Solved Question Completion Status: Modern iron and steel
Question Completion Status: Modern iron and steel begin with the three primary raw materials: a coke, sodium hydroxide, limestone Obsand, iron ore, feldspar O silica, alumina, slag od iron ore coke, and limestone QUESTION 2 Pig iron, the source of almost all of the ferrous metals, is produced in the basic oxygen turnace True False …
اقرأ أكثر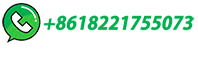
A Study on High-Grade Iron ore Beneficiation to Reduce Alumina …
Iron ore pellets are largely characterized by inherent physical and chemical properties of the ore. Alumina and silica play important roles in determining the productivity of a Blast Furnace. On average, one percent increase in iron content improves productivity by 2% and reduces coke consumption by 1%. Therefore higher iron ore feed content to …
اقرأ أكثر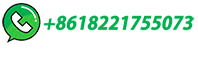
Bauxite Beneficiation: An Approach to Value Addition in …
A metallic iron concentrate with high-iron grade, and a non-magnetic product with high alumina content, can be obtained from high-iron gibbsitic bauxite containing 25–30% total iron. The metallic iron concentrate can be used as steelmaking material, and alumina can be extracted from the non-magnetic product.
اقرأ أكثر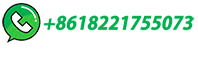
Ironmaking 101 – From Ore to Iron with Blast Furnaces
Ironmaking Blast Furnace. Iron is made by reacting iron ore (iron oxide and impurities), coke (a reductant) and limestone (CaCO 3) in a blast furnace.. Iron ores with lower iron content such as taconite are first processed to concentrate the iron level and drive off volatile impurities.
اقرأ أكثر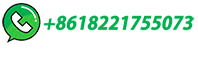
Removal of Silicon, Aluminum and Phosphorus Impurities …
In this paper, the removal processes for silicon (Si), aluminum (Al) and phosphorus (P) impurities from low-grade iron ore, in which hematite (Fe2O3), goethite (FeO(OH)), and quartz (SiO2) are the ...
اقرأ أكثر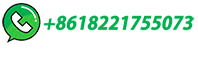
Simec Mining 950tph Iron Ore Beneficiation Wash Plant
Alumina levels range from 5.9% to 8.8% and are reduced to 2.8% after processing. The iron ore wash plant also removes clays from the feed material and the combined effect means the Fe content increases from between 43.4% and 52.7% in the feed to above 60% iron ore product, with a yield of up to 50%.
اقرأ أكثر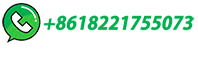
Iron Ore
1.1.3.2.1.2 Iron-Bearing Materials. Ore fines and iron concentrates make the main part of the sinter mix. The grain size of ore fines and concentrates is typically 0–8 and 0–3 mm, respectively.Grains smaller than 0.1 mm are not desired because they reduce the gas permeability of the bed and thus decrease the sintering efficiency.Recycled …
اقرأ أكثر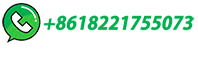
Beneficiation, sintering, and processing of raw materials …
Another aspect of considerable importance to iron-ore beneficiation in India is the possibility of lowering of alumina content of the ore. Control of the alumina con-tent of the blast-furnace charge is necessary to obtain a fluid slag of proper composition for production of quality pig iron. Depending on the nature of the ore, alumina may be
اقرأ أكثر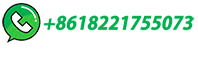
Environmental Exam 3 Flashcards
5) Smelting of iron ore involves _____. A) washing the ore with acid to extract iron B) dissolving the ore in hot water to separate iron and aluminum C) crushing and heating the ore at its melting point D) oxidizing iron to ferric oxide and then adding silicon and boron E) heating beyond iron's melting point and combining the material with carbon
اقرأ أكثر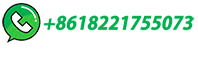
Extraction and Utilization of Valuable Elements from Bauxite …
Alumina industry is an important basic raw material industry of the national economy, which is a resource-intensive industry with great consumption of energy, water, and ore resources (Zhao et al. 2005).At the same time, the hazard of bauxite residue is the biggest environmental problem facing alumina production at present (Ke et al. …
اقرأ أكثر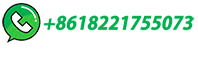
Froth Flotation of Iron Ores
With the depleting reserves of high-grade iron ore in the world, froth flotation has become increasingly important to process intermediate- and low-grade iron ore in an attempt to meet the rapidly growing demand on the international market. In over half a century's practice in the iron ore industry, froth flotation has been established as an …
اقرأ أكثر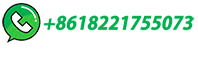
New mobile iron ore washing plant for Bhushan Power …
A new mobile iron ore washing plant for Bhushan Power & Steel is delivering a substantial increase in Fe through the effective removal of alumina and silica from the feed material. Iron Ore Washing. Pg. 2 is subsequently used as input to …
اقرأ أكثر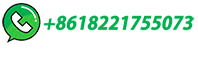
How is Steel Made? An introduction to steelmaking.
