Fine grinding: How mill type affects particle shape …
In this case, the ball mill, which produces more elongated particles, may be preferred over the stirred mill. Differences in product shapes are attributed to the different grinding methods used in ...
اقرأ أكثر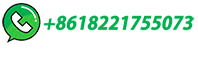
How it Works: Crushers, Grinding Mills and …
Crushers, grinding mills and pulverizers are types of grinding equipment that transform or reduce a coarse material such as stone, coal, or slag into a smaller, finer material. ... Pin mills utilize a …
اقرأ أكثر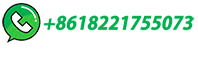
Ball Mills
Once the application requirements are clear, a suitable mill can be selected. To facilitate this process, Retsch displays the strength and efficiency of each ball mill model in a spider-net diagram, see Figure 3. A planetary ball mill, for example, offers a big jar volume compared to a mixer mill and shows a high value on this diagonal.
اقرأ أكثر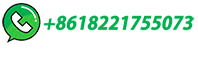
Effect of Corn Grinding Methods and Particle Size on the …
This study investigates the effect of grinding methods, including roller mill, hammer mill, and two-stage grinding, on the particle size distribution of corn and the effect of corn particle size on the nutrient digestibility of native chickens in Southwest China. The roller mill, hammer mill, and a combination of the hammer mill and roller …
اقرأ أكثر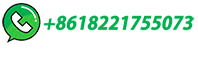
The effects of processing parameters on the shape of …
The study of particle size distribution (PSD) of materials is a crucial aspect of mineral processing. It not only determines the appropriate beneficiation process and …
اقرأ أكثر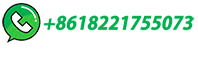
(49a) Dry Fine Grinding: Aspects of Particle Stabilization in …
In a first step, the stressing behavior inside a dry operated stirred media mill was investigated in dependence of the grinding aid as well as the most important …
اقرأ أكثر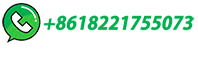
Experimental investigation of the impact breakage …
The results show that the particles are mainly broken by the impact behavior of grinding media, and only 5 % of the particles are broken by the grinding behavior [7]. Additionally, the particle breakage in the ball mill can be divided into single-particle impact breakage and multilayer-particle impact breakage.
اقرأ أكثر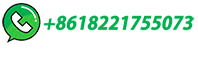
Energy-Efficient Advanced Ultrafine Grinding of Particles …
Abstract. The present literature review explores the energy-efficient ultrafine grinding of particles using stirred mills. The review provides an overview of the …
اقرأ أكثر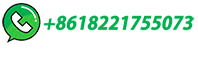
Principles of Sample Preparation by Grinding or …
Grinding forces. Particle reduction of solids occurs in multiple stages starting with the accumulation of defects or stresses in a concentrated location increasing the strain on a solid or particle. The stress forms microcracks and in crystal lattices, it will disrupt the crystal lattice in several cells or locations. ... These mills can ...
اقرأ أكثر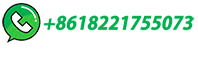
How the Nano Milling Process Works | Blog
The process of nano milling, or nano grinding, is the reduction of particles down to a very fine consistency through the use of wet grinding media mills. Reducing particles to sub-micron size presents unique challenges because the smaller the media you use, the smaller the mill screen needs to be, and the more susceptible that screen is to ...
اقرأ أكثر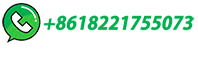
Top 5 product-specific milling technologies used in industrial
How jet mills work. The jet mill design incorporates a grinding zone at the bottom of the mill. The classification zone is located in the top section of the mill. Feed material is introduced to the mill through a top gravity feed inlet. These mills work by accelerating gas through a nozzle directed to a central focal point.
اقرأ أكثر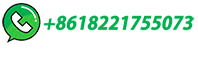
Exploring Ball Mill Diagram: A Comprehensive Guide
Crushing is the primary phase in which the large particles are reduced into smaller ones that can be introduced into the grinding mills, including ball mills. Grinding, which is the second and final stage, reduces the particle size into even finer particles with the help of impact and attrition forces.
اقرأ أكثر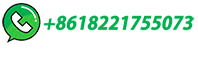
Mill, material, and process parameters
The grinding limit or minimum particle size can be calculated from inter-crystalline material parameters as described by Knieke et al. [55].The compression strength σ CS is a material parameter, and was used based on the assumption that compression is the dominant type of stress in a stirred media mill. The compression strength and …
اقرأ أكثر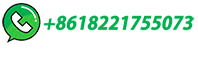
Bead Mills
A bead mill is a type of equipment used for ultrafine grinding and dispersing of particles. It operates on the principle of impact and attrition: grinding media (beads) made of glass, ceramic, or steel are agitated inside a vessel or a chamber by a rotating shaft with impellers, causing the particles to break into smaller sizes due to collision and shear forces.
اقرأ أكثر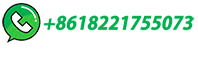
Wet and dry grinding of coal in a laboratory-scale ball mill: Particle …
After each dry-grinding test with a selected grinding time, the mill was held sufficiently long to allow the fines to settle. Then, the balls were removed and the ground particles were discharged into a container. ... the main source of fine particles for the dry grinding is secondary breakage. The ash content of the wet-ground −3.0 + 1.0 mm ...
اقرأ أكثر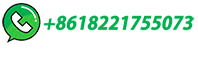
Ball Mill
Closed-circuit grinding in mills providing low residence time for the particles is almost always used in the last stages to overcome this. Several factors influence the efficiency of ball mill grinding. The pulp density of the feed should be as high as possible, consistent with ease of flow through the mill.
