5/22/2015 Articles
5/22/2015 Articles - Production of Sponge Iron through Tunnel Kiln Process I IPFOnline 1/2 1 .php IPF online India's Only Industrial product portal
اقرأ أكثر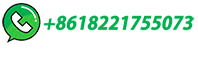
Sponge Iron Through Tunnel Kiln Process
Rotary Kiln Process of Making Sponge Iron C. A typical process scheme for making sponge iron in a rotary kiln is presented in Fig. 2.1. While Fig. 2.1 shows only the key steps, a more detailed scheme, as it would appear for a typical operating plant, is presented in Fig. 2.2. 2.3 SPONGE IRON PILOT PLANT OF RDCIS SAIL The sponge iron Pilot …
اقرأ أكثر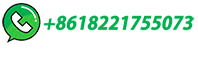
Chapter 1 Review of Sponge Iron Making Process …
Review of Sponge Iron Making Process Historical Development: Sponge iron was the main source of iron for many centuries before the blast furnace technology of iron …
اقرأ أكثر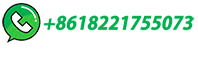
Sponge Iron production from ore -coal composite pellets in Tunnel Kiln
However, Rotary kiln process suffers from serious limitations like low productivity and pollution. In this respect fixed bed Tunnel kiln furnace are evolving as an alternative to Rotary kiln process. Iron ore fines and the low grade beneficiated iron ore cake are directly used for manufacturing of sponge iron in tunnel kilns.
اقرأ أكثر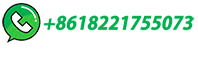
New Sponge Iron Rotary Kiln Design In Sponge Iron Manufacturing Process
Then the mixture enters the reduction zone of sponge iron rotary kiln, and the iron concentrate is reduced by carbon monoxide to form iron elements. During the sponge iron manufacturing process, hot air enters through the air tube and air nozzle of the sponge iron kiln, providing heat for the reaction.
اقرأ أكثر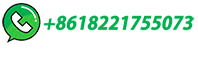
Sponge Iron
DRI, also known as sponge iron, is the product of reducing iron oxide in the form of iron ore and steel plant wastes into metallic iron, below the melting point of iron and typically in the range of 800–1200 °C. Iron oxide is charged into shaft furnace, rotary kiln, or fluidized beds in the form of pellet, iron ore lumps, or fines. The reduction takes place using …
اقرأ أكثر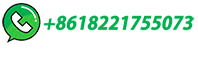
Conversion of Sponge Iron From Low Grade Iron ore And …
DOI: 10.9790/1684-1305064954 50 | Page Conversion of sponge iron from low grade iron ore and mill scale through simulating tunnel kiln (B) Rotary Hearth Process The iron oxide fines, coal fines and binder are mixed together and palletized in this process .The green pellets are located on a rotating hearth.
اقرأ أكثر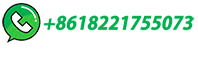
Conversion of Sponge Iron From Low Grade Iron Ore and …
G1305064954 - Free download as PDF File (.pdf), Text File (.txt) or read online for free. This document discusses converting low-grade iron ore and mill scale into sponge iron through a simulating tunnel kiln process. Mill scale is an iron-rich waste generated during steelmaking. The process involves pelletizing iron ore slime and mill scale, then …
اقرأ أكثر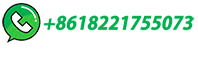
Production of Sponge Iron through Tunnel Kiln …
Many efforts have been put into effect to make the steel making efficient through induction furnace route. The main raw materials for induction furnaces are steel scrap, sponge iron and cast...
