Direct Reduced Iron: The New Age of HBI
increased use of direct reduction, producing direct reduced iron (DRI), and especially, hot-briquetted iron (HBI) Low-Carbon Innovations. As the steel industry moves toward carbon neutrality in response to increasing pressures to decarbonize, the application of DRI and HBI will see immediate benefits for steel producers. HBI is an exceptionally ...
اقرأ أكثر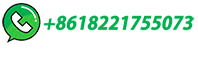
Flowchart of production of reduced iron from mill scale.
Presently, the industrial-grade iron powder produced from the atomization and electrolysis route is the most expensive. However, obtaining reduced iron powder from the mill scale by reduction ...
اقرأ أكثر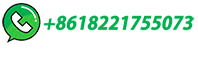
(PDF) Production of reduced iron from mill scale waste …
In our recent research, we were able to produce reduced iron in the form of spheres with a 93% metallization degree using only mill scale as a source of iron without the need for any agglomeration ...
اقرأ أكثر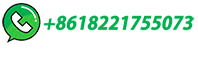
Direct-Reduced Iron
Direct reduced iron is iron ore in the form of lumps, fines or pellets that have had the oxygen removed by using hydrogen and carbon monoxide. ... Fuelled by the scenario of a shortage of scrap iron and the increase in steel mini mills as alternatives to integrated steel plants, the production of direct reduced iron (DRI) in the form of ...
اقرأ أكثر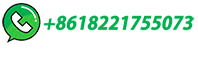
From Ore to Iron with Smelting and Direct Iron …
The specific iron content of the direct reduced iron is a function of the iron content of the iron ore. Depending on the quality of …
اقرأ أكثر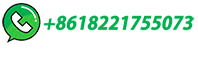
Use of Direct Reduced Iron (DRI) in the Electric Arc
The past 5 years have seen increases in the supply and use of Pig Iron, Direct Reduced Iron (DRI), and Hot riquetted Iron (HI) in the EAF. ... • DRI is shipped as old DRI, but in integrated DRI/EAF mills can be charged hot directly to the EAF (furnace discharge temperature is 650-700°)
اقرأ أكثر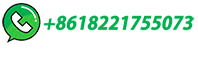
Elaboration of iron powder from mill scale
The analyses of the metal Fe content in the reduced samples show that the mill scale can be used successfully in the direct reduction process to produce sponge iron. In the rolling mill scale-iron ...
اقرأ أكثر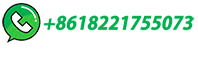
Production of reduced iron from mill scale waste using tilting …
In this study, mill scale waste produced in steel companies was recycled into spheroidal high metallization reduced iron that can be used as a feed stock in the iron …
اقرأ أكثر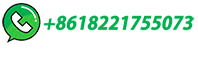
(PDF) Characterization of Iron Powder Produced by …
mill-scale and reduced iron powders at di erent reduction . temperatures. This may be due to the lower porosities of the . powder after shaking. In addition, higher apparent densities .
اقرأ أكثر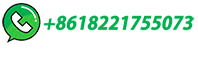
Hydrogen-Based Reduction Technologies in Low-Carbon …
The traditional ironmaking technologies (including coking, sintering, pelletizing, and BF ironmaking process) are carbon-intensive, which makes the industry a significant contributor to global CO2 emissions. Hydrogen replacement of carbon in steelmaking processes is a sustainable way to reduce CO2 emissions. First, the …
اقرأ أكثر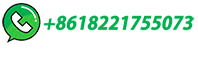
Production of reduced iron from mill scale waste using …
The production of steel in steel mills generates undesired scales of oxidized iron on the surface of the hot steel. Although several attempts have been made to transform mill scale into valuable products, the low porosity of the oxides and the presence of oil contamination have been the main limitations in pelletizing the scales. In our recent research, we were …
اقرأ أكثر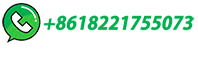
Direct Reduced Iron: The New Age of HBI
By implementing direct reduction, iron and steel producers are able to reduce CO 2 emissions significantly. What makes the global transformation of the iron and steel industry so exciting?
اقرأ أكثر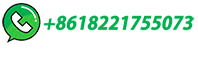
Novel insights into the reoxidation of direct reduced iron …
Direct reduced iron (DRI), obtained by this process, is a high-purity iron-containing raw material which can be used to smelt high-purity steel and special steel [6] ... Since the ball mill used in this research is a vertical semi-wet ball mill which is a reduced version of the most widely used mill in industrial production of this process. The ...
اقرأ أكثر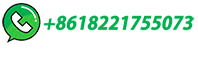
Investigation on the Coal-Based Direct Reduction of Mill
The feasibility of producing direct reduced iron from pellets made up of mill scale by utilizing coal as a reductant has been investigated. The chemical and morphological characterization studies reveal that the mill scale contains around 71% Fe and comprises of a mixture of iron oxide phases such as magnetite and hematite with a …
اقرأ أكثر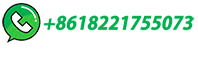
(PDF) Preparation of Reduced Iron Powders from Mill Scale …
The optimum conditions resulted in reduced iron powders with a total iron content of 98.60 pct and a metallization ratio of 98.71 pct. X-ray fluorescence (XRF) was used to estimate the elemental ...
