Optimal Control of Accretion Growth and …
Minimum response time of a large coal fired rotary kiln (80 m in length) is approximately 3-4 hours. ... The technology of predicting and controlling accretion formation is explained in detail in ...
اقرأ أكثر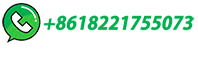
A Case Study on Accretion Formation in Rotary Kiln of DRI …
Request PDF | A Case Study on Accretion Formation in Rotary Kiln of DRI Process A Case Study on Accretion Formation in Rotary Kiln of DRI Process | Your article is protected by copyright and all ...
اقرأ أكثر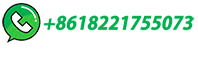
A Case Study on Accretion Formation in Rotary Kiln of DRI …
Accretion formation in a rotary kiln of 100 tpd DRI plant has been investigated. The nature of accretion formation with respect to the charge burden and operational parameter have been discussed. High ash content in the coal and excess …
اقرأ أكثر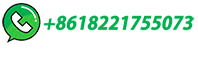
Conventional and AI Models for Operational Guidance and …
The fines and ash content of coal enhance the accretion formation and must be regulated within a certain window for the process to be steady (for prediction purposes as well). ... and MLR multiple-based models along with dynamic pressure control is demonstrated for quality and accretion control in rotary kiln on shop floor. Quality is ...
اقرأ أكثر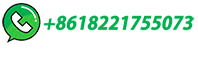
Dynamic quality prediction and control in rotary sponge iron …
For quality prediction and control purposes, the One Step Ahead Adaptive Control and Prediction Algorithm (OSAA) and Grey (1,1) prediction algorithm have been …
اقرأ أكثر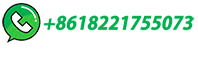
Valuation of % metallization and % accretion formation …
and minimization of accretion formation inside the rotary kiln, thereby facilitates longevity of kiln life expectancy. 2. Rotary kiln operation The inclined rotary kiln acts as the back-bone of the sponge iron production process. Its efficiency has a paramount effect on the quality of the output product.
اقرأ أكثر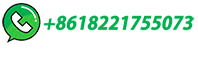
Schematic diagram of plant and the rotary kiln (see arrow) …
For example, sudden changes in LE are caused when accretions inside the kiln get dislodged. The technology of predicting and controlling accretion formation is explained in detail in [1][2] [3] [4 ...
اقرأ أكثر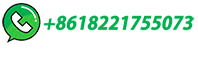
Understanding the co-relationships of variables and …
S. Mondal, Operation of Coal-Based Sponge Iron Rotary Kiln to Reduce Accretion Formation and Optimize Quality and Power Generation, 2012, pp. 727–732.
اقرأ أكثر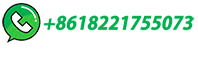
Improving the rotary kiln-electric furnace process for …
Improving the rotary kiln-electric furnace process for ferronickel production: Data analytics-based assessment of dust insufflation into the rotary kiln flame ... This phenomenon is known as accretion or ring formation. Ring formation can also be due to the presence of carbon-containing fines at high temperatures (1200–1400 …
اقرأ أكثر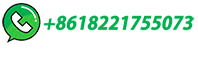
Ring Formation in the Smelting of Saprolite Ni-ore in a …
long time that the formation of ring-shaped accretion on the inside wall of the kiln cannot be avoided by any possibility, which causes serious trouble in the kiln operation. This is attributed to the liquid formation within the solid, which is an inevitably occurring phenomenon. A similar phenome-non has been reported in the cement kiln.3)
اقرأ أكثر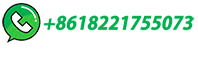
Rings growth behavior within a pre-reduction rotary kiln: …
Inhibiting the Accretion in the Coal-Fired Rotary Kiln of High-Silica Iron Ore Pellets Application by Reducing Fines Generation and Liquid Phase Formation ... The ring formation in rotary kiln is a complicated process,which obstructs the development of grate-kiln production.In the experiment of ring formation in the acid pellet gas heated ...
