cement grinding Unit
High grinding efficiency. For the structure, of the cement mill, we adopt the advanced obstructing equipment for internal powder, add the activated device to the fine grinding chamber, and there is the special grate plate …
اقرأ أكثر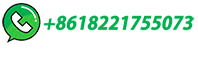
Cement Manufacturing Process- Wet and Dry Processes
Grinding: The cooled Clinker is finely ground with Gypsum (Calcium Sulphate) and other additives, such as fly ash or slag, in a Cement mill. This grinding process produces Cement powder. Storage and Packaging: The Cement powder is stored in silos before being packed into bags or delivered in bulk to construction sites for use in …
اقرأ أكثر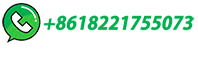
Cement Production Seminar: Grinding
This 3-day seminar covers ball and vertical mills with a focus oncomminution theory, design basis, operational principles, control and regulation, process troubleshooting, calculation methods, and optimization. The seminar offers classroom instruction from FL specialists and case studies based on real situations at different cement plants.
اقرأ أكثر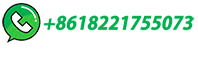
Clinker Grinding Techniques in Cement Manufacturing
Ball Mill: In some cement plants, a ball mill is used to grind clinker into a fine powder. It relies on the use of steel balls to crush and grind the clinker. Ball mills are often used for grinding cement clinker into a fine powder before it is mixed with other materials to produce cement.
اقرأ أكثر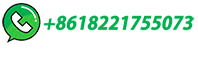
Ball mill for cement grinding
It protects the shell while ensuring optimum lifting of the mill charge. In the second compartment (and also in our one-compartment cement mills) we use a corrugated lining designed to obtain the maximum power absorption and grinding efficiency. For special applications, we can supply a classifying shell lining for fine grinding in the mill.
اقرأ أكثر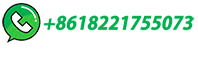
OK™ Raw and Cement Mill
Our best-in-class OK™ Mill is a globally successful vertical roller mill solution for grinding raw material, cement and slag. Its cutting-edge design features consistently deliver the highest quality products with the greatest efficiency. It is affordable to install and cost effective to operate over your cement plant's lifetime.
اقرأ أكثر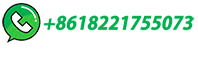
PROCESS CONTROL FOR CEMENT GRINDING IN VERTICAL ROLLER MILL …
The power ingesting of a grinding process is 50-60% in the cement production power consumption. The Vertical Roller Mill (VRM) reduces the power consumption for cement grinding approximately 30-40% associated with other grinding mills. The process variables in cement grinding process using VRM are strongly nonlinear and having …
اقرأ أكثر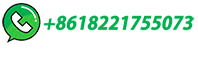
Vertical Cement Mill
Providing Consistent Results With Advanced Vertical Cement Mill Technology. Magotteaux's advanced vertical cement mill technology ensures consistent results by providing precise control over the grinding process, enabling the production of high-quality cement with minimal variations in fineness..Moreover, our use of advanced materials …
اقرأ أكثر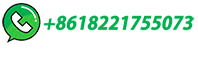
OPTIMIZATION OF CEMENT GRINDING OPERATION IN …
Condition in one of the grinding chambers of the mill . Results of Optimization . The graphical analysis presented in Figure 2 represents progress of grinding along the length of the mill after optimizing the grinding process. rogress of grinding is clearly visible in Desired p the graphs. Figure -2: Analysis of longitudinal samples.
اقرأ أكثر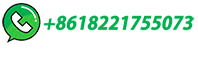
Cement Grinding
This phase of grinding may be either the wet or dry process, the end product going to a kiln. Material ground consists of limestone, cement rock, marl or marine shells along with secondary materials usually shale or clay. ... Cement Grinding Mills. Material Handled 585 – 620# raw material yields 1 BBL cement (376#) or average ratio …
اقرأ أكثر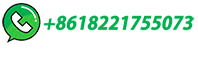
PROCESS CONTROL FOR CEMENT GRINDING IN …
The power ingesting of a grinding process is 50-60% in the cement production power consumption. The Vertical Roller Mill (VRM) reduces the power consumption for cement grinding approximately 30-40% associated with other grinding mills. The process variables in cement grinding process using VRM are strongly nonlinear and having …
اقرأ أكثر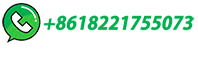
GRINDING TECHNOLOGY COURSE
A 6-week modular course is designed to give the course attendee a solid understanding of the grinding system and its auxiliary equipment. The purpose of the training is to Identify and understands necessary known and unknown information towards the completed cycle of the grinding system, whether it is a ball mill, vertical mill, or crushing process.