اقرأ أكثر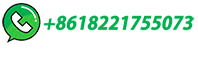
Effect of grinding nozzles pressure on particle and fluid flow …
Particles are also subjected to high velocity collisions as they are ejected from the bed by the gas jets and also upon collision with the bed surface further downstream [3]. Therefore, inside the mill particle size reduction is induced, where high shear straining and collisions prevail near the bed surface, rather than within the bed [4].
اقرأ أكثر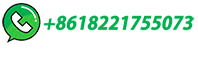
Numerical Investigation of Vertical Roller Mill Operation …
A vertical roller mill is a grinding equipment for many industries such as minerals, cement, and ceramics. It is also used to grind slag and nonmetallic ores. The VRM decreases the number of equipment in the grinding circuit by combining the drying, crushing, grinding, and particle segregation in one unit . The energy-efficient operation …
اقرأ أكثر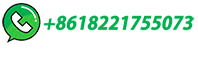
SWECO Vibratory Grinding and Particle Size Reduction …
High Amplitude Wet or Dry Mills Vibratory Grinding Mills Size Reduction Equipment Specifically designed for wet or dry grinding, the high amplitude Vibro-Energy Grinding Mills range from 1 ft³ (36 liters) to 75 ft³ (1,934 liters) of volume.. Wet or Dry Grinding Mill Models: DM1, DM4, DM10, DM20, DM28, DM70. Low Amplitude Wet Mills Vibratory …
اقرأ أكثر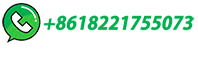
Custom Chemical Grinding & Milling Services | Seatex
Grinding and milling services by Seatex deliver standardized particle sizes for your products, every time. ... In a one-step process with quick turnaround time and hefty batch sizes, the mill uses impact grinding with an integrated dynamic classifier to convert coarse materials to fine, especially products in the soft to medium-hard range. ...
اقرأ أكثر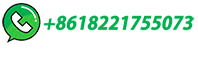
Fine Grinders, Hammer Mills, and More for Particle Size …
Designed to grind dry, free-flowing material down to 200 mesh with very tight particle distribution, our fine grinders are also ideal for heat-sensitive materials such as powder …
اقرأ أكثر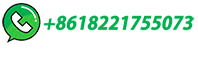
Fine grinding: How mill type affects particle shape …
The objective of this work is to assess the influence of fine grinding in ball mills and stirred mills on valuable mineral liberation and particle shape characteristics …
اقرأ أكثر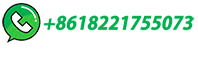
Effect of particle shape in grinding mills using a GPU …
The reduction in particle size of raw materials using grinding mills is an energy and cost intensive task. Optimization of grinding processes is not trivial as obtaining experimental information is extremely difficult due to the harsh environment. ... In SAG mills, in addition to self-breakage of the ore particles, the grinding balls cause ...
اقرأ أكثر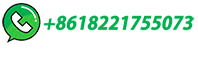
Micronization of a Soft Material: Air-Jet and Micro-Ball Milling
In a ball mill, grinding energy is transferred to materials through media such as balls, rods, pebbles, by moving the mill body . For both types of mills the mechanisms by which particle size is reduced follow the same principles. ... Studies optimizing particle size reduction of sucrose using an air-jet mill reported median …
اقرأ أكثر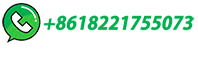
Grinding in Ball Mills: Modeling and Process Control
Besides particle size reduction, ball mills are also widely used for mixing, ... Ball mills can grind a wide range of materials, including metals, ceramics, and polymers, and can operate on a ...
اقرأ أكثر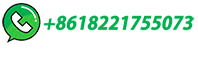
Scale-Up Investigation of a Pilot and Industrial Scale Semi …
A particle scale model based on a full two-way coupling of the Discrete Element Method (DEM) and Smoothed Particle Hydrodynamics (SPHs) methods is applied to SAG mills. Motion and collisions of resolved coarser particles within an SAG mill are performed by the DEM component. Fine particles in the feed combine with the water to …
اقرأ أكثر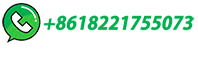
Fine grinding: How mill type affects particle shape characteristics and
There is also currently increased interest in the effects of particle morphology on flotation performance, and questions being raised as to whether the shape characteristics of particles can be selectively modified using particular grinding conditions or different mill types (Guven and Çelik, 2015).
اقرأ أكثر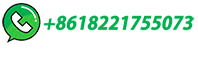
Energy-Efficient Advanced Ultrafine Grinding of Particles …
The present literature review explores the energy-efficient ultrafine grinding of particles using stirred mills. The review provides an overview of the different techniques for size reduction and the impact of energy requirements on the choice of stirred mills. It also discusses the factors, including the design, operating parameters, and feed material …
اقرأ أكثر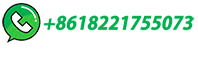
Selected Advances in Modelling of Size Reduction in Ball Mills
Mathematical models of grinding kinetics serve three purposes: (i) identification of the mill-material grinding system in terms of some parameters of physical significance, (ii) development of quantitative correlations for variation of the model parameters with the mill design and operating variables for process simulation, …
اقرأ أكثر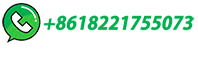
What Is a Ball Mill and How Does It Work?
On the other hand, rod mills are better suited for coarser grinding and selective grinding of larger particle sizes. A rod mill is typically more efficient within a drum diameter range of 5 mm to 0.4 mm (4 mesh to 35 mesh). This makes it more suitable for applications where larger particles need to be ground, considering the mill diameter.
اقرأ أكثر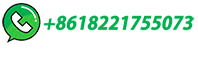