How to Manufacture Pig Iron: How Pig Iron is made?
Guide for manufacturing and making Pig Iron. Following three distinct operations are involved in the manufacturing process of pig-iron: (1) Dressing (2) Calcination and roasting (3) Smelting. (1) Dressing: The iron ores as obtained from mines are crushed into pieces of size of 25 mm diameter. This is achieved in the rock crushers of ordinary type. The …
اقرأ أكثر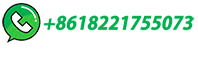
Gold Refinery Process: From Raw Material to Pure Gold
Common impurities found in gold ore include silver, copper, iron, and sulphur. These impurities need to be separated and removed through various refining processes to obtain pure gold. Refining Process Steps to Follow. The initial step in the gold refinery process involves the extraction of gold ore from the ground.
اقرأ أكثر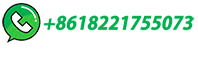
Gold processing | Refining, Smelting & Purifying …
gold processing, preparation of the ore for use in various products.. For thousands of years the word gold has connoted something of beauty or value. These images are derived from two properties of gold, its colour …
اقرأ أكثر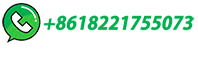
Vedanta Aluminium patents innovative breakthrough in bauxite refining
The process reduces bauxite residue by a remarkable 30% by eliminating iron values while simultaneously recovering a higher alumina yield, reducing the total organic content from bauxite during the alumina refining. The process significantly enhances resource efficiency and curbs energy consumption during refining.
اقرأ أكثر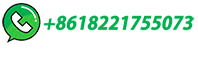
How to Extract Iron from Hematite: Methods and Plants
Medium-grained hematite refers to iron ore with an embedded particle size between 0.02 and 2mm. This type of hematite is also relatively easy to select, mainly using gravity separation, magnetic separation and magnetic roasting. Fine-grained hematite refers to iron ore with an embedded particle size of less than 0.02mm. Based on the genesis …
اقرأ أكثر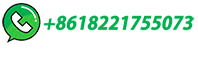
How is Silver Mined | In-Depth Guide to Silver Mining
The extraction of silver ore is a complex process. It begins with drilling and blasting to break up the rock containing the silver. This ore is then transported to a processing facility where the real magic begins. Separating Silver from Ore. At the processing plant, the ore undergoes a series of crushing, grinding, and beneficiation …
اقرأ أكثر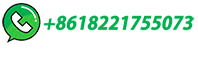
Metallurgical Machinery
Gas-based process is mostly Midrex process or HYL process, with million tons annual production capacity of large equipment. In iron ore smelting reduction process, combustion of injected coal allows the iron ore or concentrate in molten state to be reduced into molten iron. Smelting reduction process is mostly COREX process.
اقرأ أكثر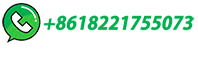
From Ore to Iron with Smelting and Direct Iron …
Smelting Reduction. Figure 2: The smelt reduction vessel (SRV) is the core technology component of the Hismelt process. …
اقرأ أكثر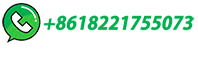
Iron Ore Processing: From Extraction to Manufacturing
These processes involve breaking down the mined ore into smaller fragments and separating it based on size. Let's explore the crushing and screening …
اقرأ أكثر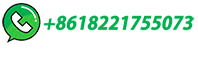
Refining crude oil
How crude oil is refined into petroleum products. Petroleum refineries convert (refine) crude oil into petroleum products for use as fuels for transportation, heating, paving roads, and generating electricity and as feedstocks for making chemicals.. Refining breaks crude oil down into its various components, which are then selectively …
اقرأ أكثر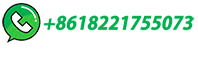
Copper Metallurgy
In the electrolytic refining process, the anodes and cathodes are, individually, the copper anodes produced in pyro-refining and 316 L stainless steel sheet or copper starting sheet, and the electrolyte (58–62 °C) is an aqueous solution of sulfuric acid (150–200 g/L) and copper sulfate (copper content 40–50 g/L).
اقرأ أكثر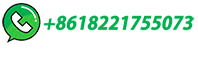
Gold Refining Methods
How to Use Iron and Carbon to Refine Gold. Iron is used to remove arsenic, antimony, sulphur. The pot is stirred briskly with an iron rod for a few minutes. Antimonides, arsenides, or sulphides are formed and separate from the metal. Carbon is used to assist iron to melt and to remove oxygen from bullion.