اقرأ أكثر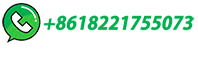
polysius® Ball Mill
The proven classical option for cement grinding. Whether employed as a two-compartment separator mill in an independent grinding system, or in combination with a high pressure grinding roll, the Ball Mill is a robust and reliable alternative for cement and granulated blast furnace slag grinding.. Used in combination with the sepol® high-efficiency …
اقرأ أكثر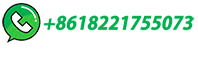
The Cement Plant Operations Handbook
6. Cement milling Finish milling is the grinding together of clinker with some 3-5 per cent gypsum, natural or synthetic, for set control, and quite often other components: …
اقرأ أكثر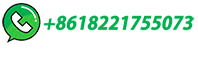
Cement Mill Optimization: Practical Strategies for …
The grinding process in cement mills consumes a significant amount of energy and has a direct impact on the overall efficiency of the mill. By optimizing the grinding process, cement manufacturers can achieve …
اقرأ أكثر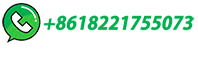
Vertical Roller Mill Operation in Cement Plant
The vertical roller mill (VRM) is a type of grinding machine for raw material processing and cement grinding in the cement manufacturing process.In recent years, the VRM cement mill has been equipped in more and more cement plants around the world because of its features like high energy efficiency, low pollutant generation, small floor area, etc.. The …
اقرأ أكثر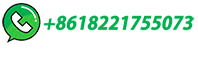
How Is Cement Produced in Cement Plants | Cement Making Process
The laboratory of a cement plant. With the help of vertical roller mills or other types of crushers, the raw materials are blended and further ground into smaller pieces of raw meal in the cement plant. In a roller mill, the rotating roller rotates continuously on the grinding table and crushes the material to fine powders, and finishes the job.
اقرأ أكثر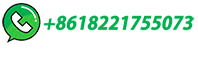
The Cement Plant Operations Handbook
Providing a comprehensive guide to the entire cement production process from raw material ... Finish mill – 12. Cement – 13. Quality control – 14. Packing and distribution – 15. Emission abatement (dust, NO ... Cement milling Finish milling is the grinding together of clinker with some 3-5 per cent gypsum,
اقرأ أكثر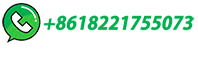
Grinding in Ball Mills: Modeling and Process Control
The paper presents an overview of the current methodology and practice in modeling and control of the grinding process in industrial ball mills. Basic kinetic and energy models of the grinding ...
اقرأ أكثر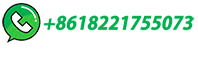
Ball Mill Grinding Machines: Working Principle, Types, Parts
Cement Industry: Ball mills are extensively used in the cement industry for grinding raw materials, clinker, and additives to produce cement. The ability to finely grind materials and control the grinding process makes ball mills crucial equipment in cement manufacturing. Mining and Ore Processing: Ball mills are used for grinding ores and ...
اقرأ أكثر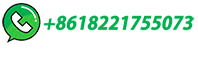
OPTIMIZATION OF CEMENT GRINDING OPERATION IN …
Optimization addresses the grinding process, maintenance and product quality. The objective is to achieve a more efficient operation and increase the production rate as …
اقرأ أكثر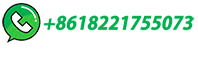
Ball Mill
In another variation, commonly known as air-swept mills, the body is more or less similar to that of trunnion overflow mills, but the fine product is forced out of the mill by powerful stream of air, which passes through the mill. In the wet process of cement manufacture, the raw meal grinding is done in the presence of water, which is known as ...
اقرأ أكثر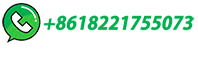
PROCESS CONTROL FOR CEMENT GRINDING IN …
The power ingesting of a grinding process is 50-60% in the cement production power consumption. The Vertical Roller Mill (VRM) reduces the power consumption for cement …
اقرأ أكثر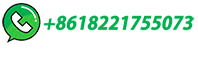
Cement Manufacturing Process
Cement Manufacturing Process Phases. Production of cement completes after passing of raw materials from the following six phases. These are; ... Material is directly conveyed to the silos (silos are the large storage tanks of cement) from the grinding mills. Further, it is packed to about 20-40 kg bags. ...
اقرأ أكثر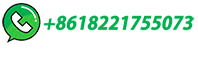
Cement Grinding Unit & Process | High Quality Cement Grinding …
At the Cement Grinding Stage, 90 – 95% of the clinker is mixed with gypsum and ground in a Cement Ball Mill to produce quality cement OPC 43 and OPC 53. In case of PPC Cement, there is an addition of Fly Ash.
اقرأ أكثر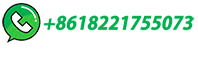
Cement Finish Milling (Part 1: Introduction & History)
Although concrete is the most sustainable building material available [1], with over 4 billion tonnes of cement produced and consumed world-wide, optimisation of the grinding process can provide ...
اقرأ أكثر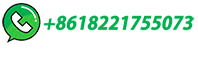
The cement mill
Cement clinker is usually ground using a ball mill. This is essentially a large rotating drum containing grinding media - normally steel balls. As the drum rotates, the motion of the balls crushes the clinker. The drum …
اقرأ أكثر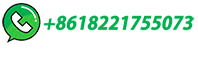
Cement Grinding
Cement grinding operation may be performed in one of the following mill setups. Ball and tube mills. Vertical Roller Mills (VRM). Roller press with Ball mill. Ball Mill. Ball mills …
اقرأ أكثر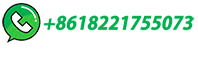
Cement Grinding
6 Cement Production Technology –Cement Grinding –Mechanical Design and Function of Separator Separators –General Classification of Separating Principles •according to flow direction relative to particle track •according to kind of separating field separation by gravitational force separation by centrifugal force
اقرأ أكثر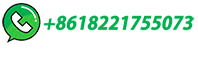
Fives | High-efficiency classifier: FCB TSV™ Classifier
Easy and efficient classification for mineral and cement grinding mills. For a grinding mill to reach optimal performance levels, it needs to incorporate a highly efficient classifier that separates fine product from coarse materials. ... The possibility of concentrating product in a dry process where two fractions show a density difference ...
اقرأ أكثر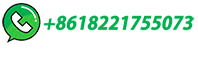