High-energy ball milling of nonstoichiometric compounds
Let us consider in brief a model of mechanical powder milling to a smaller particle size [34–39] and its applicability to estimating the powder particle size as a function of the milling energy E mill, mass M of the initial powder and particle size D in of the initial powder.The particle volume and surface area in an initial powder are equal to and, …
اقرأ أكثر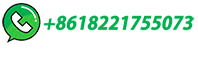
XRD Line Profile Analysis of Ball Milled ODS Ferritic Steel …
Abstract In this study, an ODS ferritic steel powder of composition Fe–12Cr–2W–1Zr–0.2Y (in wt %) was mechanically alloyed in a planetary ball mill, until …
اقرأ أكثر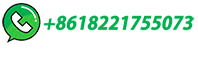
Lattice Ball Mill_Henan Hongke Heavy Machinery Co., Ltd.
Product Specification: Φ900*1800-Ф5500×8500 Product Output: 0.65-2t/h-108-615t/h Application Fields: Used for processing cement, silicates, new building materials, refractory materials, fertilizers, enrichment of ferrous and non-ferrous metal ores, glass ceramics and other materials.
اقرأ أكثر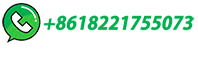
STEEL MILLING BALLS FOR BALL MILLS
STEEL MILLING BALLS FOR BALL MILLS Specifications DSTU 8538-2015 Official publication Kiev SE "UkrNDNC" 2016 . ... Center of Metallurgical Industry «Energostal», TK 2 "A long products, rolled section stock and special profiles". THE STANDARD DEVELOPERS: A. Vladimirova, E. Kosogonova, Y. Pikhtin, PhD in Technical
اقرأ أكثر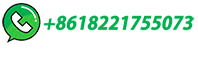
Lattice Ball Mill_Henan Hongke Heavy Machinery Co., Ltd.
Lattice ball mill is composed of feeding part, discharging part, rotating part, transmission part (reducer, small transmission gear, motor, electric control) and other main parts. The …
اقرأ أكثر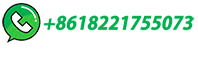
Structural disorder and phase transformation in graphite …
Carbon. EXPERIMENTAL The ball milling was carried out in a conventional planetary ball mill. Pure graphite (99.9%, average particle size less than 200 [im) powder was put into a hard bearing steel vial under a dry pure argon atmosphere. The total weight of the powder was 10g. The ball milling was performed with aball-to-powder weight …
اقرأ أكثر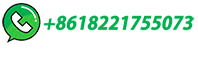
Grinding Ball Design
Grinding Ball Design. Table of Contents. Grinding balls are essential mechanical components in ball and semiautogenous (SAG) mills. Their function is …
اقرأ أكثر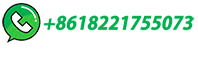
Synthesis of nanostructured Al–Mg–SiO2 metal matrix …
High energy ball milling is carried out in a planetary ball mill (Fritsch pulverisette P-5) at room temperature using WC vials and balls as milling media and toluene as process controlling agent (PCA) for the four different compositions as shown in Table 1.The materials used in this study are 99.7% pure Al powder, 99% pure Mg …
اقرأ أكثر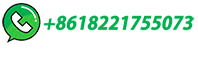
Research progress on synthesis mechanism and performance …
As a practical method of mechanochemical action, ball milling was first proposed by John Benjamin in 1970 18.It can usually cause particle deformation, lattice defects, local hot spots on the ...
اقرأ أكثر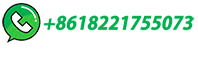
Correlation between defect density in mechanically milled …
In ball-milling, the material is pulverized by the friction between the metal balls and the metal bowl. Ratio of weight of graphite to the weight of the stainless steel metal balls was taken as 1:25.
اقرأ أكثر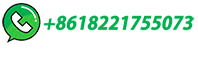
Exploring ball milling theory: A comprehensive guide
Ball milling is a mechanical process that involves the rotation of a drum containing grinding media, typically steel balls, at a high speed. The materials to be milled are loaded into the drum, and as the drum rotates, the grinding media collide with the materials, causing them to break down and reduce in size.
اقرأ أكثر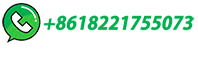
Nanocrystalline/nanoparticle ZnO synthesized by high energy ball
Ball milling was performed in different milling times using a high energy planetary ball mill machine (Retsch PM100). The milling container was consisting of 15 balls with diameter of 20 mm confined in a 500 ml bowl. Both the ball and bowl materials were made from hardened chromium steels.
اقرأ أكثر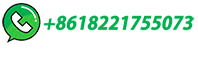
Lattice Ball Mill
Lattice ball mill is composed of feeding part, discharging part, rotating part, transmission part (reducer, small transmission gear, motor, electric control) and other main parts. The hollow shaft is made of cast steel, and the inner lining is removable. The large rotary gear is processed by casting gear hobbing. The cylinder is inlaid with ...
اقرأ أكثر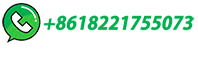
Ball Mills
Steel Ball Mills & Lined Ball Mills. Particle size reduction of materials in a ball mill with the presence of metallic balls or other media dates back to the late 1800's. The basic construction of a ball mill is a cylindrical …
اقرأ أكثر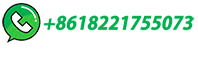
X-ray line profile analysis of the ball-milled Fe–30Co alloy
Alloy formation in solid state can also be confirmed by the evaluation of the lattice parameter a.The refinement of the XRD patterns shows that a rapidly decreases from 0.28670 ± 0.00003 nm (bcc-Fe) to 0.28564 ± 0.00004 nm just after 3 h of milling which corresponds to a compression of the lattice parameter by 0.37%.This decrease of …
اقرأ أكثر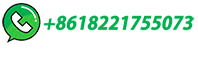
Grinding Ball Design
Grinding balls are essential mechanical components in ball and semiautogenous (SAG) mills. Their function is crushing and grinding ore rocks weighing up to 45 kg (100 lb) preparatory to recovery of valuable minerals, from lead through rare earth elements, which are essential to the approaching 21st century technological society.
