BALL MILLS Ball mill optimisation
This paper will focus on the ball mill grinding process, its tools and optimisation possibilities (see Figure 1). The ball mill comminution process has a high electrical …
اقرأ أكثر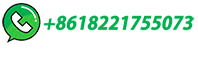
Ball Mills a suitable ball mill for every application
The variety of grinding modes, usable volumes and available grinding tool materials make ball mills the perfect match for a vast range of applications. Cooling, heating & …
اقرأ أكثر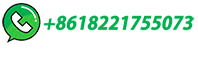
Energy-Efficient Advanced Ultrafine Grinding of Particles …
The present literature review explores the energy-efficient ultrafine grinding of particles using stirred mills. The review provides an overview of the different techniques for size reduction and the impact of energy requirements on the choice of stirred mills. It also discusses the factors, including the design, operating parameters, and feed material …
اقرأ أكثر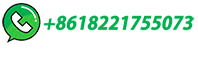
10 Ways to Improve the Grinding Efficiency of Your Ball Mill
Are you faced with the problem like low grinding efficiency, low processing capacity, high energy consumption, unstable product fineness of the ball mill? ... However, the power consumption is also large, and it is easy to change the motion state of the steel ball if the filling rate is too high, then the impact effect on large particle ...
اقرأ أكثر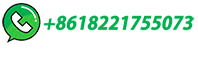
Gold Large Capacity Ball Mill,Gold Wet Ball Mill,Ball Mill …
Gold Large Capacity Ball Mill,Gold Wet Ball Mill,Ball Mill Machine Stone Grinding, Find Complete Details about Gold Large Capacity Ball Mill,Gold Wet Ball Mill,Ball ...
اقرأ أكثر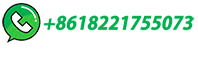
Ceramic vs. Steel Grinding Balls: A Comprehensive …
Introduction. In industrial processes, grinding balls are indispensable components in milling and grinding operations, where they play a pivotal role in reducing particle sizes and refining material textures. These balls, varying in material composition, size, and density, are at the heart of numerous industries, from mining to …
اقرأ أكثر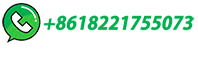
ball mill calculations, grinding media filling degree, ball size, …
online live calculators for grinding calculations, Ball mill, tube mill, critical speed, Degree of filling balls, Arm of gravity, mill net and gross power
اقرأ أكثر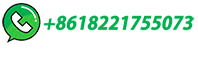
High-efficiency and energy-conservation grinding technology using …
A pilot-scale grinding technology of ceramic medium stirred mill was proposed in this study. Based on the specific productivity and grinding efficiency, the appropriate grinding parameters were ascertained as follows: material ball ratio of 0.7, ceramic ball medium size ratio (10 mm: 15 mm: 20 mm = 3:2:5), stirring speed of 110 …
اقرأ أكثر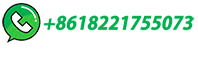
How Ball Mill Ore Feed Size Affects Tonnage & Capacity
The finer you crush, the higher your ball mill tonnage and capacity will be. The effect of ball mill feed size and how it affects circuit throughput can be hard to estimate. Here we described a method of designing a crushing plant using power drawn and power rate to define reduction ratios in each stage of crushing.
اقرأ أكثر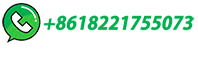
Grinding mill plants
Capacity 80 - 100 kg/h (Capacity is based on input and depends on the fineness of flour) ... Large grinding surface and no integral screen. Gives high capacity and low power consumption.. more than expected. The Miller´s Choice Milling Plant we purchased from Engsko is a very good and low cost investment and we are extremely happy with the ...
اقرأ أكثر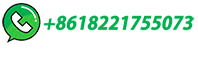
Fine grinding: How mill type affects particle shape characteristics …
The breakage mechanisms in stirred mills – regardless of the mill orientation – are typically described as abrasion and attrition (Gao and Forssberg, 1995, Sinnott et al., 2006, Wills and Napier-Munn, 2006, Ye et al., 2010), or more simply "shear" breakage (Radziszewski, 2013).The dominant breakage mechanism in ball mills is generally …
اقرأ أكثر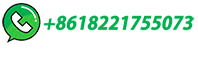
Mechanics of the grinding media in ball mills with …
This article analyzes the problems of perfecting grinding equipment for large-scale production – cement, ore, coal. An improved design of a ball mill, equipped with internal energy Exchange ...