During this reduction process, impurities in the iron ore combine with limestone to form slag, which floats on top of the molten iron and can be removed. This produces crude iron, which is then further refined in the steelmaking process to obtain the desired steel composition by adjusting its carbon content and incorporating alloying …
اقرأ أكثر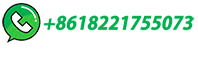
Beneficiation Strategies for Removal of Silica and …
A commercial flowsheet is expected to involve the implementation of several separation technologies. This will allow an informed selection and testing of possible process …
اقرأ أكثر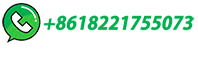
Improving recovery of iron using column flotation of iron ore …
In Brazil, the generation of iron ore slimes is estimated to be 20–40% by weight of the total iron ore mined. Taking into account the present magnitude of the iron ore slimes generated annually and accumulated over the years, it can be considered a national resource in the iron and steel industries if properly beneficiated using …
اقرأ أكثر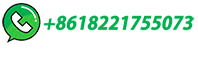
Flux for Metallurgy
Selection of flux is related to the metals to be extracted and the composition of ore. Steel-making usually uses CaO-Al 2 O 3-SiO 2 slag, while the ashes in iron ore and coke are mostly acidic oxides (SiO 2), so alkaline flux (limestone or dolomite) is usually used.Smelting of nonferrous metals usually uses FeO-SiO 2, FeO-CaO-SiO 2, FeO-Al 2 …
اقرأ أكثر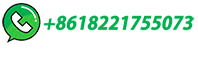
Development of process for beneficiation of low-grade …
Low-grade iron ore received from the West Singhbhum area of Jharkhand state in India was used to develop a beneficiation flow sheet to remove alumina (Al 2 O 3 ) and silica (SiO 2) from the ore to get iron (Fe)-rich product for steel plants. Mineral characterization showed that the main mineral constituents present in the head sample are goethite,
اقرأ أكثر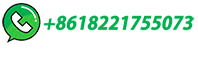
Iron (Fe) Ore | Minerals, Occurrence » Geology …
Description and properties of common iron ore minerals. Iron ore minerals are rocks or minerals that contain iron in concentrations high enough to be economically extracted. Common iron ore minerals …
اقرأ أكثر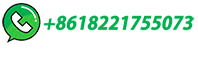
5 Ways to Remove Iron From Well Water (Easy Methods)
A good RO system can cost you between $200 – $500, and can remove upwards of 90% of the iron in the water, which makes it significantly cheaper than other iron treatment methods. The system's size and cost will depend on the amount of iron you have in your well system and how effective you need the removal rate to be.
اقرأ أكثر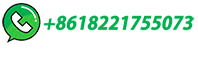
Bauxite
Bauxite (Fig. 1.33) is formed by surface weathering of clay rocks around the tropical region and composer of aluminum oxide (Al(OH) 3).It contains 15%–25% aluminum and only ore used for commercial extraction for aluminum. The bauxite occurs as near-surface layers and usually mixed with clay minerals, iron oxide, and titanium dioxide.
