Processing the ores of rare-earth elements | MRS Bulletin
Rare-earth elements (REEs) are required for use in modern high-tech applications and demand has increased significantly over the last decade. 1 However, processing of REE ores poses potential hazards to human health and the environment due to challenges in the management of thorium (Th) and uranium (U) in waste products. 2 If …
اقرأ أكثر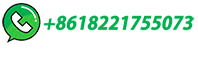
Application of deep learning in iron ore sintering process: a …
The sintering process is an intricate system with a protracted process flow. The steps in the manufacturing line are primarily composed of the ingredients and mixing process, the sintering operation process, and the treatment of the sintered ore [39, 40].2.2 Important parameters and characteristics of sintering process. As shown in Fig. 2, all …
اقرأ أكثر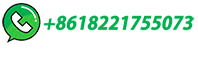
Iron Ore Characterization Techniques in Mineral …
well as ore processing. Keywords Iron ore · Characterization · SEM–EDS · XRD · XRF · FTIR Introduction The most common element that makes up rock formations is iron, which accounts for about 5 percent of the earth's crust. India alone has a signicant reserve of iron ore in the world [1]. The two most common iron minerals, hema-
اقرأ أكثر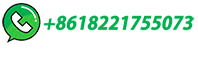
Iron ore beneficiation | Commodities | Mineral …
Our innovative surge bin technology, Lyons Feed Control Unit (LCFU), is currently being deployed into iron ore with the first installation in Western Australia. At 24 & 16 metres in diameter, these LFCUs are the largest …
اقرأ أكثر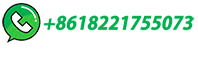
Steel Production
Steel is primarily produced using one of two methods: Blast Furnace or Electric Arc Furnace. The blast furnace is the first step in producing steel from iron oxides. The first blast furnaces appeared in the 14th century …
اقرأ أكثر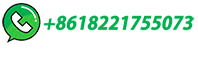
Iron processing
Iron processing - Smelting, Refining, Alloying: The primary objective of iron making is to release iron from chemical combination with oxygen, and, since the blast furnace is …
اقرأ أكثر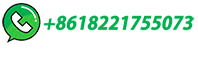
Iron Ore Processing
Iron ore processing refers to the techniques used to extract iron from oolitic iron ores, involving processes such as beneficiation, roasting, and magnetic separation to remove impurities like phosphorus and transform minerals for iron and steel production. ... asking for a less complicated process. By referring to the production technology of ...
اقرأ أكثر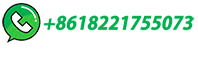
National Emission Standards for Hazardous Air Pollutants: Taconite Iron
The methodology and the results of the demographic analysis are presented in a technical report titled Risk and Technology Review—Analysis of Demographic Factors for Populations Living Near Taconite Iron Ore Processing Source Category Operations, June 2019 (hereafter referred to as the Taconite Iron Ore Processing Demographic …
اقرأ أكثر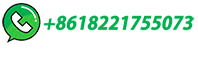
Iron Ore Agglomeration Technologies
Until the 1950s of the last century, the oxidized iron ores that were loaded into the blast furnace had granulometries within 10 and 120 mm. However, the depletion of high-grade iron ore sources has made necessary the utilization of concentration processes with the purpose of enriching the iron ore. Because of these processes, a fine …
اقرأ أكثر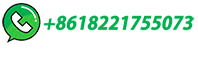
Kiruna Iron Ore Mine, Sweden
The current main haulage level at the mine is 1,365m underground. Ore processing takes place in three concentrating plants and three pelletising plants. The mine produces more than 75,000t of iron ore a day. The processed iron ore products are transported to Narvik port via the Malmbanan and Ofotbanen mine railway lines.
اقرأ أكثر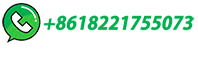
Production and Technology of Iron and Steel in Japan …
The purposes of this partnership include the establishment of an innovative iron and steel manufacturing process that reduces carbon emissions by integrating Nippon Steel's steel making technologies and Rio Tinto's iron ore processing technologies by a wide-ranging study of technologies for decarbonization in the total value chain of steel ...
اقرأ أكثر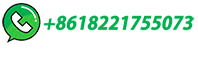
Ironmaking 101 – From Ore to Iron with Blast Furnaces
Figure 1 Drawing of an ironmaking blast furnace with hot-blast stove. Source: The German Steel Federation (WV Stahl) In order to make steel, iron must be extracted or won from iron ore. Blast furnacing, smelting and direct iron reduction are the current ironmaking processes.
اقرأ أكثر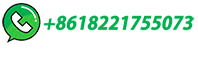
Iron Ore: Mineralogy, Processing and Environmental …
Iron Ore: Mineralogy, Processing and Environmental Sustainability, Second Edition covers all aspects surrounding the second most important commodity behind oil. As an essential input for the production of crude steel, iron ore feeds the world's largest trillion-dollar-a-year metal market and is the backbone of the global infrastructure. The book …
اقرأ أكثر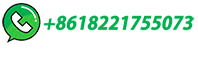
Innovating Beyond Tradition: Iron Ore Processing Technologies
In conclusion, iron ore processing technologies have come a long way from traditional beneficiation methods, ushering in a new era of efficiency, sustainability, and value creation for the mining ...