اقرأ أكثر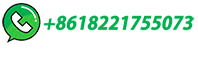
OPTIMIZATION OF CEMENT GRINDING OPERATION IN …
consumption and low production. The consumption of energy by the cement grinding operation amounts to one third of the total electrical energy used for the production of cement. The optimization of this process would yield substantial benefits in terms of energy savings and capacity increase. Optimization of the Cement Ball Mill Operation
اقرأ أكثر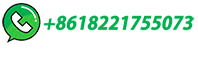
Grinding Media Wear Rate Calculation in Ball Mill
In the previous discussion the fact was established that the work done by a ball when it strikes at the end of its parabolic path is proportional to its weight and velocity; then, since the velocity may be considered as constant for all the balls in the mill, the work done by a ball is proportional to its weight. Since the amount of ore crushed varies as …
اقرأ أكثر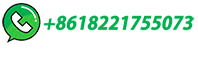
Comparing ball mills and VRMS for cement grinding
Usually, a compromise is found between the PSD curve and energy consumption, as the above actions reduce the grinding efficiency and therefore increase the mill's power consumption. Investment cost A VRM is a compact unit, making the footprint of the installation smaller and reducing the civil engineering costs when …
اقرأ أكثر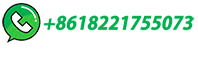
Factors Affect The Output and Quality of Ball Mills And How …
If the particle size is small, the production and quality of the mill will be high, and the power consumption will be low; if the particle size is large, the output and …
اقرأ أكثر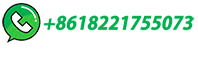
Energy-Efficient Technologies in Cement Grinding
In this chapter an introduction of widely applied energy-efficient grinding technologies in cement grinding and description of the operating principles of the related equipments and comparisons over each other in terms of grinding efficiency, specific energy consumption, production capacity and cement quality are given. A case study …
اقرأ أكثر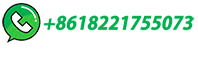
Fine Grinding as Enabling Technology – The IsaMill
These features distinguish stirred mills as fundamentally different from both ball mills and Tower Mills, as demonstrated by Tables 1 and 2. Table 1 : Typical Power Intensities of different Grinding Devices Table 1: Power Intensity of Different Grinding Devices Ball Mill is a 5.6m D x 6.4m L @ 2.6MW Tower Mill is a 2.5m D x 2.5m L @ 520KW
اقرأ أكثر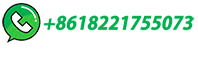
Low Maize Milling Machine Price
The large scale maize milling machine price ranges from US $1,250,000 to US $1,850,000 per set depending on the capacity of tons per day produced. Medium size maize milling machine It processes maize by peeling, grinding and flour packaging.
اقرأ أكثر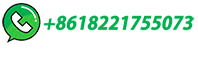
Calculate Ball Mill Grinding Capacity
The sizing of ball mills and ball milling circuits from laboratory grinding tests is largely a question of applying empirical equations or factors based on accumulated experience. Different manufacturers use different methods, and it is difficult to check the validity of the sizing estimates when estimates from different sources are widely …
اقرأ أكثر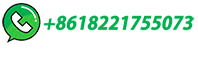
Review on vertical roller mill in cement industry & its …
India is the world's second largest producer of cement and produces more than 8 per cent of global capacity. Due to the rapidly growing demand in various sectors such as defense, housing, commercial and industrial construction, government initiative such as smart cities & PMAY, cement production in India is expected to touch 550–600 …
اقرأ أكثر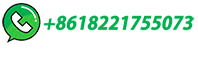
Grinding Mills and Their Types
The vibrating mill has a grinding chamber which is filled to around 65 % to 80 % of its capacity with grinding media such as balls or rods. The chamber is vibrated at a frequency of between 1000 and 1500 times per minute (can be variable speed) by cams or unbalanced weights.
اقرأ أكثر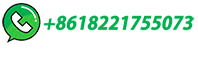
Functional Performance of Ball Milling Circuits – A Plant …
Mill grinding efficiency measures the capacity of the grinding mill to convert feed-sized material into product-sized material on a tonnes per kilowatt hour basis.
اقرأ أكثر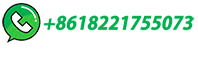
A Review of the Grinding Media in Ball Mills for Mineral …
Operational parameters such as grinding media filling, pH, mill speed and wear also affect ball mill efficiency. Grinding media with low wear rates are the most …
اقرأ أكثر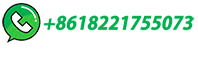
(PDF) Effects of Ball Size Distribution and Mill Speed and …
In recent research done by AmanNejad and Barani [93] using DEM to investigate the effect of ball size distribution on ball milling, charging the mill speed with 40% small balls and 60% big balls ...
اقرأ أكثر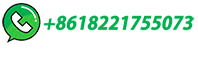
Choosing the Right Grinding Mill: SAG Mill vs Ball Mill
Sag Mill is a kind of heavy duty equipment used in the ore crushing and grinding industry. Its working principle is to utilize the impact and grinding effect of a small amount of steel balls and the material itself to crush the ore Through the rotation of the cylinder, large pieces of ore are gradually broken into smaller particles in the collision …
اقرأ أكثر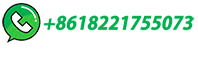
Cryomill
This results in reduced consumption and guarantees reproducible cryogenic grinding results. The CryoMill is very easy to operate. Parameters such as oscillation frequency, pre-cooling or grinding time can be digitally set via a clearly structured keypad. ... A 25 ml grinding jar of zirconium oxide and matching grinding balls as well as a PTFE ...
اقرأ أكثر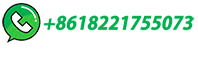
17 Signs of Problems with Ball Mills: Quickly …
3.There is a large amount of ball wear in the ball mill In the grinding operation, the consumption of the steel ball accounts for more than 10 times of the liner of the ball mill. Here are the reasons for it: …
اقرأ أكثر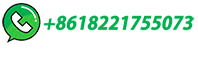
Cryo Milling | Material Milling
Cryo Milling Services. AVEKA uses liquid nitrogen to lower the temperature of the material and/or the milling process. AVEKA uses cryogenic hammer mills that can typically reduce the particle size from small pellets down to the 100s of microns.
اقرأ أكثر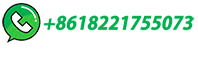