Industrial Solutions polysius ball mills
ball mills, but also from our comprehensive scope of services, ranging from maintenance and OEM spares procurement to the optimization of existing plants. The grinding unit most commonly used for grinding brittle materials, such as cement, is still the ball-filled ball mill. The following types can be found: • single-compartment mills,
اقرأ أكثر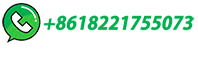
(PDF) Grinding Media in Ball Mills-A Review
One of the most used tumbling mills is the ball mill. This paper reviews different types of grinding media that have been developed and improved over the years and their properties.
اقرأ أكثر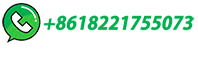
(PDF) IMPROVING THERMAL AND ELECTRIC ENERGY EFFICIENCY AT CEMENT PLANTS
IMPROVING THERMAL AND ELECTRIC ENERGY EFFICIENCY AT CEMENT PLANTS: INTERNATIONAL BEST PRACTICE. March 2019; ... Download full-text PDF Read full-text. Download full-text PDF. ... In a ball mill ...
اقرأ أكثر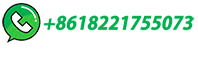
(PDF) Performance Evaluation of Vertical Roller Mill in Cement …
PDF | In this study, an extensive sampling study was carried out at vertical roller mill of ESCH Cement Plant in Luxemburg. Samples were collected from... | Find, read and cite all the research ...
اقرأ أكثر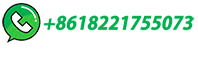
Energy and exergy analyses for a cement ball mill of a new …
Nowadays, ball mills are used widely in cement plants to grind clinker and gypsum to produce cement. In this work, the energy and exergy analyses of a cement ball mill (CBM) were performed and ...
اقرأ أكثر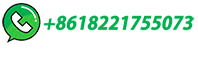
MODELING AND SIMULATION OF A CLOSED LOOP BALL …
A cement ball mill is a grinder that grinds the clinker to produce fine cement. It works on the principle of impact. The functioning of ball mill is further discussed in this study.
اقرأ أكثر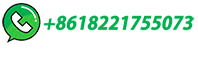
Grinding in Ball Mills: Modeling and Process Control
An overview of the current methodology and practice in modeling and control of the grinding process in industrial ball mills is presented. Abstract The paper presents an overview of the current methodology and practice in modeling and control of the grinding process in industrial ball mills. Basic kinetic and energy models of the grinding process …
اقرأ أكثر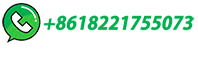
OPTIMIZATION OF CEMENT GRINDING OPERATION IN …
OPTIMIZATION OF CEMENT GRINDING OPERATION IN BALL MILLS Several energy efficient options for cement grinding are available today such as vertical roller mills, roller …
اقرأ أكثر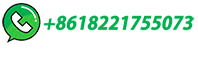
Roller Press
Simply put, the roller press is the most energy-efficient grinding machine on the market. Since its commercial introduction into the cement industry by KHD in the 1980s, hundreds of them have been installed in the cement and minerals industries, in both finish and semi-finish applications. And with the lowest specific energy consumption among comparable …
اقرأ أكثر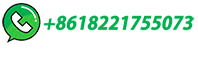
Wear Resistance Improvement for Grinding Balls of Horizontal Cement …
The one of main problem in cement industry is the continouse abrasion in lining plates of cement mill as a result of impact, abrasive and erosion by steel balls grinding media inside cement mill.
اقرأ أكثر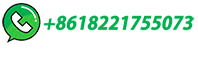
Cement Roller Press
Semi-finishing grinding system: after ground by cement roller press, materials are divided into three parts through an air classifier: coarse, medium and fine, in which the coarse material is returned to the roller press for re-grinding, the medium material is put into a ball mill for further grinding, and the fine material is directly discharged as the finished …
اقرأ أكثر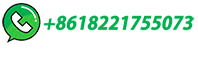
Thomas Holzinger, Holzinger Consulting, grinding …
Comparison of cement grinding systems for ordinary portland cement at 3500 Blaine, 4% limestone. Ball mill Combi grinding system Finish grinding Ball mill with cage rotor separator Roller press in semi-finish mode and ball mill VRM Roller press Spec.el Energy consumption mill motors kWh/t 30 25 17 17 % at mill motor (ball mill ) % 100 83 …
اقرأ أكثر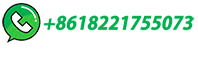
Cement Plant Operations Handbook 5
Cement Plant Operations Handbook 5th Edition 15 Contents SAMPLEProcess Summaries 1. Introduction 20 2. Raw Materials 23 ... Clinker Storage – 2. Cement Milling – 3. …
اقرأ أكثر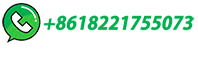
OPTIMIZING THE CONTROL SYSTEM OF CEMENT …
operation of a cement mill, directly extracted from the plant database. In each extraction two days worth of data are loaded, with a sampling period of one minute. Then the software checks for feeder stop-pages and finds continuous operational data sets of 250 minutes duration. In parallel it detects the ce-== s, A (m)
اقرأ أكثر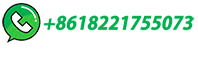
Ball Mill
The characteristic tumbling motion of these mills has given them the name 'tumbling mills', which include the ball mill, tube mill and rod mill. Ball mills are horizontal rotating cylindrical or conical steel chambers, approximately one third to half full of steel, alloy steel or iron balls, like that shown in Fig. 4.10 A–C, or flint stones.
اقرأ أكثر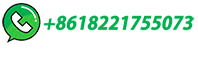
(PDF) Ventilation Prediction for an Industrial Cement Raw Ball Mill …
PDF | In cement mills, ventilation is a critical key for maintaining temperature and material transportation. ... Nowadays, ball mills are used widely in cement plants to grind clinker and gypsum ...
