Mining and Processing Iron Ore
Iron Ore. COMPOSITION • USES • DRYING • SOLUTIONS. 1015 W. Highway 24, Moberly, MO, USA • +1 (660) 263-7474 • • sales@vulcandryingsystems ... Drying is an important step in the iron ore process, reducing shipping and storage costs, while making the material easier to handle. As an …
اقرأ أكثر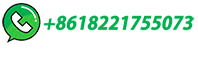
Full article: Iron ore processing
This special issue of Mineral Processing and Extractive Metallurgy presents a selection of the best metallurgy papers delivered at the very successful international 'Iron Ore 2015' conference held at the Perth Convention and Exhibition Centre, Australia, on 10–12 July 2015. This was the seventh in the series of biennial conferences featuring …
اقرأ أكثر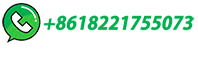
Iron Ore Processing, General
The iron ore processing industry produces usable concentrations of iron-bearing material by removing nonferrous rock (gangue) from low-grade ore. In the United States, predominant iron ore is taconite which is a hard, banded, low-grade ore. Ninety-nine percent of the crude iron ore produced in the United States is taconite.
اقرأ أكثر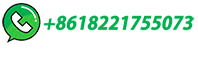
material transfer systems conveyor
material transfer trolley for conveyor system 80t. Chute Conveyor System in Material Handling Shmula Mar 05, 2011 · Today, we''ll discuss one of the simplest types of conveyors: The Chute Conveyor.
اقرأ أكثر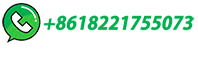
Iron Ore Pelletization
The Process Development Behind Iron Ore Pelletizing . As there can be significant variation in process requirements and sources of iron ore fines, testing is often an essential part of the development of a successful iron ore pelletizing operation. Different sources of iron ore will respond differently to agglomeration, and process requirements ...
اقرأ أكثر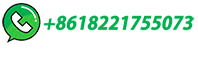
Iron ore mining and dressing
This means that the mined iron ores need to be specially processed in advance before the blast furnace process. Regions in which iron ore has formed over millions of years (e.g. through volcanism) and can be mined economically are also referred to as iron ore deposits. Especially many ore deposits can be found in countries such as …
اقرأ أكثر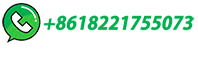
Introduction to Iron ore Pellets and Pelletizing processes
The various advantages of iron ore pellets are given below. Iron ore pellet is a kind of agglomerated fines which has better tumbling index when compared with the iron ore and it can be used as a substitute for the iron ore lumps both in the BF and for DRI production. Pellets have good reducibility since they have high porosity (25 % to 30 …
اقرأ أكثر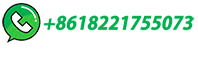
Applications of Iron Ore Pellets
What Is Iron Ore Pelletization Process. The process of pelletization begins with the use of finely powdered grains of iron ore. These grains are then converted into balls. This iron ore concentrate is next heated and dried over high temperatures. The next step involves grinding this dried residue, with the addition of Bentonite which is a ...
اقرأ أكثر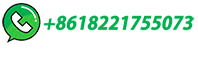
Iron Ore: Mineralogy, Processing and Environmental …
Iron Ore: Mineralogy, Processing and Environmental Sustainability, Second Edition covers all aspects surrounding the second most important commodity behind oil. As an essential input for the production of crude steel, iron ore feeds the world's largest trillion-dollar-a-year metal market and is the backbone of the global infrastructure. The book …
اقرأ أكثر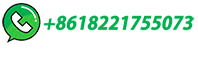
Iron Ore Processing: From Extraction to Manufacturing
Iron ore processing is a complex and vital process that transforms raw iron ore into usable steel. From exploration and extraction to grinding, beneficiation, and …
اقرأ أكثر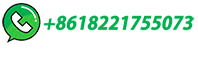
From Ore to Iron with Smelting and Direct Iron …
Ironmaking is a critical step in producing high performance steel because high-quality raw materials reduce the time and energy to …
اقرأ أكثر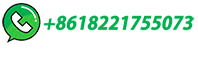
Rio Tinto validates its BioIron process to produce low-carbon …
With the process proven, Rio Tinto now plans to develop a larger-scale pilot plant to help decarbonise the steel value chain. BioIron involves the use of raw biomass, …
اقرأ أكثر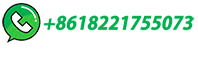
Direct Reduction Ironmaking
It is the non-coke ironmaking process in which a gaseous, liquid, or solid reductant is used to reduce the iron ore into metallic iron in a temperature less than the ore softening temperature. The product is direct reduction iron which is an ideal raw material for producing high-quality steel and clean steel.
اقرأ أكثر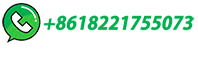
Sustainable steel through hydrogen plasma reduction of iron ore …
Iron- and steelmaking is the largest single industrial CO2 emitter, accounting for 6.5% of all CO2 emissions on the planet. This fact challenges the current technologies to achieve carbon-lean steel production and to align with the requirement of a drastic reduction of 80% in all CO2 emissions by around 2050. Thus, …
اقرأ أكثر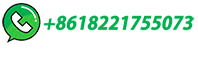
Direct reduced iron process
Sponge iron is a highly ferrous ore from the direct reduced iron process! In order to prevent excessive re-oxidation of the sponge iron in the ambient air, it must be cooled down in the lower region of the shaft furnace. Carburisation as in the blast furnace process does not occur in the DRI-process, as coke is not used as a reducing agent.