اقرأ أكثر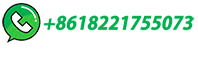
Direct Reduction Process
The pellets can be rapidly reduced at 1250–1350 °C for 10–20 min to obtain direct reduced iron, which can be used back in steel mills for smelting after treatment. Valuable elements such as Zn are reduced to metal vapor to be volatilized and removed from the pellet, and the metal vapor is oxidized and enters the flue gas collection system ...
اقرأ أكثر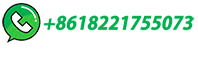
Industrial Plants in Gary and Other Environmental Justice …
A 2019 assessment by the EPA shows that fugitive emissions from iron and steel mills could be reduced by approximately 65 percent. "We're asking EPA to be more ambitious as it revises the rule ...
اقرأ أكثر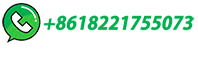
How to Make Steel: Blast Furnace Vs. Electric Arc Furnace
This reduced form of iron is steel. The extractive process is particularly emissions-heavy because CO 2 is a byproduct of both steps along the way – the blast furnace and the basic oxygen furnace. Furthermore, the process always requires the extraction of natural resources from the earth.
اقرأ أكثر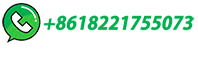
FACTS ABOUT AMERICAN STEEL SUSTAINABILITY
Integrated steel mills in the United States are almost entirely fed by domestically sourced iron ore pellets vs. sintered ore used in China and elsewhere. The use of pelletized iron …
اقرأ أكثر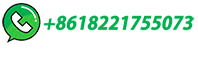
Production of reduced iron from mill scale waste using …
In Egypt more than 200 thousand tons of mill scales are dumped as a waste due to the steel rolling annually. We implemented our findings in the pilot scale into a production …
اقرأ أكثر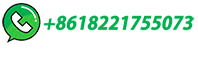
Preparation of reduced iron powder using combined distribution of …
This study presents the research results of preparation process of reducing product, high-grade reduced iron powders from mill-scale with wood-charcoal as the reducing agent by carbothermal reduction using microwave heating. And its microstructure of the samples was characterized before and after microwave treatment using SEM.
اقرأ أكثر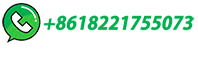
Novel insights into the reoxidation of direct reduced iron …
Further, the deeper iron atoms are more exposed after the defected iron surfaces combine with O 2, greatly increasing contact opportunities of Fe O 2. Therefore, the reduction time should be appropriately extended to decrease the surface defects of new iron, and other wet ball mills should be selected for the treatment of DRI produced by …
اقرأ أكثر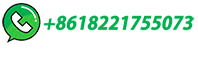
Direct reduced iron process
In the direct-reduced iron (DRI) process, the iron ores are reduced directly to sponge iron by gaseous reducing agents! Electro-steel process. In the electric steel process, the sponge iron obtained from the direct reduced iron process is used for crude steel making. In general, scrap is also added to this process as well as pig iron from the ...
اقرأ أكثر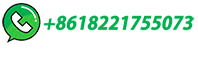
DRI production | International Iron Metallics …
Ore-based metallics - merchant pig iron (MPI), direct reduced iron (DRI), hot briquetted iron (HBI), granulated pig iron (GPI) - are value-adding feedstock materials for the iron & steel and ferrous casting industries …
اقرأ أكثر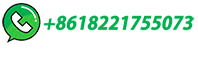
Preparation of Reduced Iron Powders from Mill Scale with …
Preparation of the reduced iron powder has been attempted with mill scale as the iron-bearing material and with wood charcoal as the reducing agent through microwave heating. The response surface methodology (RSM) is used to optimize the process conditions, with wood charcoal, process temperature, and holding time being …
اقرأ أكثر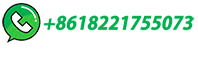
Overview on production of reduced iron powder from mill …
The oxide of mill scale and reduced Iron powder have their scope of application in numerous segments. However, the accumulation and disposal of mill scale as a waste product has become an increasingly important issue. It must be dealt with appropriately to meet the inevitably strict environment and ecological necessities to …
اقرأ أكثر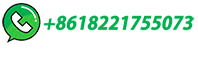
Direct Reduced Iron (DRI)
Hot rolled coil is rolled on a hot strip mill from slabs. Wire Rod. Hot rolled from steel billet, wire rod is delivered as coil, most commonly. ... Reduced iron derives its name from the chemical change that iron ore undergoes when it is heated in a furnace at a high temperature of 800 to 1200 °C in the presence of a reducing gas called syngas ...
اقرأ أكثر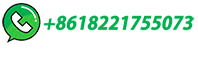
a) SEM of reduced iron powder. (b) SEM of reduced iron …
It was reported that mill scale iron powder with more than 99% degrees of metallization, 97% total Fe, and more than 96% metallic Fe was synthesized after 4 h of reduction at 1200 °C and 1300 °C ...
اقرأ أكثر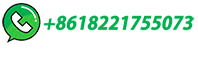
Reduction characteristics of oily hot rolling mill sludge by …
Oily hot rolling mill () sludge including high amount of iron was recycled by the direct reduced iron (DRI) method. The oil component in the sludge which should be removed in order to reuse ...
اقرأ أكثر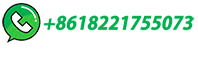
America's 1st 'green steel' plant coming to Perry County
These new hydrogen-direct reduced iron plants will retain existing workers and further grow the union workforce. Between the two plants, developers project they will create 7,200 construction jobs ...
اقرأ أكثر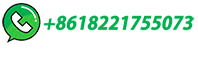