Nanomaterials | Free Full-Text | Mechanical Milling: A …
Ball milling experiments were done in a high energy planetary ball mill at a rotating speed of 300 rpm. To avoid the occurrence of any undesirable polluted phases, the ball-milling experiments were halted periodically (every 1.8 ks) and then restarted when the temperature of the vial reached about 300 K.
اقرأ أكثر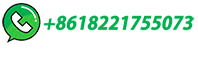
Planetary Ball Mills
If the material of the grinding jars and balls has a high density, like tungsten carbide, acceleration of the grinding balls is higher at a given speed compared to materials of lower density. ... In the planetary ball mill, every grinding jar represents a "planet". This planet is located on a circular platform, the so-called sun wheel. When ...
اقرأ أكثر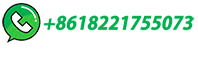
Ball Mills – fritsch.de
The comminution of the material to be ground takes place through impact and friction between the grinding balls and the inside wall of the grinding bowl respectively the mortar. The grinding can be performed dry or wet. In addition to comminution Ball Mills are also the ideal and reliable lab assistants for mixing and homogenising.
اقرأ أكثر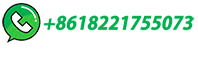
Overview of milling techniques for improving the solubility …
Fundamentally, a ball mill comprises a vessel or vial filled with balls, or rods, constructed from a variety of materials such as ceramic, agate, silicon nitride, sintered corundum, zirconia, chrome steel, Cr–Ni steel, tungsten carbide or plastic polyamide (Fig. 2). The material to be milled is placed inside the vessel, which is made to ...
اقرأ أكثر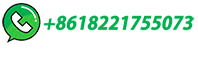
Ball Milling Method for Synthesis of Nanomaterials
For all nanocrystalline materials prepared by high-energy ball milling synthesis route, surface and interface contamination is a major concern. In particular, mechanical attributed contamination by the milling tools (Fe or WC) as well as ambient gas (trace impurities such as O 2, N 2 in rare gases) can be problems for high-energy ball milling ...
اقرأ أكثر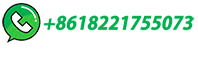
Ball Milling
Ball milling is a mechanical technique that involves grinding solid materials using hard balls like stainless steel or tungsten to prepare nanosized metal particles with desired …
اقرأ أكثر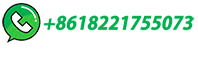
Bronze Age of Direct Mechanocatalysis: How Alloyed Milling Materials
2 Results. In a typical synthesis, two milling balls (diameter ≈10 mm) were placed together with 55 μL (0.5 mmol, 1a) phenylacetylene and 3.0 g (21.7 mmol) K 2 CO 3 as base and bulking material in a 25 mL ZrO 2 milling vessel and milled at 30 Hz in an MM400 (for detailed procedure and characterization, see ESI). As a starting point, we …
اقرأ أكثر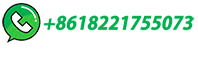
Ball Milling | Powder Processing | 30 Years of Expertise at …
Ball Milling Services. ... Ball milling is a size reduction technique that uses media in a rotating cylindrical chamber to mill materials to a fine powder. As the chamber rotates, the media is lifted up on the rising side and then cascades down from near the top of the chamber. With this motion, the particles in between the media and chamber ...
اقرأ أكثر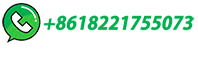
Research progress on synthesis mechanism and performance …
As a practical method of mechanochemical action, ball milling was first proposed by John Benjamin in 1970 18.It can usually cause particle deformation, lattice defects, local hot spots on the ...
