pierre.eu. Petcoke Grinding Vrm . petcoke grinding vrm - Newest Crusher, Grinding Mill . Grinding elements take the wear and tear of coal pulverisation · PDF . coals (lignite) to anthracite and Petcoke.Xwin is a technology in which granularised ceramic, . to the grinding face.
اقرأ أكثر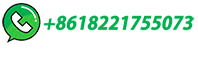
New raw mill increases productivity at Mojave | World Cement
At CalPortland's Mojave cement plant, kiln production and efficiency were adversely impacted by the reliability of the raw mill, which struggled with the increasing demands of a hot market. The decision was made to …
اقرأ أكثر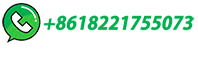
FCT-ICON SOLID FUEL HOT GAS GENERATOR
without contact with metal or moving parts, before combustion and the generation of hot gases that can be used in subsequent processes such as drying. The FCT-ICON Solid Fuel Hot Gas Generator replaces equipment that uses traditional fuels (such as natural gas, LPG or fuel oil) to instead make use of solid fuels that may be less expensive ...
اقرأ أكثر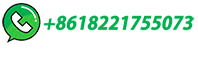
Cement Manufacturing—Technology, Practice, and …
The raw meal is prepared by drying and grinding in ball mills or vertical roller mills. Drying is achieved by using the hot gases or air from the kiln or the cooler. …
اقرأ أكثر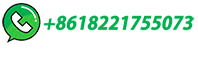
Sources of False Air
False air is mostly present in the following areas of a cement plant: * Raw mill grinding area * Kiln area * Cement mill grinding area ... In a typical dry process kiln systems, the feed materials are preheated by the hot gases …
اقرأ أكثر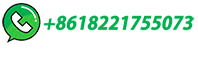
CEMENT PRODUCTION AND QUALITY CONTROL
In this unit, the proportioned raw materials are being ground to the size of (10% residual on 90 μm sieve) by closed circuit ball mill in line 1 and Vertical Roller Mill (VRM) in Line 2. While grinding; the raw materials are being dried from 4% moisture content to <1% using the excess hot gas emitted from pyrporocessing system.
اقرأ أكثر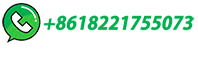
Modeling of energy consumption factors for an industrial …
By initiating a CL for an industrial cement vertical roller mill (VRM), this study conducted a novel strategy to explore relationships between VRM monitored operational …
اقرأ أكثر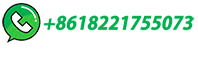
Thermal Applications
The mixing of these two gas flows results in the desired outlet temperature at the hot gas outlet (6). For burning lean gases The multiple-lance burner comprises a number of individual nozzles for lean gas and combustion …
اقرأ أكثر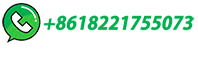
Advanced Air & Process Gas Flow Monitoring in Cement …
To optimize the flow of gases in cement plants, measuring the gas flow accurately is essential. ... Cyclone Preheaters are used before rotary kilns of cement production plants to heat the raw mix and drive off carbon dioxide and water before it is fed into the kiln. ... Now further development on material compatibility with hot gas having …
اقرأ أكثر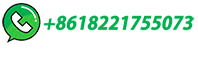
vertical cement raw mill hot gas requirement articles
Авах vertical cement raw mill hot gas requirement articles Үнэ(WhatsApp)Та мессежээ энд үлдээж болно, бид танд шууд имэйл илгээх болно.
اقرأ أكثر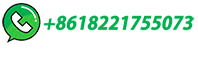
Assessment of the thermodynamics efficiency of a cement …
A process simulator was used to study an industrial-scale vertical raw mill (VRM) with 65.4% energy efficiency. The paper proposes further a new model based on …
اقرأ أكثر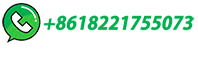
Narayana Jayaraman and Francisco Benavides, PEC …
variable speed drive to ensure constant gas flow at the mill outlet. The margin on raw mill fans is typically lower: 10% on volume and 20% on pressure. The raw mill fan is of large capacity and its specifications are determined by the mill characteristics. The cement mill and coal mill are similar to the raw mill requirements. Main filter fan
اقرأ أكثر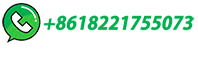
Measuring ball mill ventilation | GCP Applied Technologies
Mill ventilation is important for cooling the mill, removing moisture and improving mill efficiency. Typically, a velocity across the media of 1m/s is a good target. The challenge is to measure it. Cement producers are required to measure and report to government agencies about the air that flows up the cement mill stack.
اقرأ أكثر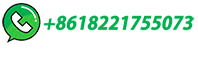
Everything you need to know about Kiln System Operations in Cement …
• Duct work to the hot air inlet of the mill. The hot air duct is provided with appropriate dampers and ambient air tempering to control temperatures at the mill inlet and outlet. • A raw fuel bunker or silo with a shutoff gate, and a raw fuel feeder, typically a belt scale. • A mill to simultaneously grind, classify, and dry the solid fuel.
