Analysis of material flow and consumption in cement production …
In the surveyed cement plant, three balances are established between input and output material in the raw mill, clinker production, and cement grinding system. 2.48 t, 4.69 t, and 3.41 t of materials are required to produce a ton of the product in raw material preparation, clinker production, and cement grinding stages; waste gases account for ...
اقرأ أكثر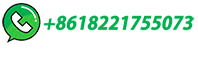
Comparative Analysis of Rod Mill and Ball Mill
Ball mill machine has always been the main grinding equipment in wet cement production. In the early years, the rod mill was first used in cement raw meal grinding, which increased the output of the grinding section by 31%, saved energy by 27%, and reduced the consumption of grinding media by 47%.
اقرأ أكثر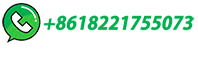
Analysis of the efficiency of the process in closed circuit …
Analysis of the efficiency of the grinding process in closed circuit ball mills Valery I. Telichenko1, Rashid R. Sharapov1*, Svetlana Y.Lozovaya2 and Vladimir I.Skel1 1Moscow State University of Civil Engineering, Moscow, Russia 2Belgorod State Technological University named after V.G. Shukhov, Belgorod, Russia Abstract. Ball mills for fine …
اقرأ أكثر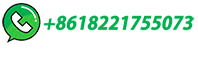
Multi-Model Control of Cement Combined Grinding Ball Mill …
In this paper, an optimal tracking control method based on adaptive dynamic programming is proposed to solve the control problem of cement combined grinding ball mill system. The two key indexes of cement particle size and ball mill load can reach the expected value. According to the actual production situation, several typical working conditions of …
اقرأ أكثر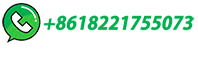
Cement Grinding Unit & Process | High Quality …
At the Cement Grinding Stage, 90 – 95% of the clinker is mixed with gypsum and ground in a Cement Ball Mill to produce quality cement OPC 43 and OPC 53. In case of PPC Cement, there is an addition of Fly Ash.
اقرأ أكثر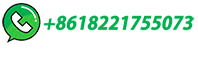
Mill drives
Central drive with two-stage planetary gear (Maag-Zahnriider AG, Switzerland) This central drive was specially developed for the drive of ball mills. ... The largest planetary gears for ball mill drives in the cement industry supplied at this writing by the Maag Gear Wheel Co., have a transfer capacity of 8 MW. Since 1967 to 1982, about 70 ...
اقرأ أكثر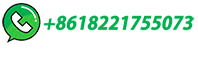
Cement Mill Optimization: Practical Strategies for Enhanced …
Adjusting mill parameters: Fine-tuning mill parameters such as mill speed, ball charge, filling ratio, and grinding media size can have a substantial impact on the grinding efficiency of the mill. For example, a 10% increase in mill speed can result in up to 10% higher production rate, while optimizing the ball charge can lead to a 5-10% ...
اقرأ أكثر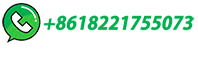
Cements ground in the vertical roller mill fulfil the …
The application of both the ball mill and the roller mill in the cement industry are explained in detail. The main flow diagrams of grinding and firing of coal by the roller mills are included and ...
اقرأ أكثر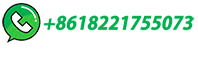
polysius® booster mill
Additional stage grinding meets challenges of cement grinding. Throughout the last decades, cement grinding technology shifted from ball mills to combi-grinding systems and vertical roller mills. Compared to ball mills, energy efficiency improved significantly. Especially for vertical roller mills, also flexibility improved (e.g. quick switches ...
اقرأ أكثر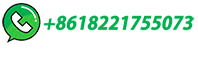
Optimization of Cement Grinding Operation in Ball Mills
Clinker, Gypsum and other desired additives are fed to the ball mill in specific proportions based on the quality requirement. Feed material is ground in the ball mill, discharged and fed to a classifier with the help of a bucket elevator for classification of the ground cement into two streams – coarse and fines.