اقرأ أكثر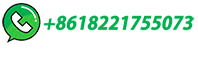
Ball Milling
It is well known as a novel synthesis technique to prepare materials in nanometer scale and non-equilibrium state. It has been widely adopted by researchers to prepare Mg …
اقرأ أكثر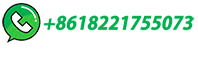
Enhanced microwave absorption performance of FeSiBCCr …
After 4 h of ball milling, the FeSiBCCr alloy powder showed a lamellar structure with a certain thickness (Fig. 1b). As the ball milling time increased to 8 and 12 h, most of the FeSiBCCr alloy particles had a thin lamellar structure and their shape anisotropy increased significantly (Fig. 1c, d). It can be seen that after 4 h of ball milling ...
اقرأ أكثر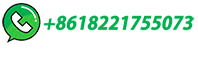
The Ultimate Guide to Understanding Ball Mill Diagrams
The wet ball mill is usually preferred when the material to be ground is wet, such as in the case of ore processing. On the other hand, the dry ball mill is suitable for grinding dry materials, such as cement, limestone, and coal. The ball mill diagram is essential for understanding the operation of the ball mill.
اقرأ أكثر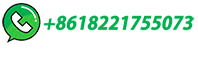
Ball Mill Grinding Machines: Working Principle, Types, Parts
Explore the working principle, types, parts, applications, advantages, and recent developments of ball mill grinding machines. Discover how these versatile tools …
اقرأ أكثر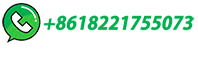
Planetary Ball Mills
Product details. Background information. Details on the fields of application, working mechanisms and materials used in planetary ball mills. Learn more. 2 grinding stations. …
اقرأ أكثر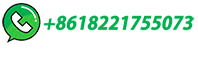
Ball Mill: Operating principles, components, Uses, …
The balls which could be of different diameter occupy 30 – 50 % of the mill volume and its size depends on the feed and mill size. The large balls tend to break down the coarse feed materials and the smaller balls help to form fine product by reducing void spaces between the balls. Ball mills grind material by impact and attrition.
اقرأ أكثر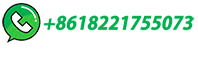
Recent Developments on the Synthesis of Nanocomposite Materials …
This review is focused on the topical developments in the synthesis of nanocomposites using the simplest top-down approach, mechanochemical milling, and the related aspects of the interfacial interactions. Milling constraints include time duration of milling, ball size, the ball-to-sample content proportion, rotation speed, and energy that …
اقرأ أكثر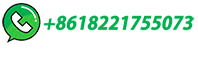
Ball Milling of La2O3 Tailors the Crystal Structure, Reactive …
Ball milling of these La 2 O 3 photocatalysts is found to increase the amount of oxygen vacancies on their surfaces and thereby the amount of 1 O 2 species produced by them. ... Characterization of La 2 O 3 materials, computational details, and La 2 O 3 materials . am3c15677_si_001.pdf (5.43 )
اقرأ أكثر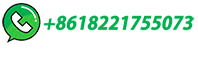
Microwave Absorption Properties of Flaky Carbonyl Iron @ Fe
In this work, large-diameter flaky carbonyl iron (FCI) and FCI@Fe3O4 composite materials were prepared by employing a simple plasma-assisted ball milling and heat treatment process. Large FCI was obtained, with 30-70 μm diameters and a thickness of 300 nm. The results show that, compared with the original polycrystalline …
اقرأ أكثر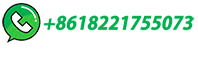
Effects of Ball Milling on the Electrochemical Capacity and …
The cycling mechanism of Li2MnO3 cathode materials synthesized by conventional solid-state methods at high temperatures (800–900 °C) has been intensively investigated. Previous studies showed that CO2 and O2 gas evolution accounts for most of the charge capacity, followed by some Mn reduction during discharge. In this work, we analyze the …
اقرأ أكثر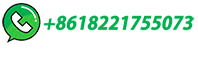
Ball Mill: Operating principles, components, Uses, …
A ball mill also known as pebble mill or tumbling mill is a milling machine that consists of a hallow cylinder containing balls; mounted on a metallic frame such that it can be rotated along its longitudinal axis. …