اقرأ أكثر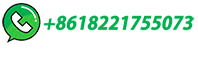
Rotary Kiln Process (ACCAR / SL – RN / Krupp CODIR)
The discharge end of the Rotary Kiln is provided with a burner, which is used for start up and / or ... Accretion formation in Sponge Iron kiln is attributable to the formation of low melting ...
اقرأ أكثر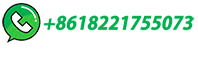
Trouble-Free Construction of a Large Diameter Waelz Kiln
Tests demonstrate absence of accretion formation in the reaction zone, and an increase in Waelz kiln lining life in the Ust-Kamenogorsk Lead and Zinc, and Leninogorsk Polymetal Combines by a factor of 1.6 – 1.8. ... The most worn lining of rotary kilns is that of a Waelz kiln due to severe operating conditions: high temperature (1400 …
اقرأ أكثر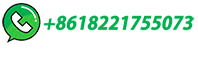
Operation of Coal-Based Sponge Iron Rotary Kiln to …
Sponge iron is the final product of coal fired rotary kilns. The schematic diagram in Fig. 1 describes the unit processes ... This is because enhanced accretion formation leads to premature ...
اقرأ أكثر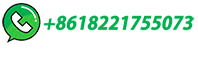
Method for removing accretions in grate kiln
The invention provides a method for removing accretions in a grate kiln. The method is characterized by including the steps that when the number of the accretions in the rotary kiln exceeds a limit value, constant-temperature finished product balls with the number larger than conventional pellet input are directly input into the rotary kiln through a feed …
اقرأ أكثر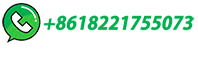
Dynamic quality prediction and control in rotary sponge iron kilns
[7] Mondal S, Choudhary P, Borah S, Deo B, Sahoo S K, Malakar P, Pothal G and Chattopadhyay P 2019 Operation of Coal-Based Sponge Iron Rotary Kiln to Reduce Accretion Formation and Optimize Quality and Power Generation AIS Tech Proceedings PR-377-076. Google Scholar
اقرأ أكثر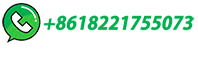
Operation of Coal-Based Sponge Iron Rotary Kiln to Reduce Accretion …
Sponge iron is the final product of coal fired rotary kilns. The schematic diagram in Fig. 1 describes the unit processes involved in a sponge iron a production plant [1]. ... But this is counterproductive for coal consumption per ton of sponge and also for accretion formation. Low melting point materials are formed at high temperature during ...
اقرأ أكثر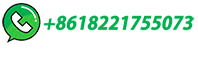
Pressure Measurement and Control in Rotary Kilns at …
Pressure Measurement and Control in Rotary Kilns at TATA Sponge Iron ... promotes accretion formation. Thus, the control of pressure inside the kiln is the first requirement of an
اقرأ أكثر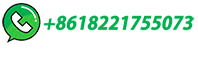
The Deposit Formation Mechanism in Coal-Fired Rotary Kiln …
The deposit-forming problem is one of the main bottlenecks restricting the yield and production benefit of iron ore pellets produced by coal-fired rotary kilns. In order to implement measures to ensure the efficient production of pellets by coal-fired rotary kilns, the mechanism and influencing factors on the deposit formation were reviewed. …
اقرأ أكثر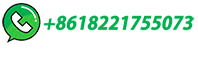
Inhibiting the Accretion in the Coal-Fired Rotary Kiln of …
mation were collected from the rotary kiln at 4-m intervals. Each sample was taken from a different position around the wall surface of the rotary kiln and labeled as S-1 to S-10. Figure 1 illustrates a sampling diagram showing the formation of depos-its in the rotary kiln of iron ore pellets. The samples were crushed and mixed according to Chinese
اقرأ أكثر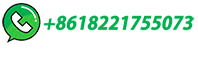
Quality Prediction and Control in Coal-Fired Rotary …
The control of reduction process inside the rotary kiln is complicated by the fact that the kiln is long (80 meters) and no samples can be taken from inside the continuously rotating kiln.