اقرأ أكثر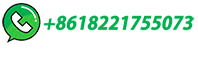
Vertical Raw Mill Heat Balance Excel Sheet
Vertical Raw Mill Heat Balance Excel Sheet . To Download the Below Excel sheet + most Important Cement Books and Guides from Famous companies click here now ... Hot gas condition before mill: Temperature: 200 °C: Pressure-95: mmH2O: Oxygen content: 9.6%: Volume at actual condition: 953,983:
اقرأ أكثر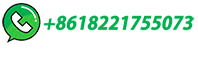
CEMENT INDUSTRY FANS
Cement industry uses large number of cooling fans usually between 5 to 15 in one clinker line based on the kiln capacity. Cooling fans are used to blow cold air to the cooler and to cool the ...
اقرأ أكثر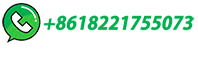
Raw milling and blending
The main difference to cement mill operation is the need to dry raw·feed and assure transport of stightly moist materialwithin a mill. ... Ball mills equipped with a .drying compartment and adequately swept with hot gas (1.5-3m/s above the ball charge),can handle feed with above 10 per cent moisture and a maximum size of around …
اقرأ أكثر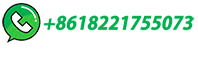
Thermodynamic Analysis of Raw Mill in Cement Industry Using Aspen Plus
Table 6: Simulation result for the exergy balance of the raw mill Exergy balance of raw mill Material Raw feed Moisture in raw feed Hot gas from kiln Unit kJ/h kJ/h kJ/h Input Simulation 3194 -9053 47474430 8 Material Raw meal Gas moisture Unit kJ/h kJ/h kJ/h Output Simulation 2024720 7545475 48152 ICESW IOP Publishing IOP Conf. Series ...
اقرأ أكثر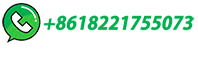
An overview of alternative raw materials used in cement …
Raw materials chemistry. Cement manufacture requires a source of calcium, such as CaCO 3 or CaMg (CO 3) 2, which comprises almost 80–90% of the total and the rest is iron oxide (Fe 2 O 3, Fe 3 O 4), quartz (SiO 2), and clay/bauxite (Al-silicates) (Aïtcin and Flatt Citation 2015; Hewlett Citation 2003; Peray and Waddell Citation 1986).Traces …
اقرأ أكثر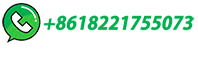
Raw Mill Moisture Content Management: A Comprehensive …
Hot gas generators: These systems introduce hot air or gas into the raw mill to dry materials during the grinding process, improving overall efficiency. 3.2. Optimizing Raw Mill Operations. Adjusting operational parameters in the raw mill can help control moisture levels and enhance grinding efficiency. Key adjustments include:
اقرأ أكثر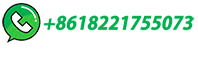
Safety in Cement Plant
Incidents and injuries resulting in burns arise from contact with hot clinker or cement powder. Hazards are particularly associated with hot cement kiln dust (CKD), and dust on preheater systems. Chemical (alkali) burns may also result from contact with CKD. Raw Mill and Preheater Tower: Material in the mill is at temperatures up to 120ºC, in the
اقرأ أكثر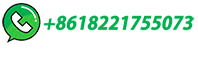
Thermodynamic Analysis of Raw Mill in Cement Industry …
The raw mill has a capacity of 240,000 kilogram-material per hour. Also, both exergy and exergetic efficiency of raw mills from three literature sources were investigated and …
اقرأ أكثر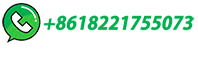
(PDF) Thermodynamic Analysis of Raw Mill in Cement
Furthermore, the power consumption of the raw mill grinding process was reduced by 6.7 percent by using exterior hot gas, as suggested in an energy and exergy …
اقرأ أكثر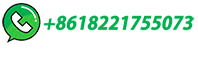
Reactions in the cement kiln
Raw meal is dispersed in the hot gas and calcination takes place in seconds, rather than the half an hour or so inside a kiln at the same temperature. Formation of early and intermediate compounds During calcination, the lime produced starts to react with other components of the raw feed. The initial silicate product is belite.
اقرأ أكثر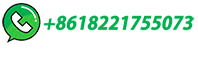
Reducing energy consumption of a raw mill in cement industry
The use of an external hot gas supply provides 6.7% reduction in energy consumption corresponding to a saving of 1.66 kWh per ton of farine production. ... In this study, the raw mill of a cement plant is considered and its performance based on the first and second laws of thermodynamics is investigated. Effects of weather conditions, …
اقرأ أكثر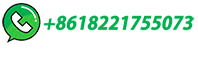