اقرأ أكثر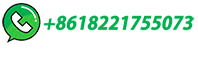
BALL MILL FOR ALL YOUR NEEDS
choose dry ball mill, such as cement, marble and other construction stone; Dry Ball Mill: Ⅰ. It is mainly used in chemical and ceramic industries; Ⅱ. The wet ball mill with wide range applica- ... and can also be used in the second stage of grinding, so it is widely used. FOTE BALL MILL 07 The Structures of Ball Mill
اقرأ أكثر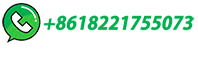
BALL MILLS Ball mill optimisation
Ball mills and grinding tools Cement ball mills are typically two-chamber mills (Figure 2), where the first chamber has larger media with lifting liners installed, providing the coarse …
اقرأ أكثر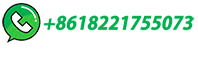
The Cement Plant Operations Handbook
mentioned in Chapter 3 for dry raw milling – ball mills, vertical roller mills, roll presses, Horomill – in combination with separators and other optional ancillaries. The finished …
اقرأ أكثر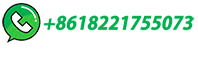
Ball mill for cement grinding
An inefficient ball mill is a major expense and could even cost you product quality. The best ball mills enable you to achieve the desired fineness quickly and efficiently, with minimum energy expenditure and low maintenance. With more than 4000 references worldwide, the FL ball mill is proven to do just that.
اقرأ أكثر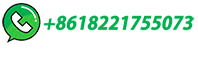
Ball Mill & Roller Press for Cement Grinding Process
The two stage grinding system. The two stage grinding system is developed from the combined grinding system of roller press and ball mill. This system performs even better on energy saving, and also solves the worn problem of the cyclone and the circulating fan.
اقرأ أكثر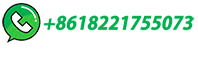
Cement Ball Mill Maintenance
Ball mill is the largest consumption equipment of mining plant. The ball mill's operating state directly influences the whole mill plant productivity. It's also the biggest investment equipment of mill plant, and the wastage …
اقرأ أكثر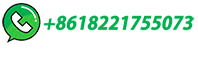
(PDF) Ventilation Prediction for an Industrial Cement Raw Ball Mill …
In the cement industry, grinding is one of the most consuming energy stages in the . ... Also, using the study done in two similar cement ball mills in the same cement plant, almost 1000000-ton ...
اقرأ أكثر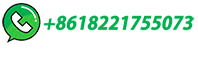
Cement Ball Mill | Cost Effective Cement Grinding Mill from …
The installation of liners. Length Diameter Ratio. The length-diameter ratio of the cement ball mill is relatively large. For mills of open-circuit grinding system, the length-diameter ratio is usually between 3.5 and 6 to ensure that the product fineness is qualified through single grinding; For ball mills in closed-circuit grind system, in order to increase the …
اقرأ أكثر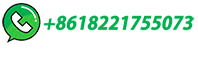
Comparison of the overall circuit performance in the cement …
The results show that high compression grinding mill circuits are more energy efficient than conventional single stage multi-chamber ball mill circuits. The circulating load ratio around the circuit is much higher compared to conventional ball milling. ... This study explored the breakage kinetics of cement clinker in a lab-scale ball mill ...
اقرأ أكثر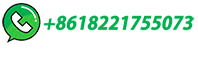
Manufacturing process
The preheater-kiln system consists of a multi-stage cyclone . preheater with five stages, combustion chamber, riser duct, rotary kiln, and grate cooler. In the preheater, the kiln feed is preheated by hot gas coming from the combustion chamber and rotary kiln. ... The clinker is taken from the clinker storage to cement ball mill hoppers for ...