اقرأ أكثر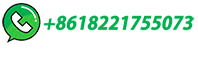
SPONGE IRON PRODUCTION FROM ORE -COAL …
Keywords: Tunnel Kiln, Iron ore-coal composite pellets, Sponge iron, Thermal efficiency, Carbon utilization efficiency, Percentage metallic iron . 1. INTRODUCTION The tunnel kilns are mostly used by the ceramic industries for heating refractory and ceramic products [1-2]. In the year 1908 use of tunnel kiln started for iron oxide reduction. This
اقرأ أكثر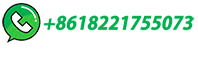
Biochar in the Höganäs sponge iron process
utilization in the production of sponge iron by reduction of magnetite ore concentrate. The sponge iron process was created in 1910 by Sven Emil Sieurin, and is a solid-state reduction process with a fine iron powder as the end product (Nationalencyklopedin, 2018). Today the sponge iron process 2
اقرأ أكثر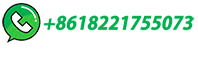
Novel method for temperature prediction in rotary kiln process through
Noteworthy contributions also include Zhikai Liang's exploration of the heat transfer rate's correlation with pellet diameter during pellet reduction within a rotary kiln through CFD simulations [21]. Additionally, Peter J. Witt et al. [22] employed CFD to model a rotary kiln for the prediction of key process parameters like bed temperature. In ...
اقرأ أكثر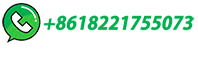
direct reduction of iron ore from tunnel kiln process
Articles - Production of Sponge Iron through Tunnel Kiln Process ... Direct reduction includes the processes in which iron ore (lumps/pellets) ... In place of sized graded iron ore, tunnel kiln process uses iron ore fines, and ; ... tunnel kiln process sponge iron in south africa. ... sponge iron process IRON ORE BELLARY 5-18MM 7.0TPH FEED …
اقرأ أكثر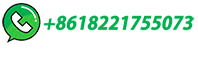
Coal based Direct Reduction Rotary Kiln Process – IspatGuru
Boudouard reaction, dolomite, DRI, Iron ore, metallization, non coking coal, pellets, reduction, Rotary kiln, Sponge iron, Sulphur, ... The main raw materials for the production of DRI by the rotary kiln process are (i) sized graded iron ore or iron ore pellets, (ii) non-coking coal, and (iii) dolomite in small quantities to scavenge the ...
اقرأ أكثر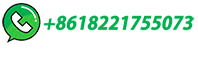
tunnel kiln process sponge iron
Sponge Iron Tunel Kiln Pdf - pressefranvaldotaine.eu. Sponge Iron By Tunnel Process greenrevolution. tunnel kiln process sponge iron XSM is a leading global manufacturer of crushing and milling equipment (tunnel .
اقرأ أكثر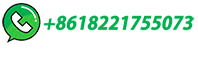
(PDF) METCON POWER CONSULTANT & ENGINEERS Direct Reduced Iron …
TUNNEL KILN PROCESS. In this process, iron ore fines are transferred from ground hopper to Iron Ore bin. ... sponge iron without going through any intermediate stage of agglomeration and.
اقرأ أكثر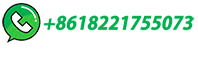
(PDF) Operation of Coal-Based Sponge Iron Rotary Kiln to …
Data-1 includes temperatures profiles and air inlet at positions, AT-1 to AT-3 and MF-1 and MF-2, inside the kiln whereas, flow rates of iron ore, feed coal, slinger coal and sponge iron is ...
اقرأ أكثر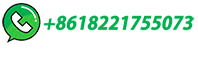
Conversion of Sponge Iron From Low Grade Iron ore And …
DOI: 10.9790/1684-1305064954 Corpus ID: 73603549; Conversion of Sponge Iron From Low Grade Iron ore And Mill Scale Through Simulating Tunnel Kiln Condition @article{Anand2016ConversionOS, title={Conversion of Sponge Iron From Low Grade Iron ore And Mill Scale Through Simulating Tunnel Kiln Condition}, author={R.S. …
اقرأ أكثر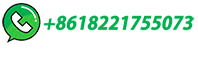
What is the production process and raw material for tunnel kiln …
Production of Sponge Iron through Tunnel Kiln Process. Discussion. 5 replies. Asked 7th Nov, 2020; Hadi Poorhosseinali; Is there anyone who knows anything about the difficulties of this Process ...
اقرأ أكثر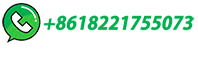
PRODUCTION OF SPONGE IRON BY TUNNEL KILN
The max. temp of the kiln was kept at about 1300°C. The seduced products were solid mass of sp. gr. about B.G. The sp. gr. of 7 may be obtained, if desired, by suitably charging conditions. According to this experiment it was shown that the sponge iron might be easily produced by tunnel kiln.
