Grinding in Ball Mills: Modeling and Process Control
Grinding in ball mills is an important technological process applied to reduce the size of particles which may have different nature and a wide diversity of physical, mechanical …
اقرأ أكثر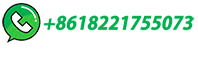
Grinding in Ball Mills: Modeling and Process Control
The paper presents an overview of the current methodology and practice in modeling and control of the grinding process in industrial ball mills. Basic kinetic and energy models of the grinding ...
اقرأ أكثر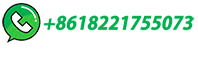
Differences Between Wet and Dry grinding: Why Choose …
In essence, grinding is a transformative process, bridging the gap between raw materials and their final applications. Wet vs. Dry Ball Milling. Ball milling is a popular grinding method. The wet ball milling process involves a drum filled with grinding media, like metal balls, and the material to be ground.
اقرأ أكثر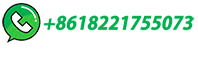
Optimization of Cement Grinding Operation in Ball Mills
Cement ball mills typically have two grinding chambers. The first chamber is filled with larger diameter grinding media and lined with lifting liners. The first chamber coarse-grinds the feed material and prepares it for the second chamber. ... Clinker, Gypsum and other desired additives are fed to the ball mill in specific proportions based on ...
اقرأ أكثر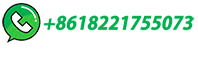
Improvements in New & Existing Cement …
o < 20% of energy absorbed is reckoned to be converted to useful grinding: the bulk is lost as heat, noise, equipment wear & vibration; o For ball mills, only 3 – 6% of absorbed energy is utilized in surface …
اقرأ أكثر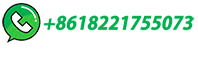
V &RQI 6HU Design of New Slotted Structured Grinding …
Laboratory experimental work was also conducted to study the effect of various types of grinding additives on product fineness and compressability. Triethanolamine (TEA), Ethylene Glycol (EG) and CEMEX (commercial grinding additives) was tested at various dosage in ball grinding mill at fixed grinding condition (ball size, speed and filling ratio).
اقرأ أكثر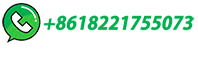
On the analysis of fine wet grinding in a batch ball mill
The influence of the slurry density on the fine wet grinding performances of a batch ball mill was examined for an alumina hydrate feed. Irrespective of the operating conditions, the size reduction process proceeds fast in the first period of grinding (20 min); then its rate progressively reduces and after 1–2 h the size of the product approches a …
اقرأ أكثر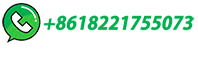
Grinding Mills | Mineral Processing Equipment | CITIC HIC
High cost-effectiveness CITIC HIC grinding mills are recognized as China's Manufacturing Industry Single Champion Product. CITIC HIC is responsible for setting the national standards of semi-autogenous mills (SAG mills) and ball mils, supported by powerful database, optimized process technology, cutting-edge design concept, and 60 years of …
اقرأ أكثر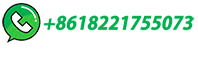
Horizontal roller mill (Horomill®) application versus hybrid HPGR/ball
Industrial scale Horomill ® and hybrid HPGR/two-compartment ball mill applications at puzzolanic portland cement production were presented with emphasis on the general operational characteristics of the circuit configurations, size reduction and energy efficiencies of the Horomill ® and two-compartment ball mill grinding conditions. …
اقرأ أكثر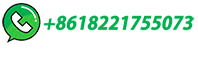
Principles of Grinding in Ball Mills
Find out more about the principles of grinding in ball mills from Orbis Machinery, LLC. Call us today for more information 262-522-1939.
اقرأ أكثر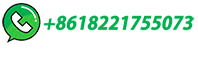
XRF Sample Preparation Equipment| Chemplex Industries, Inc.
SpectroMicronizing® Mill; Ball Impact. SpectroMill® Ball Impact Grinder/Mixer ; SpectroVial® Grinding/Blending Vials; ... Grinding & Briquetting Additives. Fusion. Fluxer G-Series. Platinum Ware. Petrochemical Standards. SpectroStandard® PE & PVC. XRF & XRD Chemical Kits. Sample Cup Accessories.