اقرأ أكثر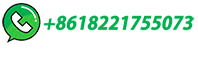
Evolving landscape: the future of Australia's iron ore industry
Australia maintained its iron ore production at around 945 million tonnes (mt) in 2023, with a 3.1% increase projected for 2024, GlobalData reports.By 2030, production is expected to reach 1.22 billion tonnes (bt), driven by various upcoming projects and expansions, including the Onslow project (2024), the Jimblebar Expansion project …
اقرأ أكثر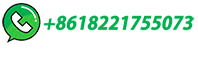
Circored Fine Ore Direct Reduction – a proven …
Outotec's Circored technology is the only process for iron ore reduction based on hydrogen that has proven its functionality and performance in an industrial-scale demonstration plant. …
اقرأ أكثر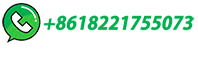
From Ancient to Modern Methods
One of the earliest known methods of iron smelting was the bloomery process. This ancient technique, dating as far back as 1200 BCE, involved heating iron ore in a furnace with …
اقرأ أكثر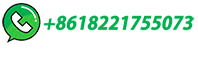
Iron Ore Processing, General
Iron ore handling, which may account for 20–50% of the total delivered cost of raw materials, covers the processes of transportation, storage, feeding, and washing of the ore en route to or during its various stages of treatment in the mill.. Since the physical state of iron ores in situ may range from friable, or even sandy materials, to monolithic …
اقرأ أكثر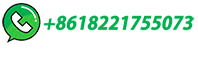
Pilot-Scale Demonstration of Ilmenite Processing …
Ilmenite Processing Technology Duluth Laboratories & Administration 5013 Miller Trunk Highway Duluth, Minnesota 55811 ... were prepared to operate a continuous counter-current process for the extraction of iron and ... powder product from mining 0.5 Mtpa crude ore. The high-level cost estimate found that the total OPEX for a 60,000 tpa TiO 2
اقرأ أكثر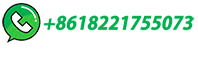
NRRI advances efficient grinding technology on the Iron Range
A crucial step in mineral processing – and in Minnesota's iron ore processing – is comminution, a process of crushing and grinding. Large rocks must first be …
اقرأ أكثر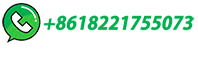
Introduction: Overview of the global iron ore industry
The company has the two largest iron ore mining and processing operations in the country, which are located at Lebedinsky and Mikhailovsky in the Kursk Region (see Fig. 1.32). The Lebedinsky mine is shown in Fig. 1.33. ... Despite development and deployment of leading-edge technologies, the iron ore industry comes with its fair …
اقرأ أكثر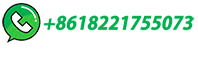
Kumba to invest further $428 mln in iron ore processing …
South Africa's Kumba Iron Ore will invest an additional 7.6 billion rand ($428 million) in processing technology that will treble premium quality production at its Sishen mine, it said on Thursday.
اقرأ أكثر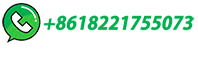
From Ore to Alloy: Navigating Ironmaking in Modern Steel …
At the heart of steel production lies the intricate process of ironmaking, where iron ore is transformed into molten iron and eventually alloyed to create various grades of steel. This article delves into the journey from ore to alloy, exploring the technologies, challenges, and innovations that shape modern ironmaking. 1. Iron Ore: Source of ...
اقرأ أكثر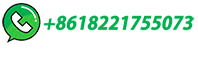
Plasma Processing of Iron Ore
The depletion of high-grade ore minerals and the scarcity of fossil fuel reserves are challenging factors for metallurgical industries in the future. Also, extensive mining for increased steel demand results in the generation of fines often found unsuitable for use as direct feedstock for the production of metals and alloys. Apart from mines …
اقرأ أكثر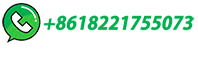
From Ancient to Modern Methods
As societies progressed, humans began to extract iron from terrestrial sources, marking the transition from the use of meteoric iron to smelting iron ore. One of the earliest known methods of iron smelting was the bloomery process. This ancient technique, dating as far back as 1200 BCE, involved heating iron ore in a furnace with charcoal.
اقرأ أكثر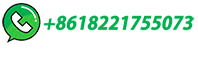
Dry beneficiation of iron ore
3 Technologies for iron ore beneficiation. Depending on iron content, beneficiation of iron ore for sale is a relatively simple to complex process. ... Fig. 4 shows the process stages of a possible iron ore beneficiation for magnetite ores or also siderite and taconite ores that have only a low to medium iron content. After comminution and ...
اقرأ أكثر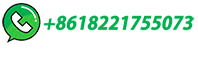
Iron ore beneficiation: an overview
Dry processing of iron ore: In dry processing of iron ore, ROM is generally crushed below 40 mm through three-stage crushing and thus segregated by screening into 10–40 and −10 mm fractions. For softer ore, tumbler index is generally low and hence lump ore is crushed below 10 mm to produce fine product. Yield from the plants has …
اقرأ أكثر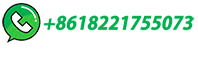
NRRI advances efficient grinding technology on the Iron …
A crucial step in mineral processing – and in Minnesota's iron ore processing – is comminution, a process of crushing and grinding. Large rocks must first be crushed and then ground down to tiny particles to expose the valuable or desired minerals so they can be separated from the waste rock. The prevalence of low-grade …
اقرأ أكثر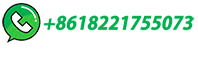
Iron Ore: Mineralogy, Processing and Environmental …
Iron Ore: Mineralogy, Processing and Environmental Issues summarizes recent, key research on the characterization of iron ores, including important topics such as beneficiation (separation and refining), agglomeration (e.g., production of pellets or powders), blast furnace technology for smelting, and environmental issues relating to …
اقرأ أكثر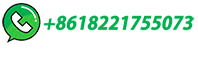
Iron Ore Processing, General
1 Introduction. Iron is the world's most commonly used metal–steel, of which iron ore is the key ingredient, representing almost 95% of all metal used per year. It is …
اقرأ أكثر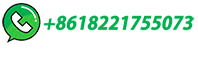