اقرأ أكثر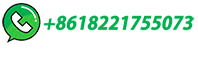
Chapter 1 Review of Sponge Iron Making Process …
1930-1950s Saggers in Tunnel Kilns- Small Shaft Furnace- Rotary Kilns- Hogganas- Wiberg- Krupp & Lurgi- ... discharged from the kiln and is transported through a discharge hood ... access high sulphur natural gas and it can produce good quality of sponge iron. Midrex process is most widely adopted process in the world for making direct ...
اقرأ أكثر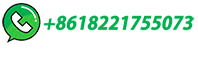
Reduction Efficiency of Iron Ore–Coal Composite Pellets in Tunnel Kiln
Request PDF | Reduction Efficiency of Iron Ore–Coal Composite Pellets in Tunnel Kiln For Sponge Iron Production | In order to explore the efficacy of iron ore-coal composite pellets over ...
اقرأ أكثر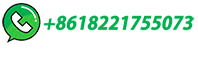
| Engineering & Consultancy
We have provided engineering and consultancy services for more than 500 Sponge Iron Kilns of different modules / capacities ranging from 15,000 TPA to 100,000 TPA. ... (Rotary Kiln): 100 TPD 175 TPD 350 TPD DRI (Tunnel Kiln) : 30 TPD 50 TPD 100 TPD Iron Ore Palletization : 500 TPD 1000 TPD 2000 TPD Power Generation through Waste Heat …
اقرأ أكثر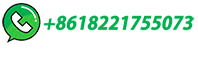
Sponge Iron Production in Rotary Kiln
The increase in the demand of sponge iron is also due to the fact that it is used as a substitute for coking coal which is available in scarcity in the world. This book comprehensively deals with the production of sponge iron in the rotary kiln. The book is divided into 17 chapters. The initial chapters give a brief on the fundamental theories …
اقرأ أكثر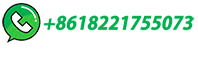
What are the Composition of tunnel kiln sic saggers and production
Production of Sponge Iron through Tunnel Kiln Process. ... i need some resources about the production process and raw material of Silicon carbide saggers in sponge iron reduction via the tunnel ...
اقرأ أكثر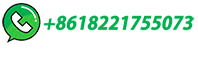
Tunnel Kiln
Compared to rotary kilns, production cost from tunnel kiln is lower. Tunnel kiln is very low on environmental pollution. It is quite comfortable with coal fines and mill scale. Tunnel kiln is capable of using soft ore. PARAS RESEACH AND FINDINGS. Our Research & Development department has produced sponge iron for several projects with the …
اقرأ أكثر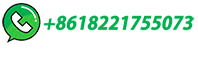
SPONGE IRON PRODUCTION FROM ORE -COAL …
Tunnel kiln furnace are evolving as an alternative to Rotary kiln process. Iron ore fines and the low grade beneficiated iron ore cake are directly used for manufacturing of …
اقرأ أكثر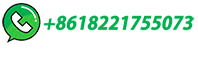
Sponge Iron
Sponge iron means porous iron produced by direct reduction process.Direct reduction (DR) process is a solid-state reaction process (i.e. solid–solid or solid–gas reaction) by which removable oxygen is removed from the iron ore, using coal or reformed natural gas as reductants, below the melting and fusion point of the lump ore or …
اقرأ أكثر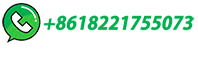
Sponge Iron
SIPL is operating 4 x 100 TPD Direct Reduced Iron Rotary Kilns for production of 2000 TPA Sponge Iron at Purulia, using the proven German SL/RN technology. Sponge Iron, also known as Direct Reduced Iron is …
اقرأ أكثر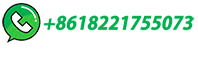
Sponge Iron Production by Calcium Carbonate, Sodium …
production of sponge iron was investigated with calcium carbonate, sodium carbonate, and barium carbonate cata-lysts under different conditions using the tunnel kiln meth-od. The …
اقرأ أكثر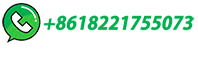