اقرأ أكثر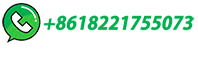
_Taurus
NETZSCH Taurus Ball Mill, the pinnacle of fine and ultra-fine grinding technology. ... Conductive additives. Blog. 08.09.2023. NETZSCH - next level in battery research. Event. 07.10.2024 – 10.10.2024 Fair. Detroit, MI, United States. The Battery Show. ... NETZSCH Taurus has the most advanced technology in Mills using Grinding Media for ...
اقرأ أكثر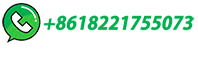
Optimizing cement grinding with chemical additives
Grinding additives assist with de-aeration in front of the grinding roll, which allows for smoother operation (less vibration) as well as better dispersion at the nozzle ring and in …
اقرأ أكثر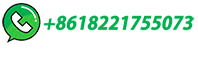
The influence of suspension properties on ultra-fine grinding …
Therefore, all the grinding experiments described in the following were carried out with a concentration of 0.5%. 3.2. Grinding resultsFrom literature, it is known that the grinding results in stirred ball mills are generally not influenced by the solid concentration for a fixed value of the specific energy.
اقرأ أكثر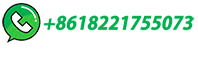
Balls, iron/steel, forged/stamped for grinding mills
Between 2021 and 2022 the exports of Balls, iron/steel, forged/stamped for grinding mills grew by 25.9%, from $1.33B to $1.67B. Trade in Balls, iron/steel, forged/stamped for grinding mills represent 0.0071% of total world trade. Balls, iron/steel, forged/stamped for grinding mills are a part of Other Iron Products.
اقرأ أكثر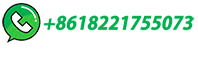
A critical review on the mechanisms of chemical additives …
Halasyamani et al. [42] investigated the effect of pH on the grinding of quartz and calcite with HCl and NaOH in a ball mill. The maximum grinding efficiency for quartz was at pH 7 and was attributed to the dispersion effect since its PZC was at pH 2.
اقرأ أكثر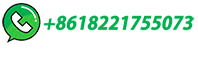
PAPER OPEN ACCESS …
Grinding aid or grinding additives refer to substa nces which when mixed into the mill contents cause an increase in rate of size reduction and flowability. Grinding process of clinker was carried ...
اقرأ أكثر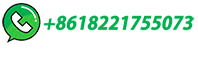
How it Works: Crushers, Grinding Mills and Pulverizers
Ball mills typically use water or other liquid and additives to help reduce friction and provide cooling during the grinding process. The feed enters one end of the ball mill, and discharges out the other end. Ball mills vary greatly in size, from large industrial ball mills measuring more than 25 ft. in diameter to small mills used for …
اقرأ أكثر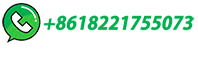
What is a Ball Mill Explained: In-Depth Guide
Critical Speed: Critical speed is the hypothetical speed at which the centrifugal force is equal to the gravitational force, and the grinding media starts sticking to the inner shell of the equipment instead of falling freely.Grinding at or close to critical speed of the mill yields a poorer grinding efficiency. The ball mills are mostly operated at 65 …
اقرأ أكثر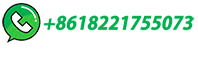
Cement Clinker Grinding Aids
One research route that has been explored for about half a century is the development of additives to the grinding mill feed that substantially improve the efficiency of grinding. ... 1973)1 the use of silicones in the ball mill grinding of quartz (Gilbert, 1962); and the use of acetone, carbon tetrachloride, benzene, and nitromethane in the ...
اقرأ أكثر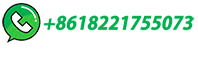
Grinding Aids
As previously stated, in dry grinding the additive may be present, at least in theory, in solid, liquid, vapour or gaseous form and some of the most interesting results of the use of these additives are reported from the cement industry. ... The researches of Schweitzer and Craig into the grinding of cement clinker, in a laboratory ball mill ...
