Synthesis of nitrogen‐doped graphene catalyst by high‐energy wet ball
In this research, nanoscale high-energy wet ball milling methodology was investigated as an effective synthesis method for N-G catalysts by using graphene oxide and melamine as raw materials. The main purpose is to study reaction mechanism of the synthesis process and the physical, chemical, and electrochemical properties of N-G …
اقرأ أكثر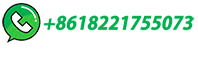
MILLING METHODS COMPARISON GUIDE
Media milling employs a medium rather than internal moving machine parts to use impact, abrasion, and attrition to reduce particle size. Media milling can be wet or dry. Jet milling …
اقرأ أكثر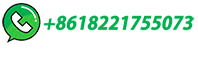
Industrial Ball Mill Grinder Machines | Thomas Scientific
Industrial Ball Mill Grinder Machines are essential tools in various Scientific and industrial applications, primarily used for grinding and blending materials to achieve uniform consistency and fine particle sizes. ... M 20 Universal Mill. ... Pellets for wet or dry milling Long wearing for non-contaminating grinding Tough, hard, non-porous ...
اقرأ أكثر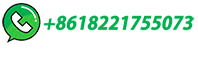
WET BALL MILL OF FLEXIBLE BASE
WET BALL MILL OF FLEXIBLE BASE TXDOT DESIGNATION: TEX-116-E CONSTRUCTION DIVISION 3 – 4 EFFECTIVE DATE: APRIL 2024 REVIEW DATE: APRIL 2024 PART II—WET BALL MILL PERCENT INCREASE PASSING THE NO. 40 SIEVE 4. PROCEDURE 4.1 Weigh a 3,000 ± 50 g (6.6 ± 1.1 lb.) sample using the bulk gradation …
اقرأ أكثر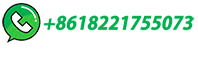
Laboratory Ball Mill
Labmate's Ball Mill is an advanced material blending device that utilizes rotating steel balls to create a finely homogenized blend of materials within a precisely controlled setting. It …
اقرأ أكثر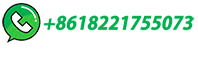
Ball Mills
Unique designs & various ball mill drive options, including standard shaft mount, gearwheel, pinion & direct drive ball mills and more.
اقرأ أكثر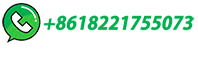
Wet milling
Wet milling Wet milling with IKA's inline machines is a safe and efficient alternative to dry grinding. ... Universal mixing plant, consisting of vessel, agitator, dispersing machine and electric control with HMI: Efficient mixing, dispersing, heating/cooling and optimal feeding of additives during production of emulsions and suspensions ...
اقرأ أكثر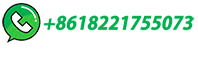
Pharmaceutical nanocrystals: production by wet milling and …
Nanocrystals are produced in the form of nanosuspensions using top-down (e.g., wet milling or high pressure homogenization) and bottom-up methods (e.g., …
اقرأ أكثر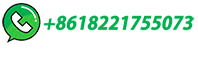
Scaling Energy Transfer in Ball Mills: A Scale-Agnostic …
Ball mills are widely used for size reduction in mineral processing, but effective scaling from laboratory to industrial scale remains challenging. This study introduces a novel scaling constant approach to replicate energy transfer to ore during milling across different scales by adjusting rotational speed and grinding medium size …
اقرأ أكثر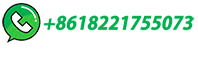
Aggregate Wet Ball Mill – Rainhart
The Rainhart Aggregate Wet Ball Mill is used to determine the resistance of aggregate in flexible base materials to disintegration in the presence of water. These results are essential in determining whether the base will resist crushing, degradation, disintegration, and premature structural failure.
