The Cement Plant Operations Handbook
Providing a comprehensive guide to the entire cement production process from raw material extraction to the finished product, the industry's favourite technical reference book is …
اقرأ أكثر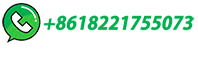
Roller Press
Simply put, the roller press is the most energy-efficient grinding machine on the market. Since its commercial introduction into the cement industry by KHD in the 1980s, hundreds of them have been installed in the cement …
اقرأ أكثر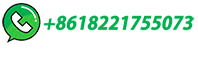
The 6 Main Process Fans in Cement factory
In cement industry raw mill exhaust fans handle 2.2 ton of exhaust gases for the production of 1 ton of clinker. Raw mill exhaust fans are operated with very adverse situations because the fan handles mainly gases such as CO2, N2, …
اقرأ أكثر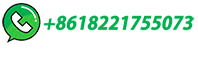
How Cement is Made
The raw cement ingredients needed for cement production are limestone (calcium), sand and clay (silicon, aluminum, iron), shale, fly ash, mill scale, and bauxite. The ore rocks …
اقرأ أكثر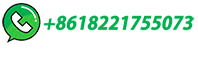
Vertical roller mills | FL Cement
Whether grinding raw coal, clinker, cement and/or slag, we have a VRM solution to suit your grinding needs. What's more, our online condition monitoring services enable you to adopt a proactive maintenance strategy for your OK™ and ATOX® mills that eliminates unexpected downtime and ensures continuous high performance.
اقرأ أكثر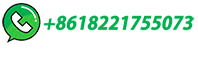
Cement Plant Process Attendant, Roller Mill | Midlothian, TX
Exposure to cement, clay, limestone, and various lab chemicals. See MSDS for more details; WORKING CONDITIONS Works in all weather conditions including heat, cold, ice, rain, and in high humidity, and is required to work in all plant environments. Incumbents will be exposed to vibrating equipment and mechanical and electrical hazards and heights. .
اقرأ أكثر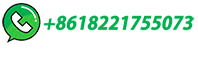
Plants | JK Cement
Clinker and gypsum are fed to the cement mills through electronic weigh feeders at controlled rate and ground in ball mills. The classifier (high efficiency separator) controls the fineness of white cement. The finished product of desired chemical composition and physical properties is transported to Cement Silos for storage.
اقرأ أكثر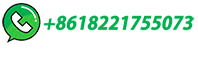
Top 35 Cement Companies in India
India is the 2nd largest producer of cement in the world. The Indian Cement Industry comprises of 125 large cement plants with an installed capacity of 148.28 million tonnes and more than 300 mini cement plants with an estimated capacity of 11.10 million tonnes per annum.
اقرأ أكثر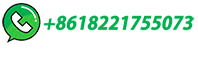
Cement
Cement - Extraction, Processing, Manufacturing: Raw materials employed in the manufacture of cement are extracted by quarrying in the case of hard rocks such as limestones, slates, and some shales, with the aid of blasting when necessary. Some deposits are mined by underground methods. Softer rocks such as chalk and clay can …
اقرأ أكثر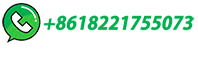
The Cement Plant Operations Handbook
Finish mill – 12. Cement – 13. Quality control – 14. Packing and distribution – 15. Emission abatement (dust, NO x, SO 2, etc) – 16. Maintenance – 17. Process – 18. Materials analysis –19. Plant capacity summary – 20. Storage capacity 15. Cement plant construction and valuation 244 1. New plant construction – 2.
اقرأ أكثر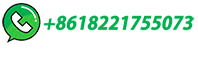
PROCESS CONTROL FOR CEMENT GRINDING IN …
the capacity of grinding and drying of mill. The grindability affects the capacity of grinding, type of mill and roller pressure. The capacity of the mill is calculated Using G K * D 2.51 Where, G is capacity of the mill, K1 is roller mill coefficient and D is table diameter. 2. PROCESS CONTROL OF VRM The conventional control system of VRM
اقرأ أكثر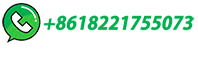
OPTIMIZATION OF CEMENT GRINDING OPERATION IN …
Optimization of the Cement Ball Mill Operation . Optimization addresses the grinding process, maintenance and product quality. The objective is to achieve a more efficient operation and increase the production rate as well as improve the run factor. Consistent quality and maximum output with lower specific power consumption
اقرأ أكثر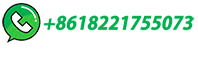
Improving Mill Shoe Bearing Reliability and Productivity
What are the causes for an increase of Cement Mill trunnion Bearing temperature and what are the possible solutions . Cement mill trunion bearing temperature may increase due to following reasons: 1. HP pump pressure is low. 2. Cutoff time of HP pump after mill start up; 3. Mixing of contamination with oil; 4. LP pump oil flow is less; 5.
اقرأ أكثر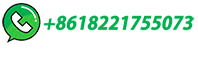
CEMENT FORMULAE HANDBOOK
I would request all the readers to make full use of this Cement Formula Handbook (version 3.0) and share it with colleagues and contemporaries. As always, your comments ... 10 Grinding Mill Investigation 25 11 Tromp Curve Calculation and Significance 27 ... 23 Details on Waste Heat Recovery (WHR) 56 24 Miscellaneous Formulae 64
اقرأ أكثر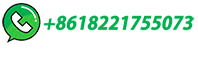
OCCUPATIONAL HEALTH AND SAFETY IN CEMENT INDUSTRY
Dust emissions are one of the most significant impacts of cement manufacturing and associated with handling and storage of raw materials (including crushing and grinding of raw materials), solid fuels, transportation of materials (e.g. by trucks or conveyor belts), kiln systems, clinker coolers, and mills, including clinker and limestone burning and …
اقرأ أكثر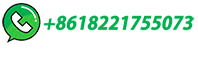
Cement grinding Vertical roller mills VS ball mills
Vertical roller mills and ball mills represent two clearly distinct technologies. However, with proper adjustments to the operational parameters of the vertical roller mill almost identical cement properties can be achieved by the two mills that satisfy the cement user's demands.Nevertheless, the two types of mills have their distinctive merits.