اقرأ أكثر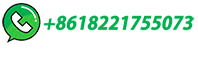
Iron Ore PRICE Today | Iron Ore Spot Price Chart | Live Price of Iron
Iron Ore Price: Get all information on the Price of Iron Ore including News, Charts and Realtime Quotes.
اقرأ أكثر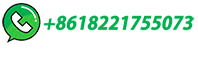
The Sintering Process of Iron Ore Fines – IspatGuru
The Sintering Process of Iron Ore Fines. satyendra; March 9, 2013; 8 Comments ; flux sinter, Iron ore fines, self fluxing sinter, sinter, sinter machines, Stright line machine. circular machine, super fluxed sinter,; The Sintering Process of Iron Ore Fines. Sintering plants are normally associated with the production of hot metal in blast …
اقرأ أكثر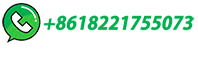
New process for treating boron-bearing iron ore by flash
Boron is an important industrial raw material often sourced from minerals containing different compounds that cocrystallize, which makes it difficult to separate the mineral phases through conventional beneficiation. This study proposed a new treatment called flash reduction–melting separation (FRMS) for boron-bearing iron concentrates. …
اقرأ أكثر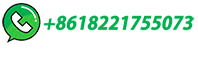
Iron Mining Process
Iron Mining Process. From blasting to crushing to separation – more than 85% of the iron mined in the United States is mined in northeastern Minnesota to make our nation's steel. Blasting Taconite is a very hard rock. Using explosives, the taconite is blasted into small pieces. ... The iron ore is separated from the taconite using magnetism ...
اقرأ أكثر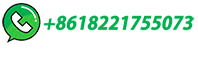
Effect of Ammonia Injection on the Iron Ore Sintering Process…
The experiment involving ammonia injection was conducted to minimize solid fuel consumption and carbon emissions during the sintering process of iron ore. The sintering bed temperature, sintered ore quality, combustion efficiency, and pollutant emission under different ammonia injection concentrations and coke ratios were …
اقرأ أكثر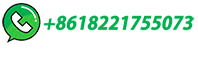
What Are Iron Ore Pellets and How to Make Them?
What are iron ore pellets? Iron ore pellets are spheres of typically 8-16 mm to be used as feedstock for blast furnaces. They contain 64-72% iron and additional materials, which can adjust the chemical …
اقرأ أكثر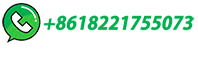
Iron, boron, and sulfur isotope constraints on the ore …
In this study, a combined systematic Fe, B, and S isotope investigation was first applied to investigate the sulfide precipitation processes and the relative proportion …
اقرأ أكثر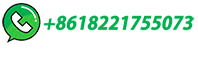
Iron Ore in India, Types, Uses, Distribution, World Map
Natural ore, also known as "direct shipping ore," is ore that contains a high percentage of hematite or magnetite (more than 60% iron) and can be fed directly into blast furnaces to produce iron. Iron ore is a raw material used to produce pig iron, which is one of the primary raw materials used to produce steel—steel accounts for 98 per ...
اقرأ أكثر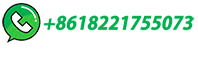
H2 Green Steel
H2 Green Steel will be the first carbon-neutral steel plant in the world, built on technology from SMS group.
اقرأ أكثر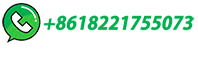
Zanaga Iron Ore Company Limited 2022 Annual Report …
Zanaga Iron Ore ompany Limited ("ZIO" or the "ompany") (AIM ticker: ZIO) is the owner of of the Zanaga Iron Ore Project based in the Republic of Congo (Congo Brazzaville) through its subsidiary Jumelles Limited. The Zanaga Iron Ore Project is one of the largest iron ore deposits in Africa and has the potential to
اقرأ أكثر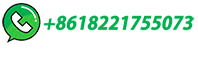
A REVIEW OF IRONMAKING BY DIRECT REDUCTION …
The proposed iron ore reduction process therefore would be a potential to reduce iron directly using biomass with high efficiency and real environmental benefits. View. Show abstract.
اقرأ أكثر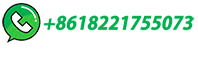
Ironmaking 101 – From Ore to Iron with Blast Furnaces
Iron is made by reacting iron ore (iron oxide and impurities), coke (a reductant) and limestone (CaCO 3) in a blast furnace. Iron ores with lower iron content …
اقرأ أكثر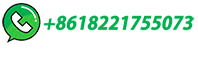
Iron Ore Processing, General
Making iron and steel from iron ore requires a long process of mining, crushing, separating, concentrating, mixing, agglomeration (sintering and pelletizing), and shipping …
اقرأ أكثر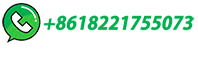
Effect of gangue composition on assimilation characteristic of iron ore
For iron ores, the influence of gangue composition on LAT is basically the same as that of pure reagents, but the linear correlation coefficient is not obvious. It is better to study the effect of synergy of SiO 2, Al 2 O 3 and MgO content in iron ore on LAT than that of single factor.
اقرأ أكثر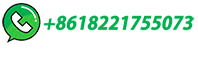
Multisource Information Fusion for Autoformer: Soft
As a key thermal-state indicator of the iron ore sintering process, the content of ferrous oxide (FeO) in the finished sinter is directly related to product quality. Based on the massive data of sintering process, the data-driven soft sensor model provides a good choice for real-time FeO content detection. However, the complex characteristics of the data, …
اقرأ أكثر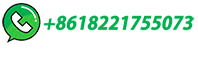