اقرأ أكثر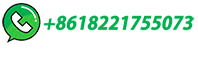
(PDF) DESIGN AND ANALYSIS OF BALL MILL INLET CHUTE …
Ball mills (Fig 1.1) are coming in cement plant areas of raw grinding, coal grinding and cement grinding which in turn as raw mill, coal mill and cement mill. Ball mills are horizontal tube mills having single or two compartments for grinding, Balls as grinding media and driven by side or central drive.
اقرأ أكثر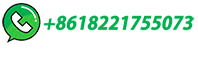
THE NEED FOR EFFECTIVE RISK MITIGATION IN …
THE NEED FOR EFFECTIVE RISK MITIGATION IN CEMENT PLANTS THE NEED FOR EFFECTIVE RISK MITIGATION IN CEMENT PLANTS ... Traditionally the ball mill (which is also known as the tube mill) is used for grinding and pulverizing of the cement clinker. Generally a closed circuit
اقرأ أكثر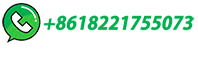
OK™ Raw and Cement Mill
Our best-in-class OK™ Mill is a globally successful vertical roller mill solution for grinding raw material, cement and slag. Its cutting-edge design features consistently deliver the highest quality products with the greatest efficiency. It is affordable to install and cost effective to operate over your cement plant's lifetime.
اقرأ أكثر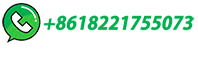
Energy and cement quality optimization of a cement grinding circuit
The model structure for the one-chamber or multi-chamber cement ball mills have been subject of various researchers. Benzer et al. [21] developed model for open circuit two-chamber cement ball mill. In their structure, the first and second chamber of the ball mill as well as the intermediate diaphragm were all model fitted hence calibrated …
اقرأ أكثر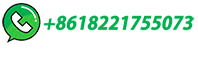
The cement mill
Cement manufacturing - brief description of a cement mill. Cement clinker is usually ground using a ball mill. This is essentially a large rotating drum containing grinding media - normally steel balls. As the drum rotates, the motion of the balls crushes the clinker. The drum rotates approximately once every couple of seconds.
اقرأ أكثر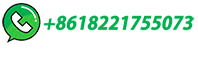
CEMENT PLANT TALK-001
Mill Feeding: Periodic variation in composition and size of material. Grinding in Ball Mill: First chamber loading and consequently jamming. Blending Silo: Mill variation affecting kiln stability quickly. Coal Mill: Mill Bag filter jamming. Kiln Fluctuating Free lime in clinker. Cement Mill: Mill tripping at higher cement temperature.
اقرأ أكثر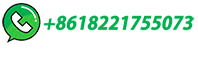
HOLLY HILL CEMENT PLANT
The Holly Hill (SC) cement plant was constructed in 1966 by the plant's founders, Lawrence E. Miller and William J. Colvin. The original facility included a 12-foot ... which over time grew into two kiln lines and four finish mills. In 2003, the old plant was demolished and a new one was built in its place. • 1.1 to 2.2 million metric tons ...
اقرأ أكثر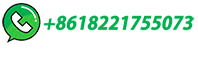
Cement grinding Vertical roller mills VS ball mills
Vertical roller mills and ball mills represent two clearly distinct technologies. However, with proper adjustments to the operational parameters of the vertical roller mill almost identical cement properties can be achieved by the two mills that satisfy the cement user's demands.Nevertheless, the two types of mills have their distinctive merits.
اقرأ أكثر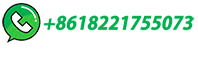
Closed and Open Circuits Ball Mill for Cement, …
We bring forth a highly advanced Ball Mill, specifically engineered for both wet as well as dry cement grinding applications. Classified depending on the circuit design, bearing, grinding type and drive, the selection is made …
اقرأ أكثر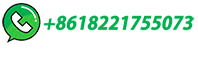
Digitization and the future of the cement plant | McKinsey
When envisioning the cement plant of the future, it is important to understand the reference for a typical plant today. Our reference plant is a five-stage preheater-calciner kiln with a vertical raw mill and two cement ball mills. It has an annual production capacity of one million metric tons of cement and produces several types of …
اقرأ أكثر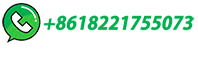
Predictive Controller Design for a Cement Ball …
The annual cement consumption in the world is around 1.7 billion tonnes and is increasing by 1% every year [].Cement industries consume 5% of the total industrial energy utilised in the world [].A total …
اقرأ أكثر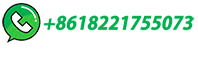
(PDF) Grinding in Ball Mills: Modeling and Process …
The paper presents an overview of the current methodology and practice in modeling and control of the grinding process in industrial ball mills. Basic kinetic and energy models of the grinding...
اقرأ أكثر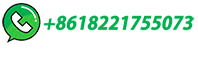
(PDF) Cement plant operation handbook
Download Free PDF. Download Free PDF ... Cement plant operation handbook. jorge pinedo sanchez. See Full PDF Download PDF. See Full PDF Download PDF. Related Papers. Category Title NFR: 2.A.1 Cement production SNAP: 040612 Cement ISIC: 2694 Manufacture of cement, lime and plaster. Pradeep Nayak.
اقرأ أكثر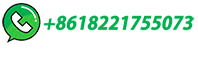
Cement Roller Press
The cement roller press, also known as roller press in cement plant, high pressure grinding roll (HPGR), is a kind of cement equipment for brittle materials, apply for grinding cement clinker, cement raw material, …
اقرأ أكثر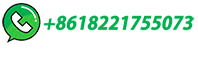