اقرأ أكثر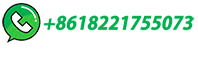
Cement Mill Optimization: Practical Strategies for …
Let's explore some practical strategies with real-world figures and numbers: Adjusting mill parameters: Fine-tuning mill parameters such as mill speed, ball charge, filling ratio, and grinding media size can have a substantial …
اقرأ أكثر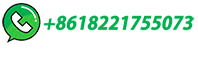
Ball motion, axial segregation and power consumption in a full …
The internal shell diameter of the first chamber is 3.85 m and it is 4.3 long.It has a wave liner fitted consisting of 36 liner plates around the circumference. Fig. 1 shows the internal structure of the first chamber of the cement mill. Fig. 2 shows a close up of the lifter plates whose profile consists of a gradual rise to a high point followed by an abrupt …
اقرأ أكثر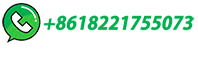
Cement grinding Vertical roller mills VS ball mills
Cement vertical roller mills are not typically fully enclosed in a building (Figure 9). In many cases the mill is covered with a roof to protect the separator drive. The noise level from …
اقرأ أكثر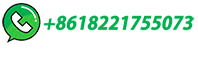
Hardie® Plank Lap Siding
Protect and transform your home with our best-selling product line from the #1 brand of fiber cement siding in North America*, available in stunning finishes to suit every style. Showing products for: typeSlug: exterior-siding-products productSlug: hardie-plank-lap-siding variantSlug: collectionSlug: familySlug: colorSlug:
اقرأ أكثر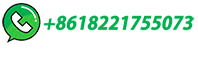
Welcome to Tanga Cement PLC | Simba Cement – Tanga Cement …
Tanga Cement PLC is a producer of Simba Cement brands in Tanzania. Simba Cement is the result of careful research and development by our cement engineers and scientists. It is specially blended with good quality control monitoring systems, high quality cement engineered for use in all structural, building and particularly useful in marine and ...
اقرأ أكثر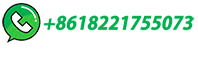
Mills Concrete LLC | Business Details
Mr. Jeremy Mills, Owner Referral Assistance Pennsylvania Attorney General List of Registered Contractors 16th Floor, Strawberry Square Harrisburg PA 17120 Phone Number: (888) 520-6680 Fax Number ...
اقرأ أكثر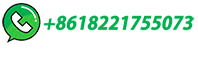
Energy-Efficient Technologies in Cement Grinding
In this chapter an introduction of widely applied energy-efficient grinding technologies in cement grinding and description of the operating principles of the related equipments and comparisons over each other in terms of grinding efficiency, specific energy consumption, production capacity and cement quality are given. A case study …
اقرأ أكثر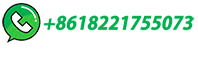
How Cement is Made
Stage of Cement Manufacture. There are six main stages of the cement manufacturing process. Stage 1: Raw Material Extraction/Quarry The raw cement ingredients needed for cement production are limestone (calcium), sand and clay (silicon, aluminum, iron), shale, fly ash, mill scale, and bauxite. The ore rocks are quarried and crushed into smaller …
اقرأ أكثر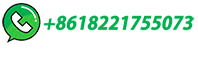
Synchronous and slip-ring induction motors drive cement mills
Abstract: In the process of selecting a suitable motor for a cement mill, there are several issues to consider that, for the purpose of analysis, can be grouped into two distinct categories. The first category is the technical analysis, which is based on engineering considerations that evaluate the merits of either a synchronous or a slip-ring induction …
اقرأ أكثر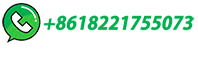
Home
"OPC, PPC and PSC cements of Jagdamba Cement produced by Jagdamba Cement Industries Pvt. Ltd and Shubhashree Jagdamba Mills Pvt. Ltd. have been surpassing the benchmarks of best quality. We have been using Jagdamba Ultra Premium OPC Cement in high quantity in our big projects all over the country. ... Shubha Shree Jagdamba …
اقرأ أكثر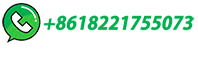
Cement Plants
Cement Plants; BIRLAPUR (Jute Mill, Hospital, School) KOLKATA (Corporate & Registered Offices, Jute Mill) NEW DELHI (Office) MUMBAI (Office) RCCPL Private Limited (formerly Reliance Cement Company …
اقرأ أكثر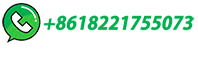
Consumables for Cement Industry
We supply the complete range of wear resistant casting and grinding media balls. We supply entire set of castings, diaphragm and balls for cement mill, raw mill and coal mill. We also supply hammers, vertical mill rollers, kiln plate, and castings for mining and other applications. Please write to us for more details.
اقرأ أكثر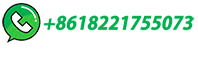
Facilities
Key details. Receives blast furnace Slag and Fly ash from JSW Steel Limited and JSW Energy Limited, respectively; Green power of 8.00 MW (solar) used in the manufacturing process ... JSW Green Cement Pvt Ltd, Chandramouli Silk Mills, Plot no. C - 3A, MIDC, TTC Industrial Area, Pawane, Turbhe, Navi Mumbai - 400705 Sambhajinagar Captive …
اقرأ أكثر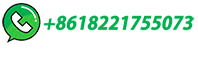