اقرأ أكثر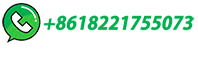
Ball Mill Manufacturer | Neumann Machinery Company
Supplier of Continuous Feed Ball Mills for Wet & Dry Grinding Applications. Founded in 1984 with the acquisition of the EIMCO ball, pebble and rod mill product lines. Neumann Machinery Company (NMC) is headquartered in West Jordan, Utah, in the USA just 14 miles south of Salt Lake City. The area is steeped in a rich history in the supply of ...
اقرأ أكثر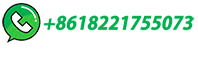
Ball Mill Design/Power Calculation
A wet grinding ball mill in closed circuit is to be fed 100 TPH of a material with a work index of 15 and a size distribution of 80% passing ¼ inch (6350 microns). The required product size distribution is to be …
اقرأ أكثر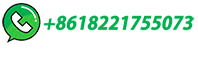
AMIT 135: Lesson 7 Ball Mills & Circuits – Mining …
Mill Type Overview. Three types of mill design are common. The Overflow Discharge mill is best suited for fine grinding to 75 – 106 microns.; The Diaphram or Grate Discharge mill keeps coarse particles within the mill …
اقرأ أكثر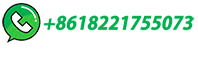
Ball milling: a green technology for the preparation and
The use of ball milling as a defibrillation method after a series of pre-treatments of raw materials was also described by the group of Elkoun, who reported the extraction of CNFs and CNCs from carrot pulp by ball milling and acid hydrolysis respectively. 60 More in detail, NFCs were obtained from never dried carrot pulp (4%) by ball milling ...
اقرأ أكثر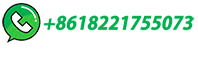
Wet Ball Milling Method and Technology
Wet grinding, a subset of the wet milling process, involves the reduction of particles in a liquid medium. Unlike dry grinding, where contact with air can lead to undesirable …
اقرأ أكثر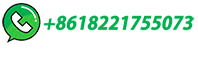
Ball Mill Grinder | Wet & Dry Grinding Ball Mill | Labotronics
Our ball mill grinder is a versatile tool designed for grinding and blending materials into fine particles. Its cylindrical chamber houses the grinding medium—be it metallic or ceramic balls—allowing for smooth, efficient milling. Widely used in industries such as mining, ceramics, and pharmaceuticals, this grinder operates through rotation ...
اقرأ أكثر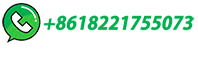
Atmosphere matters: The protection of wet ball milling …
Na 2 S 2 O 4, biochar, and micron iron were reunited by wet and dry ball milling. • Wet ball milling promoted faster and complete Cr(VI) removal (100 % in 80 min) • The composite of wet ball milling presented excellent anti-ageing property. • Higher electron selectivity was obtained (59.15% for wet and 46.72% for dry) •
اقرأ أكثر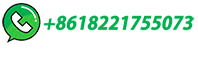
Ball Mills
Available cylinder sizes range from laboratory mills to 12′ in diameter.. Discharge Features. For discharge of the product on wet grinding processes we offer our standard media retention grate along with an …
اقرأ أكثر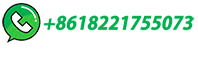
Energy-Mass-Size balance model for dynamic control of …
A dynamic model is developed for a wet overflow ball mill based on a set of mass and energy balances to simulate the mill. The energy balance relies on temperature and mass flow data. The key control parameters to be measured are mill temperature (feed and discharge streams), mill power draw and the mass flow rate in the feed stream.
اقرأ أكثر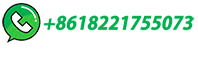
Rubber Ball Mill Liner Wear Rate Estimation
Secondary Grinding Ball Mills experience 1-2 years of liner life, depending on tonnage/ball size. Normally Lifter to Plate ratio is 1:2.Tertiary Grinding Ball Mills experience up to 4 years of liner life. Since, all the mills are unique in their operation and the practical sense in which they run, we do wear measurement during every shutdown.