اقرأ أكثر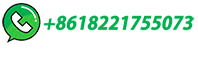
From Ore to Iron with Smelting and Direct Iron …
Smelting Reduction. Figure 2: The smelt reduction vessel (SRV) is the core technology component of the Hismelt process. Source: RioTinto While years of ironmaking technology innovations have …
اقرأ أكثر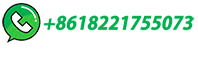
Edison and Ore Refining
Edison planned to process 1200 tons of iron ore every twenty hours. The plant had three magnetic separators that could produce a total of 530 tons of refined ore. ... Iron ore rock crushers used in Edison's iron ore refining business. In 1892, Edison shut down the mill in the hopes that replacing some of the equipment would improve …
اقرأ أكثر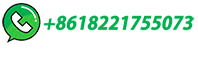
What is Smelting
In the smelting process, iron ore is heated, leading to the separation of iron from impurities. This iron-carbon combination forms the basis for the production of steel. This versatile material has revolutionized modern industry and construction. ... Casting equipment, including molds or castings, tongs, and other handling tools, are …
اقرأ أكثر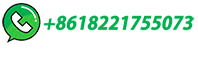
Iron processing
The partially reduced ore is then smelted in the second unit, and liquid iron is produced. Smelting-reduction technology enables a wide range of coals to be used for iron …
اقرأ أكثر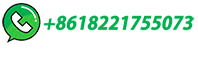
Gold Refining Process
To present the essential points of all methods of gold refining commonly practised, as well as those of historic interest," was the author's purpose in this volume. The fifteen chapters of which the book consists deal with the Simpler Methods of Early Days; Amalgamation Process; Refining with Oxidising and Chloridising Agents; Sulphur …
اقرأ أكثر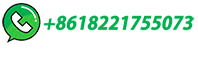
Hard Rock Lithium Processing
important lithium ore mineral. A typical run of mine ore can contain 1-2% Li 2 O, while a typical spodumene concentrate suitable for lithium carbonate production contains 6-7% Li 2 O (75% - 87% spodumene). Higher grade concentrates with 7.6% Li 2 O and low iron content are used in ceramics and more demanding industries.
اقرأ أكثر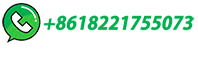
Iron processing
Iron processing - Ores, Smelting, Refining: Iron ores occur in igneous, metamorphic (transformed), or sedimentary rocks in a variety of geologic environments. Most are sedimentary, but many have been changed by weathering, and so their precise origin is difficult to determine. The most widely distributed iron-bearing minerals are oxides, and …
اقرأ أكثر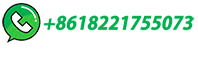
Recovering Gold through the Froth Flotation Process
Along with mechanized mining equipment, froth flotation dramatically improved the efficiency of gold mines. Thanks to this process, miners and refiners are able to extract quality minerals from ore at lower grades than has been previously possible – making it perhaps the most important mining industry innovation of the 20th century.
اقرأ أكثر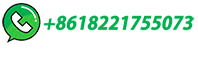
iron ore refinery processing plant | Mining & Quarry Plant
Iron ore mining process flow chart … gold ore refining process plant, gold ore refinery flow chart. In this process, many gold mining types of equipment are used, … chrome ore processing spiral plant – Mineral Processing …
اقرأ أكثر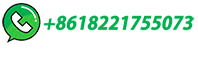
Steel Production
Even though equipment is improved and higher production rates can be achieved, the processes inside the blast furnace remain the same. ... The blast furnace uses coke, iron ore and limestone to produce pig iron. Coal traditionally has been a key part of the coke-making process. The coal is crushed and ground into a powder and then charged into ...
اقرأ أكثر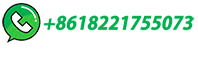
What is Smelting
In the smelting process, iron ore is heated, leading to the separation of iron from impurities. This iron-carbon combination forms the basis for the production of …
اقرأ أكثر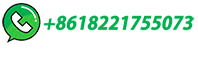
Pig Iron Manufacturing Process
At any place where there is a market demand for steel, and pig iron can be made in the electric furnace at a profit, the steel ultimately produced would be cheaper, if made by the electric reduction of iron …
اقرأ أكثر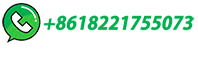
Iron processing | Definition, History, Steps, Uses, & Facts
The six main steps of iron ore processing
-
- Screening. We recommend that you begin by screening the iron ore to separate fine …
- Crushing and stock piling. This step involves breaking up the iron ore to obtain an F 80 …
- Feeding the crusher (Reclaim) The surge pile allows a constant supply of material to be fed …
- Grinding. The primary grinding mill grinds the material before it undergoes spiral gravity …
- Spiral gravity separation. The gravity separation feed range is approximately 30% solid …
Platinum Group Metals
MRT™ Platinum Group Metal Refining Systems have Proven to be Very Advantageous for a Large Number of PGM Refining Applications. Examples of the application of MRT™ for platinum group metal refining …
اقرأ أكثر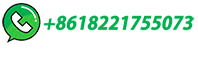
From Ore to Alloy: Navigating Ironmaking in Modern Steel …
Iron ore, primarily hematite and magnetite, serves as the raw material for ironmaking. Mines worldwide extract these ores, which are then processed to remove impurities and …
اقرأ أكثر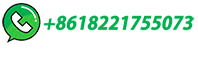
Guide to Modern Smelting Processes
Early iron smelting was accomplished using charcoal- fueled furnaces known as bloomeries. Iron's Impact: Iron tools and weapons were harder and more durable than bronze, leading to transformative changes in agriculture, construction, and warfare. Iron was the foundation of empires like the Roman Empire, as it enabled the construction of
اقرأ أكثر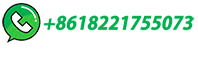
Iron Processing | Equipment, Process Flow, Cases
The former mainly selects magnetite ore, and the latter is mainly used for sorting hematite, mixed iron ore and weak magnetic ore. 6.2 Magnetic separation – cation reverse flotation process The grade of …
اقرأ أكثر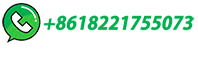
Sustainable Lithium Extraction: How is Lithium Mined and …
Lithium mining from ore deposits combines traditional mining techniques, including drilling, blasting, and excavation. Once the lithium-rich ore is extracted from the ground, it undergoes physical separation processes to remove impurities, concentrating the valuable lithium minerals. What is the process of mining lithium from evaporating ponds?
اقرأ أكثر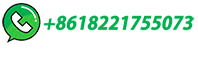