اقرأ أكثر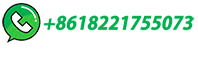
Ball Milling-Enabled Fe2.4+ to Fe3+ Redox Reaction in …
Aqueous Na-ion batteries using Prussian blue materials have inherent advantages in safety, material sustainability, and economic cost. However, it is challenging to obtain long-term cycling stability because many redox reactions have poor intrinsic stability in water. Here, we demonstrate reversible Fe2.4+ to Fe3+ redox reaction of …
اقرأ أكثر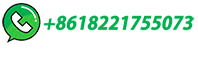
Ball Mill Liner Design
There are many different designs and styles of ball mill liners. As with grinding balls local economics and ultimately operating costs determine the best design and material to use. The initial set of liners is …
اقرأ أكثر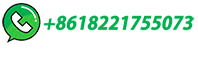
What is a ball mill and What are Its Advantages and …
Applications of ball mill. Cement industry: The ball mill is commonly used for grinding cement clinker and gypsum to produce cement. Mineral processing: The ball mill is widely used in ore processing plants to grind various ores and other materials. Ceramic industry: The ball mill grinds different ceramic materials, such as clay, quartz, …
اقرأ أكثر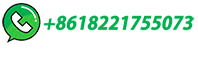
A contact-electro-catalysis process for producing reactive …
Ball milling is a representative mechanochemical strategy that uses the mechanical agitation-induced effects, defects, or extreme conditions to activate substrates. Here, we demonstrate that ball ...
اقرأ أكثر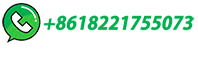
Ball mill: Principles, construction, working, uses, merits, and
A ball mill is a type of grinder or mill used to mill the materials into fine powder in pharmaceutical, chemical, or metallurgical industries. Ball milling relies on the impact and attrition between the balls impacting the material to …
اقرأ أكثر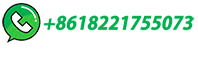
Ball Mill Success: A Step-by-Step Guide to Choosing the …
In the intricate dance of ball milling, where raw materials are transformed into finely milled particles, the choice of grinding media emerges as a pivotal performance lever. This seemingly minor selection can dramatically influence the efficiency of the milling process, the quality of the output, and, ultimately, the bottom line.
اقرأ أكثر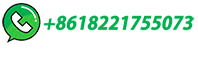
Ball-milling in liquid media : Applications to the preparation …
The ball-milling was directly oriented to industrial applications: in 1966, Benjamin (INCO Co.) tried to improve the mechanical properties of nickel-based superalloys by high energy mechanical grinding. ... when stainless steel balls (softer than the vial material) with 5 or 10 mm diameter are used, the pollution remains low: the iron content ...
اقرأ أكثر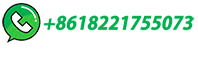
Environmental Mechanochemistry: Recycling Waste into Materials …
Recycling Waste into Materials using High-Energy Ball Milling. ... The text reviews 1017 studies utilizing mostly high-energy ball milling for the treatment of various types of consumer, technogenic and agricultural waste. The text is divided into chapters based on individual waste types. The book presents an Appendix compiling all studies ...
اقرأ أكثر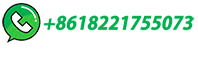
High-Energy Ball Milling
It involves the use of a high energy ball mill to initiate chemical reactions and structural changes. High energy ball milling: Mechanochemical processing of nanopowders reviews the latest techniques in mechanochemistry and how they can be applied to the synthesis and processing of various high-tech materials.
اقرأ أكثر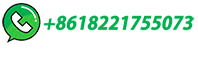
Ball milling – A green and sustainable technique for the preparation …
The ball milling method is classified as vibration mill, planetary mill and magneto-ball mill depending on the movement of the balls and vessel and among them, the planetary mill is the most common as it has been used to reduce the particle size of many materials. The ball milling process induces a reduction in the particle and …
اقرأ أكثر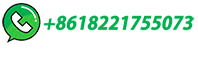