اقرأ أكثر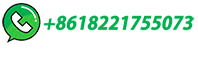
Effect of chemical additives on the dynamics of grinding …
DOI: 10.1016/0301-7516(85)90044-4 Corpus ID: 95831855; Effect of chemical additives on the dynamics of grinding media in wet ball mill grinding @article{Fuerstenau1985EffectOC, title={Effect of chemical additives on the dynamics of grinding media in wet ball mill grinding}, author={Douglas Winston Fuerstenau and …
اقرأ أكثر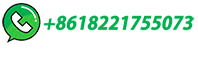
Cement Additives
Grinding Aids are used in the cement mill (Ball Mill, Vertical Roller Mill, HoroMill) to increase the productivity, save electrical energy and/or to increase the fineness and improve defined cement properties, e.g. powder flowability. A typical example is SikaGrind®-400.
اقرأ أكثر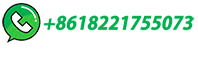
`Grinding Aid Effectiveness in Cement Ball Mill
Grinding Aid Effectiveness in Cement Ball Mill Web: Email: bulawali@gmail, ali@bulawali LinkedIn: Ali Bulawali The introduction of the grinding aid (GA) has been started more than 50 year ago, to facilitate clinker grinding in cement mills improve mill output despite of the above features, the wear of mill interior …
اقرأ أكثر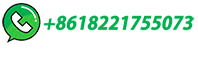
Improvement of cement performances through the use …
In addition, the use of a suitable grinding aid can improve the particle size distribution of cement and positively influence clinker hydration, thus improving the cement quality. …
اقرأ أكثر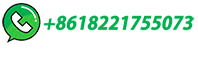
Effect of grinding aids on the grinding energy consumed during grinding
In an experiment using a stirred ball mill and grinding aids (Paramasivam and Vedaraman, 1992, Sureshan and Moothedath, 1992, Fuerstenau, 1995, Wang and Forssberg, 1995, Hasegawa et al., 2001, Oettel and Husemann, 2004), Paramasivam and Vedaraman (1992) studied the effect of the physical properties of liquid additives on dry …
اقرأ أكثر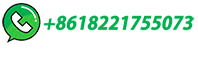
Review of the Effect of Grinding Aids and Admixtures on the …
Grinding aids (GAs), also called grinding additives are introduced in liquid or solid form in the ball mill or vertical cement mills during grinding because of their anticipated merits. They can be divided into amines and their salts, polyalcohols, lignosulfonates, fatty acids, and fatty acid salts based on their chemical makeup [ 1 ].
اقرأ أكثر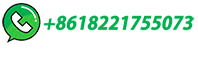
Energy-Efficient Technologies in Cement Grinding
The comminution efficiency of a HPGR is better than ball mills such that it consumes 30–50 % of the specific energy as compared to a ball mill. Four circuit configurations of HPGR can be used in grinding of raw materials, clinker and slag such as : Pre-grinding unit upstream of a ball mill. Hybrid grinding. Semifinish grinding
اقرأ أكثر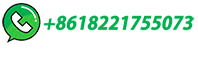
Ball Mill Grinder | Wet & Dry Grinding Ball Mill
Ball Mill Grinder. Our ball mill grinder is a versatile tool designed for grinding and blending materials into fine particles. Its cylindrical chamber houses the grinding medium—be it metallic or ceramic balls—allowing for smooth, efficient milling.
اقرأ أكثر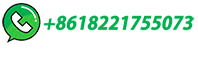
Improvement of cement performances through the use …
(VRM) are slowly, but steadily, outnumbering horizontal ball mills. Vertical cement mills are able to reach production values which are significantly higher than the ones achievable with traditional ball mills, in some cases up to 300 t/h. Empirically, It can be ... one of the newly developed cement grinding additives for vertical rollers mill.
اقرأ أكثر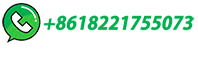