اقرأ أكثر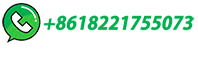
Accretion Control in Sponge Iron Production Kiln using …
of the kiln for several days. Accretion build up or ring formation in the kiln is normally caused by the deposition of low melting complex compounds on the refractory wall of the rotary kiln which gradually increases in thickness and takes shape of a circular ring. This narrows the kiln diameter which ends up hindering material
اقرأ أكثر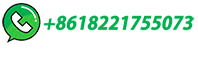
(PDF) Accretion Build Up Resistant Refractories for Sponge Iron Kilns
The discharge end of the Rotary Kiln is provided with a burner, ... Accretion formation in Sponge Iron kiln is attribut able to the formation of low melting eutectic in. Silica ...
اقرأ أكثر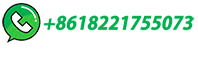
Understanding the co-relationships of variables and …
S. Mondal, Operation of Coal-Based Sponge Iron Rotary Kiln to Reduce Accretion Formation and Optimize Quality and Power Generation, 2012, pp. 727–732. ... A study on the accretion formation in DRI kilns and possible ways for its reduction. IOSR J. Mech. Civil Eng., 12 (2015), pp. 98-103. CrossRef Google Scholar [7]
اقرأ أكثر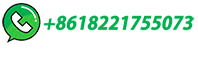
Operation of Coal-Based Sponge Iron Rotary Kiln to Reduce …
The temperature profiles of the gas and charge in a coal-fired rotary sponge iron kiln affect both the iron ore reduction process and accretion formation.
اقرأ أكثر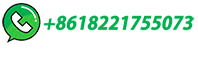
FeO-SiO2 Phase diagram. | Download Scientific Diagram
Accretion formation in a rotary kiln of 100 tpd DRI plant has been investigated. The nature of accretion formation with respect to the charge burden and operational parameter have been discussed.
اقرأ أكثر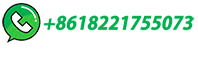
Formation Mechanism of Deposits in Rotary Kiln during …
Rotary kiln has been widely used in hazardous waste treatment because of its strong adaptability to raw materials, high productivity, and simple processing technology. However, the formation of deposits reduces its performance period and profitability. This study characterized the deposit mineralogy and thermodynamically and experimentally …
اقرأ أكثر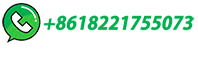
Accretion Control in Sponge Iron Production Kiln …
process is presented. Then, the general accretion formation and rotary kiln process parameters is outlined. Furthermore, the design of the proposed FLC design is presented. Finally, the designed model simulation results were be reported. 2. Kiln Based Sponge Iron Production Process Rotary kilns are found in many processes that involve
اقرأ أكثر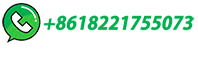
Accretion Control in Sponge Iron Production Kiln using …
Then, the general accretion formation and rotary kiln process parameters is outlined. Furthermore, the design of the proposed FLC design is presented. Finally, the designed model simulation results were be reported. Other advanced control strategies including fuzzy control [9], intelligent control [10] and predictive control have been ...
اقرأ أكثر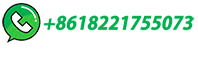
Rotary kiln process: An overview of physical mechanisms, …
The rotary kiln is used in many solid processes, including drying, incineration, heating, cooling, humidification, calcination and reduction. This widespread application can be attributed to factors such as the ability to handle varied loads, with large variations in particle size [1].The rotary kiln is a slightly inclined steel cylinder that rests …
اقرأ أكثر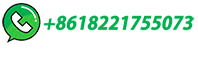