اقرأ أكثر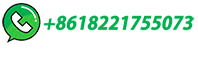
Extraction of Metals | CIE IGCSE Chemistry Topic Questions …
Iron is extracted from its ore, hematite, in a blast furnace. Substances added to the furnace are: Iron ore, hematite, containing impurities such as silica, SiO 2; Air; Coke, C; Limestone, CaCO 3; Substances formed in the blast furnace are: Molten iron; Molten slag; Waste gases such as carbon dioxide; State the two functions of the coke used in ...
اقرأ أكثر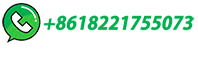
REMOVING IMPURITIES FROM IRON ORES: METHODS AND …
by heating above 56 ᴼ C in water or addition of cau stic soda. Solubilizatio n in caustic soda depends on starch/caustic. ratio (normally 4:1 or 3:1) and starch particle …
اقرأ أكثر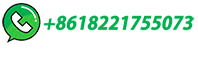
Physiochemical separation of iron ore
Aluminum removal. Since the beginning of iron ore flotation research in the 1930s, silica removal has been studied extensively while aluminum removal has received limited attention. The reverse cationic flotation route widely used in the iron ore industry is less selective for alumina–hematite separation than for quartz–hematite separation.
اقرأ أكثر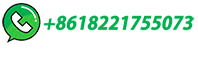
A new disposal method for white mud: Replacing limestone …
A new process for resource utilization and disposal of white mud is proposed. •. Moderate white mud will not deteriorate the sinter quality and productivity. •. …
اقرأ أكثر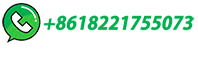
THE ALUMINIUM STORY BAUXITE TO ALUMINA: THE …
Mud Washing 20 16. Residue Disposal and Re-use 20 17. Impurity Balances and Removal including Liquor Purification 22 ... alumina, up to 20% of iron oxides and 2-5% of silica in reactive clays ... store it for subsequent rehabilitation of the minesite once all ore is removed. The caprock is fractured or blasted, and the bauxite (usually quite ...
اقرأ أكثر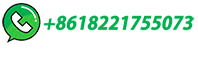
Ore Washing and Machine Selection
Log Washersare used in a variety of material processing applications and are best known for their ability to remove tough, plastic clays from natural and crushed gravel, crushed stone, and ore feeds. One limitation of Log Washers is that they must have a controlled top size. In general, most …
اقرأ أكثر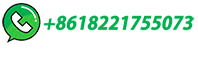
Processing options for removal of silica and alumina from …
Global demand for iron and steel has increased substantially over the past 20 years and there has been a greater focus on developing suitable processing options to treat low …
اقرأ أكثر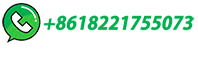
Recent strategies for the removal of iron from water: A …
The mineral form of aluminum-silicon oxides with iron substituting for silicon or aluminum is called pyroxene. ... NOM and co-existing cation on the iron removal efficiency of limestone was examined during the study. ... Manganese ore constructed wetlands have been used in the reclamation of steel wastewater for the removal of iron. …
اقرأ أكثر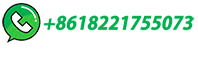
Effect of Adding Limestone on the Metallurgical Properties of Iron Ore
On the other hand Mikho Iljana et al. [36] studied many properties for addition of limestone (CaCO 3 ) in iron ore pellets reduction and he concluded that with an increase in the percentage of ...
اقرأ أكثر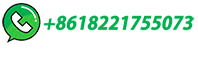
4 Q&A You need to Know about Mineral Washing Process
2.3.2 Alkaline roasting and water washing of iron ore: P removal The iron ore sample was roasted in a muffle furnace under the different NaOH concentrations (10-50 g/kg …
اقرأ أكثر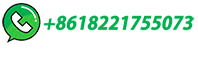