اقرأ أكثر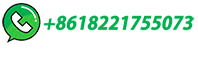
What is Profile Milling | Profile Milling Process, …
The milling cutters for profile milling including round inserts and concepts with radius for roughing and semi-roughing, and ball nose end mills used for finishing and super-finishing. Choose the proper tool …
اقرأ أكثر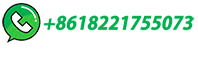
Effect of ball milling on the sintering performance of indium …
The mechanisms inducing lattice distortion and grain boundary diffusion in mixed In2O3-Ga2O3-ZnO (IGZO) powders were investigated during ball-milling treatment at different rotation speeds.
اقرأ أكثر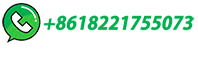
Role of particle size, grain size, microstrain and lattice …
The decreased dehydrogenation temperature and improved dehydrogenation kinetics were achieved by high-energy ball milling Mg(AlH 4) 2.The particle size, grain size, microstrain and lattice distortion of the post-milled samples, i.e., from macro- to micro-scale, were systematically characterized by means of SEM and XRD …
اقرأ أكثر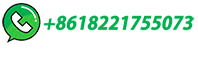
(PDF) Effect of Particle Size and Lattice Strain on the Debye …
Iron (Fe) powder was ball milled in an argon inert atmosphere. The milled powders were characterized by X-ray diffraction. The high-energy ball milling of Fe after 20 h resulted in particle size ...
اقرأ أكثر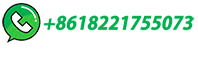
Structural and mechanical evaluation of a new Ti-Nb-Mo …
The main focus of this work is to investigate the impact of varying milling times (2 to 18 h) on the structural and mechanical properties of the developed Ti-Nb-Mo alloy. The morphology, phase composition, microstructure, and mechanical behavior of milled and sintered Ti-25Nb-25Mo alloy samples were characterized systematically …
اقرأ أكثر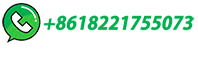
Nature and density of lattice defects in ball milled …
Abstract. Copper powder of 99.9% purity with particle size in the micrometer range was subjected to high energy ball milling by milling times between 2 and 24 h …
اقرأ أكثر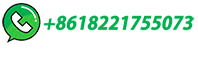
Changing the game of time resolved X-ray diffraction on the
Reactions were conducted in custom-made polymethylmethacrylate (PMMA) jars (see Supplementary Note 2 for details), using 1 stainless-steel milling ball (8 mm diameter for Reactions I and II, 7 mm ...
اقرأ أكثر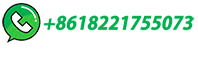
Structural transformation of porous and disordered carbon during ball
The samples are obtained by mechanical milling using a ball-milling apparatus (QM-1SP2, Nanjing University Instrument Factory, China). 0.2 g AC (YP-50F, Kuraray Co. Ltd., Japan) and 40 g agate balls were put into an agate milling jar (50 mL) installed by a stainless-steel container in air. Then ball-milling was carried out from 1 to …
اقرأ أكثر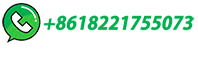
The Art of Milling
Metal Separation Samples such as industrial waste, recyclable waste and sec-ondary fuels often contain metallic components which cannot be pulverized with laboratory mills. On the contrary, metallic objects such as steel nails or iron screws can damage the grinding tools which can lead to a considerable deterioration of the mill's performance.
اقرأ أكثر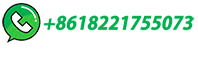
Magnetic properties of ball-milled SrFe12O19 particles
The ball milling was done with a Planetary Mill PULVERISETTE 5 classic line with two grinding-bowl fasteners and a revolution speed of 150 rpm. A ball-to-powder ratio of 6:1 was used with 35 ml of ...
اقرأ أكثر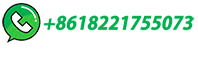
STEEL MILLING BALLS FOR BALL MILLS Specifications
percentage in steel shall be no less than 0.60%;0.80% for balls with rated diameter of 70-120 mm provided that carbon weigh. rcentage in steel shall be no less than 0.65%. The …
اقرأ أكثر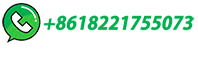
Effect of High-Energy Ball Milling on the Structural and …
In the present work, nanocrystalline binary Fe60Al40 (wt.%) powders have been synthesized by a high-energy planetary ball mill under an inert argon atmosphere. …
اقرأ أكثر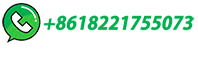
Ball Mills for Lithium Ore
The productivity of the lattice ball mill is about 20% to 30% higher than that of the overflow ball mill. 2. Lithium ore overflow ball mill ... The barrel of the overflow ball mill is welded with a steel plate with a thickness of 15-36mm. Cast steel flanges are welded to both ends of the barrel. The end cover and the flange are connected with ...
اقرأ أكثر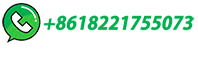
Evolution of crystallite size, lattice parameter and internal …
Plastic deformation of the Al 87 Ni 8 La 5 powder by ball milling resulted in two characteristic changes in the XRD patterns which are (i) a shift and (ii) broadening of …
اقرأ أكثر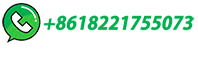