اقرأ أكثر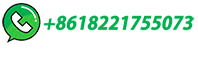
Review on vertical roller mill in cement industry & its …
The cement mill is either a Ball mill with two chambers or Vertical roller mill with inbuilt classifier. Material is ground till desired Blaine is achieved and then final product is stored in concrete silos for further blending. ... In line calciner six stage preheater & Kiln: Cement clinker is made by pyro processing of kiln feed into the ...
اقرأ أكثر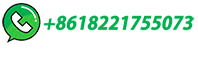
Cement Manufacturing—Technology, Practice, and …
The mixture is then ground into a powder that creates cement in ball mill-like equipment. The powder is hardened when mixed with water. The name Portland was given by the inventor as it resembles a stone quarried on the Isle of Portland. ... State-of-the-art suspension preheater kilns have 5–6 cyclone stages with a maximum capacity …
اقرأ أكثر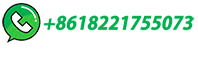
Ball Mill
A ball mill is a type of grinder containing various metal balls of different sizes that work on the principle of impact and attrition. ... since a single stage ball mill approximates closely to a completely mixed system. ... Usually, for large scale operations, as in the case of raw-meal grinding mills or cement mills, only continuous mills are ...
اقرأ أكثر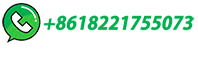
Grinding process is a critical stage in cement production
• CPI & LNVT Ball Mill: CPI & LNVT is a renowned manufacturer of grinding equipment for the cement industry. Their ball mills are widely used for grinding cement clinker, gypsum and other materials into a fine powder. The ball mill operates by rotating a horizontal cylinder, filled with steel balls, which impact and grind the material as it ...
اقرأ أكثر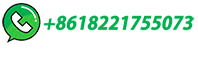
OPTIMIZATION OF CEMENT GRINDING OPERATION IN …
Operation and Elements of a Closed-Circuit Ball Mill System . Cement ball mills typically have two grinding chambers. The first chamber is filled with larger diameter grinding …
اقرأ أكثر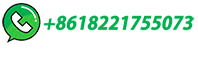
Influence of milling of a reused FCC catalytic waste on the …
The catalytic residue Recat was collected from an oil refinery FCC unit and stored in closed containers. A Portland Special Cement for Oil Wells (CPP), regulated by standard NBR 9831/08 [] and distilled water were used to prepare the pastes.Recat sample was dry milled in a planetary ball mill, model PM 100, in a grinding jar of 500 mL, which has a high …
اقرأ أكثر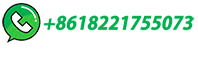
Ball Mill In Cement Plant
Of course, even if we set a more appropriate cement fineness, it is difficult to change the current situation that the flow velocity in the open-circuit ball mill is only 1/2-1/3 of that in the closed-circuit ball mill with the same …
اقرأ أكثر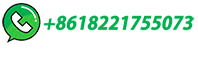
The Cement Manufacturing Process
To produce powdered cement, the nodules of clinker are ground to the consistency of powder. Grinding of clinker, together with additions of approximately 5 percent gypsum to control the setting properties of the cement can be done in ball mills, ball mills in combination with roller presses, roller mills, or roller presses.
اقرأ أكثر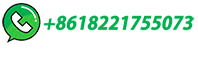
Improving cement production through Artificial Intelligence
Ball mills have been around since the late 1800's, playing a crucial role in the production of cement. The second-to-last stage of cement production happens in mills, where clinker is ground from a size of several centimeters into pieces less than 100 microns in size. That is smaller than a grain of beach sand!
اقرأ أكثر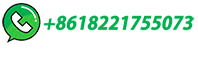
The Monarch Process
The kiln feed heads next to 2 separate preheater pre-calciner rotary kiln lines. Hot gases travel through the kiln and up through each of four separate stages prior to being sent to the baghouse or roller mill. As the heat rises up the tower, the kiln feed is pneumatically conveyed to the top stages of the tower.
اقرأ أكثر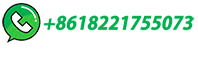