اقرأ أكثر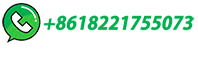
Laboratory Ball Mills | Bench and Floor Jar Mills
Jar Mills are available in bench or floor models and have one to six jar capacities in 1, 2 or 3 tiers. They are used for wet or dry grinding, mixing and blending of ores, chemicals, ceramics, glass, and more. Benchtop Labmill is lightweight and compact and easily adjusts to four sizes of milling jars, 16-320oz (0.5–10L). Jars made of High-Density …
اقرأ أكثر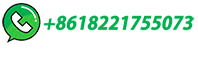
Wet Ball Mill for Metal Ores and Non-ferrous …
Buy wet ball mill from trusted wet grinding ball mill supplier. Energy saving wet ball mill, small energy consumption, large productivity, effectively improving grinding efficiency.
اقرأ أكثر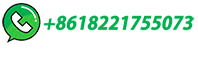
Exploring ball milling theory: A comprehensive guide
Ball milling is a mechanical process that involves the rotation of a drum containing grinding media, typically steel balls, at a high speed. The materials to be milled are loaded into the drum, and as the drum rotates, the grinding media collide with the materials, causing them to break down and reduce in size. ...
اقرأ أكثر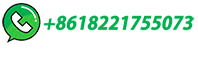
Everything You Need to Know About Wet Media …
Toll processors have a range of wet and dry milling methods at their disposal to achieve incredibly fine gauge powders. Wet grinding — also called wet media milling — is often the preferred process for particle …
اقرأ أكثر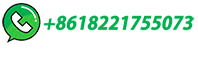
DYNO®-MILL UBM
Unique milling principle for universal use in wet-milling technology The DYNO®-MILL UBM milling principle The new generation of DYNO®-DISC BC agitator discs was specially developed for this series. These feature unique Bead Channels in combination with a closed outer contour. DYNO®-DISC BC Bead channel The bead channels ensure the efficient ...
اقرأ أكثر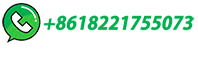
Universal wet-milling technique to prepare oral nanosuspension …
The wet-milling in aqueous phase was executed by three types of beads-milling equipment, which were newly developed, to prepare the drug nanosuspension. Among them, the oscillating beads-milling apparatus was mainly used, which is applied to the middle manufacturing scale in this research. ... The simple and universal technique …
اقرأ أكثر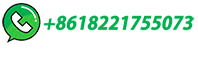
Modern Wet Milling and Material Processing
Grinding media for ball mills ranges in size from 6 - 10 mm for most traditional applications and 1.5 - 2.0 mm for vertical mills. Typical ball mills use high-alumina or porcelain balls for their density, but wear …
اقرأ أكثر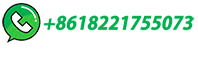
The Ultimate Guide to Understanding Ball Mill Diagrams
The ball mill can be operated in a wet or dry way, depending on the material properties and the intended use. The wet ball mill is usually preferred when the material to be ground is wet, such as in the case of ore processing. On the other hand, the dry ball mill is suitable for grinding dry materials, such as cement, limestone, and coal. ...
اقرأ أكثر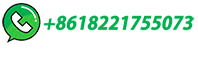
Impact of water combined wet ball milling extraction and …
Wet ball milling resulted in increased exposure of polar groups in molecules and elevated surface charge of water/wet ball milling-treated CFs (as indicated in Table 4). This enhancement promoted electrostatic interactions among molecules, as well as between the molecule and the solvent, thereby increasing the flow resistance of the …
اقرأ أكثر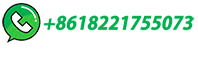
0.5 to 15 TPH Small Scale Miner's Ball Mill
In general, ball mills can be operated either wet or dry and are capable of producing products on the order of 100 um. This duty represents reduction ratios as great as 100. The ball mill, an intermediate and fine-grinding device, is a tumbling drum with a 40% to 50% filling of balls. The material that is to be ground fills the voids between ...
اقرأ أكثر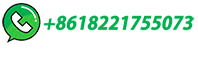